How to insulate the walls of a 1950s concrete block house with limestone exterior on three sides and concrete block on the fourth?

I live in Southwest Michigan. I have an east-facing house built in the 1950’s that was built entirely out of concrete block. However, the east, south, and north walls are covered with what are essentially limestone sculpted (not flat) veneers several inches thick cemented to the surface of the cement block. The rear of the house, west-facing, was never veneered and is currently just plane cement block that was painted brown by my dad back in the 80’s.
The house is spacious. It uses radiant, baseboard heat. The interior walls and ceiling were constructed with a very thick, tight steel mesh, meaning the spaces in the mesh are very tiny, like 1/4″ diamonds, a mesh I’m even reluctant to call mesh because of how very strong and rigid it is, adhered directly to the cinderblock and then used as a base for a thick layer of plaster, a very, very fine plaster that is so smooth and nonporous that I have a hard time getting paint to stick to it, and not just to exterior walls but interior walls too where that mesh is attached to wood studs and then plastered over.
The attic is insulated with a double-layer of fiber glass insulation on the floor, meaning directly against the ceiling below and an additional layer of fiber glass insulation above fastened to the roof decking between the roof rafters. Also, I couple of years ago, I replaced all the windows and doors in the house with new high-efficiency Pela windows.
Anyway, the house is rural and heated by propane, which does cost a bit more, but even with those modifications, in the winter’s coldest months, it’s not uncommon to for my propane bill to be $1,000 to $1,200 for this 2,000 sq. ft. one-story ranch home with a basement.
I think I’m losing my heat out the walls, which being built in the 50’s were certainly not insulated. My questions are these:
1. Is there anything I can do to beef up the insulation on the exterior on the walls that are limestone without destroying or covering the limestone? Like were concrete blocks hollow in the 50’s and, even though staggered like bricks, can insulation be blown into those hollows? If so, would that make any significant difference?
2. If not, will putting up exterior insulation–like Tyvek, foam, Rockwool–on the back wall, the one that is cement block, and then putting vinyl siding over it really be cost effective or make any real difference if I can’t do the same to the other three exterior walls?
3. How much savings should I get, like how cost effective is it, building out studs in the interior walls, insulating, and then dry walling over them? It sounds extremely expensive, involving rewiring, moving radiators, redoing woodwork and trim, completely redoing the solid, 1″ mahogany paneling on all the walls of the master bedroom, losing square footage, etc., that I wonder if it would take decades to never to recoup the costs.
4. Basically, I’m trying to find the most cost-effective way to reduce my heat bills in the winter, because $1,200 a month heat bills in January and February are just outrageous! So what are the least expensive things I can do to improve my home’s heat efficiency given its construction and the challenges that presents.
GBA Detail Library
A collection of one thousand construction details organized by climate and house part
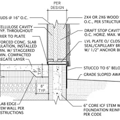
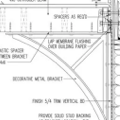
Replies
It would take 3.5" of exterior EPS or 2.5" of exterior polyiso to bring it up to code minimum (as a "mass wall" it only needs R13 continuous insulation if on the exterior in climate zone 5A, R17 continuous insulation if on the interior) but it would cut your fuel use by something like half, maybe a bit more. Currently your walls are in the R2-R4 range, depending on the particulars, but windows are also a significant fraction of the heat loss (~R2- if clear-glass single panes+ storms, ~R3 if low-E replacement windows.) A spray-applied weather resistant barrier on the exterior prior to putting up the foam usually works if the window flashing details are already adequate.
Using EPS can be cheaper, since it can be finished with a faux stucco, where as polyiso would need siding mounted on furring through-screwed to the structural wall.
The diamond mesh is known as "metal lath", commonly used for plaster or stucco in lieu of traditional wood lath.
Insulating the basement walls on the interior with 3" of polyiso, or 1.5" of EPS trapped against the foundation with a 2x4/R13 studwall will also make a difference, but it's lower priority than the fully above grade walls.