How to make our walls and HVAC system more efficient?

Hi,
My wife and I are building a new row house on an existing foundation of an old row house in Pittsburgh. We hired an architect and subsequently a very reputable builder to renovate the row house. The structure has only one shared wall (we own and adjacent city lot and plan to have a courtyard so the home won’t have a shared wall on both sides like most row houses. As such, we only have one wall to run ductwork and plumbing up and very little wall space to insulate. The HVAC sub has advised that we will need two furnaces and condensers with the 2nd set being on the third floor due to the lack of wall space (we have no interior walls that run up all three floors and we plan to have 6 zones in the house (lots of duct work).
I started thinking about the $4k plus cost of the unnecessary hvac equipment and started to wonder if there was a way to better insulate my structure such that i can use two walls for ductwork thereby allowing for only one furnace and condenser. The saved mech costs could help pay for the additional rough carpentry and insulation, giving me a much more efficient home for little extra cost.
Here is the catch – the interior of the home is about 16’10” wide and 72′ deep. So losing interior space on the two short walls – no big deal. Losing it on the long wall – tough to swallow. Further complicating things the area where we are building does not have the best expertise for green building, so complex solutions. Adding to that – while I am extremely happy with my builder and architect, neither of them are extremely knowledgeable in green solutions. As such, I need to find a solution that not only improves the envelope of my home and gives me a second wall to run ductwork, but I need a solution that has “low risk” implementation such that the framers doing my house are not scared off by “complex” solutions or bid overly conservative bc it’s a new thing for them.
I plan to hire a local energy consultant to help size our HVAC once we determine a more appropriate wall solution, but I currently need to determine what that best wall solution is. As I said, my builder is good, but not green, so they haven’t proposed a solution that provides the best ROI while being more green, and they are reluctant to price out 4-5 solutions because of the time involved without charging me extra, which I understand. I haven’t spoken with my architect yet, but I also flip houses on the side, and so i figured I would determine the solution that is easiest to implement.
The way I see it, I have a few options, and the short exterior walls are the easy solution:
1. Short exterior walls – The easiest solution appears to be to lay 1-2″ of interior rigid insulation inside my 2×6 walls which will eliminate the thermal break associated with my framing. I am in zone 5 in the US and need 2″ of exterior insulation to avoid moisture accumulation so using exterior sheathing would require verticle strapping, and the row house will be built up to the property line on the sidewalk, so i’m not sure what an additional 2″ of external sheathing would do to the look of the home. I also don’t know if I would need my builder to install a drainage plane. For those reasons it seems like interior rigid insulation with dense pack cellulose makes the most sense. If I am wrong, please let me know. That would give me R25-30 on my two short walls with no thermal break.
2. Long wall is harder because I don’t want to lose much interior space and I need to be able to run ductwork up this side as previously mentioned. The way I see it, I have four options –
a) double studded 2x4s with no spacing (or 1″) between walls. I only lose 2-2″ of interior space and have no thermal breaks. I can run 4″ ductwork up the interior wall and still have 4″ of dense pack cellulose behind it providing R-16 insulation, and almost R30 insulation where there is no ductwork or frame material. This seems like the easiest solution to implement, but i lose 2-3″ of interior space across 72′ and 3 floors.
b) same as above but I’ve read that there is a way for the outer 2×4 wall to extend out over the foundation. This would allow more spacing between walls for more insulation, but I don’t know the details around doing something like this. If it’s an easy implementation, perhaps this is the way to go.
c) 2″ (or more) of exterior foam sheathing with verticle strapping and a drainage plane. This is easier as this long run side of the home isn’t adjacent to the public sidewalk. The builder already pitched a 1.5″ closed cell + 4 inches of bat insulation pitch so they should be familiar with implementing an appropriate dry-inward wall associated with exterior sheathing.
d) build a larson truss – This really accomplishes the same thing as B i think right? I just don’t know which is more difficult to implement.
The fourth long wall will remain a 2×6 wall with dense pack cellulose and a fair bid of ductwork. The wall isn’t shared with the neighbor and there is a slight gap (1/2″ or so) between my home and the neighbors, but I am stuck with a 2×6 for this wall.
So, am I missing some other easy/more cost efficient implementation for this long run wall? Any help would be appreciated.
GBA Detail Library
A collection of one thousand construction details organized by climate and house part
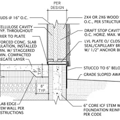
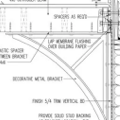
Replies
Have you considered using a water based system for heating and cooling? This would cut down on the amount of vertical chase space required, allow for one set of HVAC units, provide for better zoning, etc.
