How to Make Minisplits Work Better

Hello! I’m hoping someone here can help me figure out how to make our heat pumps work better for us.
We are in eastern Massachusetts, and in April 2020 we had Hyperheat minisplits installed for both heating and cooling. We had our oil boiler removed at the same time (it was failing and not repairable), so we’re all in on the minisplits. They have worked great for cooling…heating not so much. When it gets into the 20s or below, it can be uncomfortably cold (temps getting below 60 in corners when the thermostat is set to 68 or higher), especially in the living areas. And our electric bills seem very high, though I don’t know how much of that to attribute to the minisplits and how much to water heating (solar HW w/electric backup).
From reading this site, I guess our system is oversized. We did what the installers suggested – a unit in each room except the bathrooms, tied to two outside compressors. I also think our insulation isn’t great (in particular, our old radiators are recessed into the walls, and there probably isn’t much insulation behind them). I’m not sure how to fix that, and frankly I’ve lost faith in contractors knowing how to do things right if the homeowner doesn’t :(.
I don’t want to go through another winter being cold in our house and wasting money. I’m at a point where I’m considering getting a woodstove just to keep us warm. Is there anything we can do to make the minisplits work better?
Thanks for any help!
GBA Detail Library
A collection of one thousand construction details organized by climate and house part
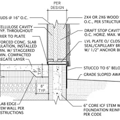
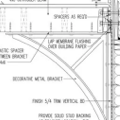
Replies
Have you had an energy audit with a blower door test? If so what was your ACH50 number?
Seems like there is a mass saves program that more or less covers the cost.
What is the temp of the air your units are blowing out into the room and what is the temp of the air going into the units?
Seems to me if you units were oversized the symptoms would be cold and clammy in the summer and no trouble keeping warm in the winter.
Walta
No blower door test. We have an old asbestos pipe in the basement that we were recommended to leave alone because it was stable. Mass Save won't do a blower door test with asbestos in the house. We have had all the Mass Save recommended insulation done (blown into the walls).
I don't know what the temp of the air was in the winter, unfortunately. Could you tell me how to use that information so I can try it in the fall?
Although air-source heat pumps are very efficient, and can work efficiently and effectively in cold weather, unfortunately they are not a good match for poorly insulated and/or poorly air-sealed homes, because if they have to work too hard the coils frost over, and require electric resistance heat to melt the ice. They are an excellent match for well-insulated and air-sealed homes, so the best thing you could do is to insulate and air-seal.
Regarding temperature set points, a common complaint is that the room temperature is often lower than the thermostat setting. The simple fix there is to use a higher temperature setting. Don't worry about the number you set it to; it could be labeled "A, B, C" and still work fine.
Is that true in less severe climates? We also installed a hyperheat ducted minisplit for upstairs. We have not given up our natural gas boiler/radiator system yet, but would like to someday (why we got the hyperheat and sized it for heating rather than cooling demand). But our house is not at all airsealed/insulated, and really cannot be without a gut overhaul (stucco directly on diagonal plank sheathing, plaster walls). (We did airseal our half of the duplex's attic with closed-cell foam and then insulated with rockwool and polyiso strips on the rafters)
we are in 4a.
incidentally, so far the a/c is working fine, we just tried it for the first time when we had 90+ degree days and lows of 70.
This critique of air source isn't much of a real problem- so what if the unit defrosts? With a ducted system, you could run resistance for a few minutes per day to cover it if you even notice it. I have a ducted hyper heat in a leaky zone four house and never notice defrost. The efficiency hit is small too, while the heat pump is worlds more comfortable than the furnace was. All leaky houses are uncomfortable vs well sealed and insulated homes, the heat source doesn’t matter much.
Paul I don't have first-hand experience with the issue but I have heard from many other design and construction professionals that it's a big problem. A few past clients with leaky homes were not happy either, so I no longer recommend ASHPs as the sole heat source for those types of projects.
For ductless, I agree. For ducted systems, this is easily designed around: when unit defrosts, electric resistance temporarily kicks in. For the user, it's the same experience as a furnace: warm air comes from vents.
