How to insulate rafters in 1.5 story cape to reduce thermal bridging?

Hi All,
I live in a 1.5 story cape in Nassau county on Long Island (zone 4a). The house is a fairly typical
Levit with no dormered additions, meaning little to no attention was spent on insulation much less air sealing. As anyone who has lived in one of these houses can attest, the second floor is stifling in the summer. We have a geothermal heating/cooling system with ductwork running through the kneewalls.
I currently have little to no insulation in the rafter bays. What exists is a combination of “fluffy stuff” (fiberglass, rock wool, and even cotton). I want to address the overheating issue, but more importantly want to do it in a way that respects my carbon footprint. After much research, it seems like a hot roof is the way to go. I have been considering open-cell water-blown spray foam to fill the rafter cavity (rafters are 2×6), but I woul like to address thermal bridging, air seal, and bring my attic insulation level to > r38. My question boils down to this: how do I do it? I’ve considered the following:
1. Spray the entire roof deck, filling the cavities with open cell. Build a mooney wall-like structure that is offset from the rafters, cover with netting (and strapping?), fill with cellulose.
2. Same spray as above, but cover the foam with a few layers ofpolyiso. Strap and drywall. I know the gwp of polyiso may be high, however.
3. Same spray as above, fur out the rafters, cover with polyiso, fill the remaining cavity with cellulose. I’m not sure this will work, as it seems to me that the netting allows for air to escape as the cellulose is being filled. Polyiso is not air permeable.
Any thoughts are greatly appreciated! I want to do this project but be responsible to our environment too. Thanks!
Bill
GBA Detail Library
A collection of one thousand construction details organized by climate and house part
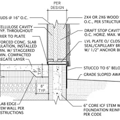
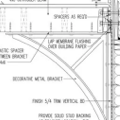
Replies
The global warming potential of continuous polyiso sheathing isn't substantially more (and probably less than) that of open cell between rafters on a performance basis. It's 2x the polymer per cubic foot, but it's performance is higher, and not being undercut by the rafters. An R20 cavity fill between rafters comes in at about R13-14 after thermal bridging, at about 2.3lbs of polymer per square foot (averaged, including framing fraction. That's 2.3lbs/R14= 0.16 lbs/R-ft^2.
With 1lb/ft^3 polyiso you get about R6 for 1/12= 0.083lbs for 0.083/R6= 0.014 lbs/R=ft^2, a full order of magnitude improvement.
The blowing agent for polyiso (pentane) has a GWP of about 7x CO2, whereas the blowing agent for open cell foam (water) is negligible, but no way does that make up for the difference in polymer per R.
But you CAN'T use polyiso on the interior of an unvented roof assembly without creating a highly risky moisture trap.
If you install if closed cell foam blown cellulose between the rafters, install a sheet of smart vapor retarder there and add Mooney-style 2x6s perpendicular to the original rafters 24" o.c. you can then install R23 rock wool on the Mooney-inteiror-purlins with only without any roof-rot risk. You could also put the membrane on the interior side, directly under the gypsum if your installer thinks they can still dense pack it. The flash-foam of closed cell puts a ~1 perm vapor retarder between the cellulose and interior and creates a non-wicking condensing surface, which will protect the roof deck. The variable vapor retarder limits the amount of moisture that the cellulose has to buffer to very reasonable levels, while allowing reasonable seasonal drying rates for the cellullose.
William,
This article explains all of the various ways you can insulate a sloped roof assembly: How to Build an Insulated Cathedral Ceiling.
By far the best way to proceed is to install a thick layer of rigid foam on top of your roof deck. Of course, this approach isn't cheap, and it requires you to install new roofing -- but it is the best way to go.
IRC code-min for zone 4A is R49. With 2x6 rafters and rock wool batts (R23), and 5" of exterior polyiso (nominally R30, before derating) you'd have more than sufficient exterior R for dew point control even after derating for temp. The center-cavity R would be about R43 nominal, but due to the thermal break over the rafters it would still meet code with a U-factor below the U0.026 code max per TABLE N1102.1.3:
http://publicecodes.cyberregs.com/icod/irc/2012/icod_irc_2012_11_sec002.htm
The installed cost of that much polyiso is on the order of $3 per square foot (plus the cost of new roofing) with virgin-stock foam, about half that if using reclaimed roofing foam from commercial demolition. For performance-prediction purposes presume polyiso will average somewhere between R5- R5.5 per inch with that stackup, in your climate. So the 5" of exterior foam is a bit under R25 during the coldest weather, if R30ish during the spring & autumn shoulder seasons. If installed on the interior side of R23 rock wool it performs at it's full rated R, but you'd have the moisture trap problem.
If summer heat is the issue, then the thermal mass of the materials used gets important. Having a heavy material like gypsum fibreboard (Fermacell) on the inside instead of light sheetrock makes a surprisingly big difference. Using dense pack cellulose instead of fiberglass or rock wool also helps.
For a quick what-if, try this German calculator with different materials etc - look at the heat protection values at the top right. Any questions, just email me, their English translation is far from complete. Phasenverschiebung = phase shift in hours, temperaturamplitudendämpfung = temperature amplitude damping.
https://www.u-wert.net/berechnung/u-wert-rechner/index.php?&d0=1.25&L0=1&mid0=196&d1=4&L1=1655634327&mid1=217&x1=10&uu1&d2=4&L2=1655634327&mid2=36&x2=6&uu2&d3=4&L3=1655634327&mid3=217&x3=34&uu3&d4=0.02&L4=2&mid4=2970&d5=14.5&L5=1603385292&mid5=551&x5=70&d6=14.5&L6=1603385292&mid6=36&x6=11&d7=1.9&L7=6&mid7=17281&d8=12.5&L8=3&mid8=3287&bt=1&T_i=20&RH_i=50&Te=-5&RH_e=80&outside=0&name=Dach