I believe there are fan coil units available now that could make a water based system competitive.
Are you suggesting that I could keep a blower on the third floor but run water lines to that floor instead of ductwork and just have a blower up there?
I"m familiar with the idea of getting heat from a water based system using a high powered water heater (tank or tankless), but how do you get cool water without doing geothermal?
Three options for avoiding ducts:
1) Do hydronic heat with panel radiators, and, completely separate, a mini-split ductless air conditioning system.
2) Do heating and cooling with mini-split ductless systems that can heat and cool.
3) Use a heat pump system to generate hot or cold water to use for heating and cooling in mini "fan-coil" units that are like mini-split heads but smaller. Chiltrix makes both the heat pump and nice fan-coil units.
http://www.chiltrix.com/
I recommend getting your energy consultant on board early in the project.
I just got off the phone with my energy consultant. I am bringing him in. My wife would never ever live in a house with min-splits on the walls, and anythign I have tried to price out with a Hydronic system or mini-splits costs significantly more than the current design IF i can get it back down to one furnace and one condenser (17 SEER two stage compressor, 96% AFUE 2 stage, multi speed fan furnace).
As Charlie points out, if you have ground or roof space a water based heat pump might be a good solution.
Your climate in Pittsburgh always seems so temperate, at least to me up here in State College; when it's snowing here it's raining in Pittsburgh. My gut says an air source (air-water) compressor would work great. There are others on GBA with first hand experience who can chime in on that. (I have water-water geothermal.)
On the mini-split wife issue, well I understand, having lost the battle to have panel radiators in our home. However, in retrospect, if I had done my homework earlier I think we could have implemented them in a more benign fashion and they wouldn't have been so objectionable.
Folks on GBA love mini-splits and I have come to believe there is good reason. I sometimes think about how we could have designed this house to incorporate mini-splits in less prominent locations. You are at a good stage with your architect and energy consultant to make that happen.
Matthew,
You've been given good advice so far. Ductless minisplits or ducted minisplits are probably the least expensive solution.
For more information on the Chiltrix and similar equipment, see Air-to-Water Heat Pumps.
The bulk of your long post has to do with questions about basic design issues (where to put a chase to hide your ductwork). We can't solve issues like that here -- especially without a floor plan. These basic design issues should be addressed by your architect.
The fact that you don't trust your architect or builder, because "they aren't knowledgeable about green solutions," is worrisome. You can't enter a construction project like this one without trusting your architect and builder.
I don't recommend that you try to put ducts in exterior walls, by the way, with only 4 inches of cellulose between the duct and the wall sheathing. That's a bad idea.
-- Martin Holladay
Thanks, I am going to explore the chiltrix solution. I guess if my wife refuses to install the wall/ceiling units I can still do a ducted solution. I sent it to my HVAC guy and will do so with my energy consultant once I hire one.
So back to the insulation topic - if I can implement a ductless solution, And want a simple way to get close to R-30 without thermal breaks - that I should just put 2" of interior foam over my 2x6 walls that are packed with dense pack insulation?
Without first running an AGGRESSIVE Manual-J load calculation you can't really specify the right equipment. If the loads are within the range of a ducted mini-split, that can work well, and is better suited for low loads than most gas-burners. A code-min R20 + R5 c.i. ~1200' house that's reasonably air tight with R15 foundation insulation and code-min windows and a 15% glazing /floor ratio would typically come in at ~15,000 BTU/hr, for heating, and a comparable amount for cooling. If one of the 72' walls is a common wall with conditioned space on the other side you're probably looking at less than 10,000 BTU/hr for both heating & cooling, depending on how much glass, and what direction it's facing. Most split system1 or 2 stage cooling doesn't come any smaller than 1.5 tons, and it's hard to find a gas furnace under 28,000 BTU/hr. You don't say how many square feet per floor, but indicate they're not all the same size.
Zoned ducted systems broken up into 6 zones have a huge problem with having sufficient air flow when a single zone is calling for air conditioning unless you oversize the hell out of the air handler &/or add some bypass ducting, etc. That makes it louder than need be, and turns it into a potential efficiency & reliability nightmare.
Floor mounted mini-splits work fine for many people who can't stand looking at wall-blobs, but are OK with the look of hydronic convectors, panel radiators, or wall-furnaces:
https://www.greenbuildingadvisor.com/sites/default/files/Floor-mounted%20indoor%20unit.jpg
Ceiling cassettes are another option, but it's hard to find ceiling cassettes that modulate to a suitably low level for your low loads.