Thanks. The house has had cellulose blown into the walls, and has relatively new windows (mid 2000s). Is that enough? Is there an easy, non-invasive way to improve it? As for air-sealing, I'd like to do that, but honestly I don't even know where to start (and frankly we don't have time to research and DIY it).
We tried turning up the temps once or twice, and that did increase the room temp somewhat, but I hate to think what our electric bills would be like if we did it all winter.
Seems to me soon or later you will pay to remove the asbestos because you are going to disclose the asbestos before you sell and the buyer will demand its removal or a similar amount as a discount either way you are paying and every year you wait the price goes up as the regulations get stiffer and more expensive while you live with the increased health risk. I see no reason to wait have it done while you are on vacation.
Once it gets cold consider inferred photography it will show you where the energy is leaking in and out. You can rent the equipment at some Home Depots.
Walta
I agree with Walter that infra red photography could quickly and accurately show you the energy leaks. You can purchase a FLIR brand infra red attachment for your iPhone or Android phone for as little as US $300. Use it both inside and outside the house. You can scan a room for trouble areas and then take the photo once you find one. Search this website for articles on thermal photography.
Ok, that's probably worth doing. Will look into the cost of that.
Theorajones,
It seems to me like there are 2 different scenarios in which you are not getting the warmth you desire.
Scenari0 1: the heat pumps cannot keep up with the total heating load.
Scenario 2: the heat pumps are not delivering the right amount of heat to the right places.
If someone can monitor the energy usage of the pumps and the temperature data (as Walta suggests), then compare to the ratings, it may help tease out which scenario it is. My guess is it's likely to be scenario 2 unless the installers messed something up. At least if we're talking well above 0F, such as 20F as you say.
I actually do think the heating source matters for comfort for a few reasons. One is the set point (a thermostat issue more than a heat source one i suppose). If the heat pump thermostat is in the head (as they usually are) it may think it's warm enough when, on average, it's not. As Mike said, one solution is to simply ignore the set 'temp' and just treat it like a 'warmer or cooler' dial. Another might be to install a remote thermostat in the cooler regions of the room.
Another reason a heat source might matter is due to radiant temperature. Old baseboards were placed on exterior walls of rooms to increase the temperature of the walls and mix warm air with the cool air leaking in. If the walls are colder, a human body will feel colder, regardless of the air temperature.
Two possible remedies to this might include ensuring you have good mixing of air so the warmer air can reach the cold corners. Another remedy is to see if your cold corners are due to air leaks and missing insulation, etc. A thermal camera and blower door both are good tools for this. Perhaps even a simple point and shoot IR thermometer and a smoke stick as a starting point.
Thanks! I'm not sure how to monitor the energy usage of the pumps and the temperature data. Walta mentioned measuring the incoming and outgoing air temps, but I don't know how to do that exactly, or what to do with the resulting data.
Are remote thermostats something I'd need to get from our installer? Sorry, I'm afraid I am pretty clueless about all this.
I was recently told by a well known energy consultant that hot air heat pumps deliver low temperature air and do well in tightly sealed homes. If yours is leaky, they are struggling to deliver the necessary btu's.
A heat pump, properly sized, puts out the same BTUs as the same sized furnace. A leaky house that struggles with a heat pump will struggle with a furnace or boiler too.
For what it's worth, we weren't cold when we had our oil boiler/forced hot water system.
Exactly! This seems like a distribution problem - you probably have much more heat than needed, it’s not going to the right places. If these ductless heads were heated with a boiler (they make ductless heads that connect to boilers too), the same issues would persist.
On the other hand, had the replacement been an air-to-water heat pump, the baseboards could have been used by that.
A list of the equipment (exact model numbers of both the compressors and indoor units), as well as a room by room Manual-J load calculation would be useful.
How are the heads in the cold rooms behaving in winter? Are they blowing 100% of the time, or are they cycling on/off? Hand held remotes, or wall remotes? Unless you have wall-mounted remotes with the room temperature sensor in the remote, the head is only sensing the room temperature by the temp of the intake air at the head, thus if it's not blowing, it's not sensing, resulting in large temperature swings, often with short-cycling. Properly sized they should be blowing nearly 100% of the time when it's in the 20s or cooler outside.
Even when properly sized it's normal for there to be temperature offsets between the average room temp and the temp sensed at the head due to stratification. This offset increases when it's colder outside. If the head isn't undersized for the zone, the solution is to just bump up the temp reading on the remote, or buy a wall remote with an internal temperature sensor, mount the remote on an interior wall away from window drafts, and set it up to respond to the sensor in the wall remote.
Heating with electricity, even with properly sized ductless will usually be somewhat more expensive than heating with a gas fired boiler at recent MA utility rates. Most Eversource/Nat'l Grid customers in eastern MA are paying $0.28-$0.30/kwh for electricity and $1.75- $2.00/therm. With a multi-split that tests at HSPF 10 (10,000 BTU /kwh) delivering one million BTUs (MMBTU) uses 100 kwh of electric, at a cost of $28-$30/MMBTU. To deliver the same amount of heat a mid-efficiency 85% gas boiler burns (1,000,000/85,000=) 11.75 therms, at a cost of $20.50- $23.50/MMBTU.
If the ductless system is 2x or more oversized for the system it simply can't hit it's HSPF efficiency numbers due to excessive cycling losses.
If the wall radiators are in fact finned convectors in a sheet metal cabinet it's usually possible to insulate the back of the cabinet (closest to the exterior wall sheathing) with 3/4" or 1" foil faced polyiso (fire rated versions such as Dow Thermax preferred.) An empty, un-insulated exterior wall cavity with plank sheathing, wood siding, and plaster/lath interior runs about R4, so even 3/4" polyiso would cut the heat loss in half. If the radiators are cast iron a rigid insulation approach is usually not possible, but it may be possible to slip in the aluminized bubble pack type radiant barrier (~R2) which is still better than nothing.
Radiators on an upper floor or finished attic cut into kneewalls can be insulated from the attic side of the kneewall. (I installed 3" of reclaimed rigid polyiso on the crawl-attic side of a radiator in my own top floor.)
If you have some old oil billing slips from prior year, run a fuel-use based load calculation to better estimate the whole-house heat load, and the oversize factor of the ductless system. See:
https://www.greenbuildingadvisor.com/article/replacing-a-furnace-or-boiler
Thanks! I have posted what I have for our system in a separate comment below. We have remotes but we don't use them and I don't even know where most of them are. We use online controls mostly. I assumed the units themselves were sensing the room temperature.
I think the units were running most or all of the time during the winter.
We never did a load calculation and as far as I know the installers didn't either, or if they did they didn't mention it to us. I will try to find some old oil bills. I knew that our electric bill would go up significantly when we switched over. Just not sure how to determine what's normal for a system like this. Our biggest month since we got the minisplits was Jan 2022, in which we used ~2800 kWh. That said, we do also have the solar hot water, an EV (infrequently charged), and we are heavy tech users.
I appreciate the insulation information, though it also makes my brain hurt. Technical building details are not my thing and I don't have the time and resources to devote to learning about them. I'm going to have to hire out any insulation work that happens.
Your complaints and concerns have been posted on GBA previously by several other people in recent years who installed cold climate heat pumps in there home, notably in northern climates.
Its typical to see a heat pump in AC mode functioning well and more economically than in the heating season. When it's the heating season, it's typical to see people complain about comfort and energy consumption of their heat pump. The cause is poorly insulated/sealed home and/or poorly selected and installed heat pump equipment.
How many square feet is the home?
How many floors?
Is the home a simple shape or more complex and sprawling?
Two outdoor units and multiple indoor heads, how many heads?
Although there will be someone on this website to discredit my statement, multi-split setups tend to be a tough pill to swallow.
The cons are:
1) Many pieces of expensive equipment to maintain after warranty is gone, not to mention warranty may not cover labor or refrigerant replacement.
2)Complexity. Contractors lack qualified personnel to size, install, and troubleshoot these systems.
3) Increased electricity usage caused by long refrigerant lines, multiple indoor heads and outdoor units running sub-optimally.
4) Comfort issues due to poorly performing home and/or hvac equipment.