Mini-splits are usuall quieter than the typical oversized ducted HVAC systems too. A 1-ton mini-split is quieter than most refrigerators when running at low to mid-speed (where they run 95% of the time if right-sized for the load).
A Chilltrix solution is great if it meets the loads, and you have competent design help & local support. Each solution is semi-custom, and there is some design risk that you would not have with a mini-split.
If you are going for a high-R building envelope it's likely that even the smallest gas furnaces and split systems will be more than 2x oversized.
A 2x6 16" o.c. cellulose studwall with typical interior & exterior options comes in at about R14 whole-wall after thermal bridging. To hit R30 whole-wall would require 3" of interior polyiso, and there may be special detailing required around the thermally unbroken floor joists, band joists etc., which are thermally bridging the foam. It's far better to put the foam (or rigid rock wool) on the EXTERIOR, where it puts all of the structural wood inside the foam layer. If 3" of exterior polyiso or 4" of exterior rigid rock wool is not possible, for a 2x6 wall in Pittsburgh (US climate zone 5) you need a minimum of 1.5" of exterior polyiso, or 2" of exterior EPS or rigid rock wool for dew point control on 5.5." of cellulose. That's well shy of R30 whole-wall, but it its what it is. If you drop back to code-min 1" exterior polyiso you would need a Class-II vapor retarder on the interior (2-mil nylon such as Certainteed MemBrain, or half-perm "vapor barrier latex" primer), which would be somewhat less resilient- R8 or more on the exterior would be preferable.
Thanks for the detailed answer Dana. I hadn't considered the thermal break at the joist area for interior insulation. I will rethink the interior insulated panels for the short walls.
After doing some reading comparing the costs of a double studded 2x4 wall compared to external panels - it seems as though double studded 2x4 walls on the two short walls may be the easier & more affordable solution.
I don't believe that is possible on our long wall since we want to build out and not in (foundation already exists).
Is there any reason not to do blown in celluslose in a 10-12" double studded walls on the short walls (North and South facing) and just 2-3" of external panels on the long wall (E facing)?
Also - the western facing "shared" wall is like 90% shared and 10% exposed. That 10% will be a 2x6 wall with no practical way of providing additional insulation.
I have uploaded the floorplan section of my CDs for reference. Please note though - framing is currently spec'ed for 2x6s. The CDs are being amended as we were originally retrofitting an old home, but reframing costs were the same as new build due to extremely uneven floors.
I would also add that the wife is already changing her mind about the chillix or any min-split system due to the way they look. ugh. opens all sorts of new questions - traditional force air vs chillix ducted, etc...
so thankful that I am hiring an energy consultant that will do the manual J calcs and help me spec a system.
Make sure the Manual-J reflects the actual U-factors as you change up the insulation schemes, and make sure that it has aggressive assumptions about ventilation & infiltration rates. With non-standard construction the consultant will probably need to calculate the U-factors, and since you have access to the framing plan you can assess the framing fraction fairly accurately to get fairly precise U-factors.
Using heat recovery ventilation can make a real difference in the design condition load numbers. In high-R houses high nominal infiltration & ventilation assumptions can dominate the load numbers.
If the ~65' shared wall is west facing, it means most of the windows are facing east, which can lower the peak cooling load compared to west facing windows, but it can still be a fairly high peak if it's not shaded by a nearby building. Reducing the window sizing or even using low-SHGC windows may be in order if there isn't much shading factor on the east side. This is sometimes only an issue for the upper floor, but some shade analysis is called for.
Completely follow on the U-factor for framing, but not sure I follow on ventilation and infiltration rates.
All Three of the non-shared walls have a lot of windows. The north and south have the most percentage wise, the east the most in absolute terms. We aren't changing window design.
The majority of the east and south windows will have significant shading for summer time heat. Being in Pittsburgh and having so many windows - my concern is hearing efficiently more than cooling.
So, I have been doing some research on the Chiltrix system and it seems like there is some skepticism on the efficiency numbers. Also, I'm not sure if I will be able to find an installer in my area that has used the system, but I am looking.
https://www.greenbuildingadvisor.com/articles/dept/musings/air-water-heat-pumps
The default settings of many load calculation tools for air leakage are unrealistically high, and if they are assuming ASHRAE 62.2 ventilation rates WITHOUT heat recovery it adds quite a lot to the heat load numbers.
In a high-R house even an unshaded 12 square foot U0.18 top floor bedroom window facing east can be a serious comfort problem in June/July, when the sun rises earlier than the occupants. (Don't ask me how I know this! :-) )