Thanks! I posted information about the system and house in a separate comment below. Would appreciate your input on whether the system is oversized. We do have some pretty long refrigerant lines too, no one mentioned that would be an issue. I feel stuck with this system, though I'm not sure we had a lot of choice. Getting a new oil system seemed ridiculous, and bringing a gas line to the house was cost-prohibitive. I'm hoping we can make what we have work.
Two outdoor Mitsubishi multi-split condensers imply 2x24k or greater. This is likely oversized for a regular Eastern mass house, although OP didn't give dimensions or construction of the house.
Likely culprit is short-cycling and poor hot air distribution. Short-term fixes are running only 1 unit at a time, turning up the "temperature", ceiling fans in reverse mode. Maybe standing fans for air distribution.
Thanks. I posted info about the house and system in a separate comment below. It is a pretty typical Eastern MA cape, mid-century, wood construction. When you say running one unit at a time, do you mean one indoor head or one compressor outside? Or trying to run one head per compressor so it's not a multi-head system anymore?
Unfortunately we don't have the ceiling height for ceiling fans.
More info about our system and house:
~1450 sq ft conditioned, consisting of two rooms upstairs, three downstairs, and one basement space that's semi-finished. It's a cape, so a pretty simple shape. There are two outdoor units, each with three heads connected to them.
Here's what I have for the units installed (copied from the invoice):
MXZ-3C24NAHZ2-U1 Outdoor Unit
MSZ-FH12NA Indoor Unit
Mitsubishi GL-Series MSZ-GL09 indoor unit
Mitsubishi GL-Series MSZ-GL09 indoor unit
Mitsubishi MXZ-3C30NAHZ2-U1 Outdoor Unit
Mitsubishi GL-Series MSZ-GL09 indoor unit
Mitsubishi GL-Series MSZ-GL09 indoor unit
Mitsubishi GL-Series MSZ-GL09 indoor unit
I strongly recommend doing a room-by-room load calculation, using the purpose designed heat pump sizing tool developed by the Better Built Northsest utility consortium.
It's free (but you do have to share an email address to open the free account), and it's easy enough to use that even HVAC installers can use it! :-) (Really, they have
excuse not to. ) See:
https://betterbuiltnw.com/hvac-sizing-tool
A 1450 square foot 2x4 framed insulated cape with mid-century clear glass windows + clear glass (no low-E) storms built over an uninsulated basement or unvented uninsulated crawlspace would typically come in at or under 25,000 BTU/hr @ +10F (a typical coastal eastern MA outside design temp) or even +5F (central MA) , which is the approximate capacity of just one MXZ-3C24NAHZ2:
https://ashp.neep.org/#!/product/26170/7/25000///0
... well within the capacity of the MXZ-3C30NAHZ2
: https://ashp.neep.org/#!/product/26173/7/25000///0
The whole-house heat load at +47F is likely to be ~9000 BTU/hr, which is less than the minimum output of either of those compressors @ +47F, which means even with just one MXZ-3Cxxx the compressor will by cycling on/off any time it's above (roughly) freezing. But you have two.
There is almost no bedroom in a Cape that can use the full ~10-11,000 BTU output of a GL09 head when married to an MXZ compressor- most would be a quarter that or less. Unless the room's design load is at least on the order of half the max output or more it's likely to run into comfort issues related to oversizing. Even the GL06 is a bit oversized for most smaller bedrooms, but it can at least throttle back to about 4000 BTU/hr (merely ~2x the design load of an average bedroom.)
It may be possible, or worthwhile to consolidated the loads of 3-4 rooms and use a single right sized ducted cassette to heat them. The starting place is to run the room by room loads, then figure out if there is a way to reasonably duct & combine them. Some times utilizing the mini-attics behind kneewalls can work, but many times not.
For reference, I live in a 1920s 2x4 framed 1.5 story bungalow with ~2400' of conditioned space+ 1600' of insulated (but no directly heated) basement, mostly original wood-sash single-panes + 1980s vintage clear glass storms. The design heating load at my house is ~37KBTU/hr @ +5F. Most (but not all) 1960s Capes would have about the same window/floor area ratio as this house, and comparable BTU/square-foot load ratios. Those with "Mid-Century Modern" pretensions might have a lot more glass, yielding higher heating & cooling loads, but it wouldn't be 2x.
>"We use online controls mostly. I assumed the units themselves were sensing the room temperature."
If you're controlling it with an online app it means the Wi-Fi adaptors are already in the head, which can make it either easier or harder to use with the range of available wall sensors. Some functionality will usually have to be given up. Yes, the units internal sensors are sensing the room temperature, but they can only sense the temperature of the intake air, not the average room temp. There are multiple third party Wi-Fi thermostats that can work with the GL series heads, as well as Mitsubishi's "Kumo Cloud" dumber remote temperature sensors rather than at wall thermostat. Using just a wi-fi remote temperature sensor, may be more compatible with your current online setup than a fully functional wall thermostat. It's impossible to cover all the variations and software layers here, but if it isn't using a temperature sensor other than the one inside the head there will always be offsets between the average room temperature and the temperature the head is sensing. A remote sensor or thermostat should resolve most of the comfort issues, but won't do too much for the efficiency hit from oversizing.
Do you have kneewalled rooms up stairs with head-banger sloped ceilings? Those are usually hard to air seal adequately on the first pass, but if air is leaking out of the top of the house those rooms would normally be warmer in winter than the rooms below. If the foundation, foundation sill & band joist aren't well sealed from outdoor air it makes for cold floors in the first floor rooms, which creates an even larger temperature offset for a high-wall ductless head. I believe MassSave will still subsidize insulating & air sealing with a couple of inches of closed cell foam on the foundation sills & band joists, but not the basement walls.
In addition to MassSave, the Massachusetts Clean Energy Center runs various subisidized programs (often limited in scale), and if you're looking to pull the gas meter you might be able to participated in their next Decarbonization Pathways pilot. They are currently planning on decarbonizing 30 homes in the next round, though the sign up period is still pending (supposedly happening this month.)
https://www.masscec.com/decarbonization-pathways
https://www.masscec.com/blog/2022/05/02/masscec-will-seek-homeowners-receive-complimentary-home-decarbonization-services
If you want to be notified of when applications are going live, sign up here: https://www.jotform.com/form/221085167380151
This program will provide a lot more serious retrofit analysis, including blower door testing, etc and develop a path forward based on the condition of the house now. You have probably already spent some of the bigger chunk money (on the ductless systems), but doing a much more serious job on the insulation & air sealing will likely fix most or all of your comfort issues.
I'm probably shooting myself in the foot here, since I'm hoping to get some goodies for ditching the gas burner in favor of low-temp hydronic heat pump to cover half the heating zones (which would be hard to adequately retrofit with ducts, with several rooms currently heated with radiators with loads too small for ductless).
1450 sqft, including basement space? I would be surprised if your design heat loss even reaches 30k btu. Thus your 54k combined btus almost certainly very oversized. There's not a lot you can do at this stage. As I suggested previously - perhaps you can try operating only one outdoor unit and their attached indoor units at a time. I don't know if that's feasible for your living space usage patterns.
I bet you have nearly enough heat pump for two homes! but a guess is worthless.
Besides living with it as is, you could hire out a Manual J as said earlier, hire someone independent of the situation to do the calculations for you. Make sure they are conservative in their math. Armed with knowledge, you may be able to strong arm the HVAC company into a remedy. Assuming the equipment is oversized for your home.
You'll probably be uncomfortable even after resizing the equipment, typical of an average quality home retrofitted with heat pumps in a cold climate and as far as electrical consumption any efficiency gained back will be modest at best. There is no magic bullet just marketing hype.
Is humor acceptable? HVAC Taken: "I don't know who you are. But, I do know what you want. If you are looking for a properly sized heat pump, I can tell you it will cost less money than already spent. Dana has a very particular set of skills, skills acquired over a very long career, skills that make him a godsend for people like you. If you let your oversized heat pumps go, that'll be the end of it."
>"Dana has a very particular set of skills, skills acquired over a very long career, skills that make him a godsend for people like you."
It may come as a surprise to some, but I've never done HVAC for a living. Having experienced first hand some of the sloppy practices within the industry I've educated myself on how to do it right.
The first hydronic heating system I designed (for my own home) was only 14-15 years ago. The first ductless system I specified (for a relative) was about 12 years ago. Since then I've been involved directly or indirectly in specifying, measuring/monitoring or implementing at least a dozen heat pump systems, and an even greater number of hydronic fossil burner systems, learning a bit every time. The rapid evolution of modulating air source heat pumps has been pretty incredible to watch over the past decade, and I'm still finding out new stuff every year (sometimes every month!)
Projects I get involved with tend to be friends of friends/relatives, or sometimes people who find me by word of mouth or web forums, and only rarely have I accepted compensation of any kind. For me it's a hobby, and an interest in seeing people avoid headaches, overspending in the wrong places ending up with less money and poor comfort in what Nate Adams coined the "The Gulf of Disappointment" more than a half-decade ago. It's fair to say that theorajones is currently experiencing that gulf. Getting out of the gulf is not insoluble problem, but it's important to treat the house + HVAC as a complete system rather than separately, and it's important to measure stuff & make calculations before taking expensive action.
I've learned to not expect either the average HVAC contractor or average insulation contractor to give good guidance on the bigger picture, not out of malevolent intent, but rather because they don't really see the whole picture. The "ductless head in every room" micro-zoning approach appears to make sense on the surface, and I'm sure many contractors believe its the best or only way to achieve comfort but is in most cases it's a terrible, expensive, and less effective way to go.
Contractors such as Nate Adams' EnergySmart Ohio company (https://energysmartohio.com/ ) have it MOSTLY right. (He still uses way more closed cell foam than I'm comfortable with from a total environmental point of view, and he has historically been a bit too dismissive of ductless & ducted mini-split solutions, but seems to be coming around as of late). Nate's collection of "HVAC 2.0" contractors will most likely "get it" too:
https://www.hvac20.com/map.html#/
I don't have any direct experience with them, but in eastern MA, Abode Energy (the company Mass CEC has gotten in bed with for the Decarbonization Pilot) will also probably get it right:
https://www.abode.energy/
For those who are newbies to this stuff Nate Adams' short videos and free chapter downloads from his book are available from links on the HouseWhisperer website:
https://www.natethehousewhisperer.com/comfort-guides.html
It's also worth looking at some the detailed case studies (with lots of pictures & details) of real houses that his company has addressed for guidance:
http://energysmartohio.com/case-studies/
Most people will recognize in their own homes some of the flaws/deficiencies addressed in those case studies. I have to tip my hat to Nate for making an HVAC contractor re-crate and return a 4 ton modulating heat pump that was already on the job site when he had specified a 3-tonner. The 4 tonner would have worked, but would have been sub-optimal. It wasn't just dumb luck that he got it right- he had done the math to prove it.
Seems impossible the only problem is excess capacity given that the symptom is insufficient heat output.
If excess capacity were the main problem the complaint would be short cycling. My guess is at this point both systems are undercharged and likely have small leaks.
Walta
Walter, Considering that the systems were so hugely oversized and mis-sized for the demands, it is certainly possible that they were improperly charged as well. Since this HVAC contractor is a hack, it would be worthwhile to have a different contractor check the pressures and other installation features as well.
Still, it is easy to explain the poor performance being caused by oversized equipment. With such dramatically oversized equipment, the heads are cycling on and off, therefore, not providing adequate mixing of the room air. Wall heads are placed high on the walls in general and short-cycling will allow stratification to occur. Since the people are sitting down low, stratification results in warm ceilings, but cool floors and walls in the sitting/living levels. Also, drafts will be more noticeable, as it takes some time for drafts to start convecting. WIth nearly constant head operation and mixing, the cool convection currents don't have time to get established. Also, with the internal temperature sensor driving the system, the sensor is located up high in the room with the head and sensing the ceiling temperature, not the sitting space temperature. Add to that, the fact that some of the individual room heads might be heating adjacent ceilings through convection through door openings and you've got no idea what room is being heated by which head, and by how much.
It's counterintuitive, but this system might work best at very low temperatures with the upstairs system turned off completely. Then it will possibly be running at near its lowest turndown condition and provide more consistent heat and better mixing.