Insulating Cathedral Ceiling in Bathroom

We are in Northern NY state, zone 6. The builder installed vent baffles from soffit to ridge vent and spray foamed (flash coated) the underside of the baffles (and partially down the truss rafters). Then he installed R-38 kraft faced insulation between the ceiling joist. The ridge vent was open to the baffles for the most part but when they spray foamed the vent baffles they sealed the ridge vent from the attic space. Around the non-IC bath fan and recessed lights they peeled back the kraft to create a 6-12 inch space with just fiberglass (three sides, one is against the wood0. The upstairs is essentially divided into thirds. One third (the north gable end) is divided in half by a center wall that extends to the peak of the scissor trusses and runs perpendicular to the trusses (for roughly 12′). One side of the center wall is the master bath, the other side is a walk-in closet/laundry . Each has a ceiling that goes from a 5′ exterior wall up to the peak. The middle third of the upstairs is the master bedroom which has traditional trusses and a flat sheetrock ceiling. The south third is a loft area off the bedroom with scissor trusses. Recent inspection revealed mold on the underside of the spray foam applied to the baffles and gable ends and under most if not all the vent baffles to varying degrees. I have removed all the sheetrock from the scissor trusses at each end third as well as the R-38 to gain access to the space then I removed all the baffles and spray foam, killed the mold with Concrobium and RMR-86 and will be painting all with Foster 80-20. Same deal above the bedroom but I could remove the spray foam and baffles and treat the mold from the attic space without pulling the ceiling. Next comes re-insulating in a manner that will prevent this from recurring. We plan to install painted (both sides primed) T&G as the bathroom and closet/laundry ceilings and polyurethaned (both sides) T&G as the loft ceiling. T&G would be installed directly to the rafters. Before I install the T&G I plan to install new vent baffles partially up the sheeting then reinstalling the R-38 without the kraft facing (most was damaged during removal) then install Certainteed’s Membrain. I may also install firing strips after the Membrain and before the T&G to protect the Membrain. I believe I will need to take care to seal the Membrain at the peak to minimize the transmission of water to prevent rot and mildew. I’m also thinking of caulking the T&G joints for several boards down from the peak (entire length) since that is the high point and I need to minimize the transmission of water to prevent rot and mildew. Am I on the right path here? Would I be better off putting one inch foam board down with all butt joints taped instead of the Membrain? Or put the foam board down, skip the tape, and put the Membrain up? Or, do I need to reinstall sheetrock (taped and painted) before I put the T&G up.
BTW, the house if 15 years old with a standing seam metal roof with no penetrations (plumbing vent goes through he gable end). I suspect spray foaming (closed cell) the entire sheeting/roof some required thickness (rafters are 2×6) and turning the attic space into conditioned space might be best but may be cost prohibitive for us.
GBA Detail Library
A collection of one thousand construction details organized by climate and house part
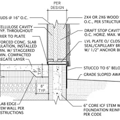
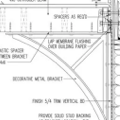
Replies
When doing T&G the most important part is getting a solid air barrier. Detailing poly as your air barrier is possible if you take a lot of care. I think it is much simpler and less chance of tears to install 3/4" to 1" of foil faced polyiso with taped seams instead. This can work both as your air and vapor barrier plus provide a small boost in assembly R value.
T&G can be nailed up through the foam with 2.5" nails. Make sure to mark out your rafters ahead of time.
Generally moldy roofs result from interior air leaks (vapor barrier helps but air leaks is what you need to fix), if you can get your ceiling well sealed, you should have no problems. This generally means taking care with your air barrier, use only vapor tight device box and avoid canned pot lights in the ceiling.
I like it, thanks for the reply. Couple additional questions (of course), you identified 3/4" to 1", is 1/2" to flimsy (locally I only see 1/2" and 1", no 3/4")? Also, I'm assuming foil faced polyiso is installed by gluing to the rafters and cap nails? What would recommended nail spacing be on a sloped ceiling? I'm also assuming I'd have to tape over any nails/caps that break through the foil? Silicone/latex caulk all the edges and seal around bathroom vent fan in similar manner? Sorry to be a pest but the devil is in the details so I want to make sure I get them right.
1/2" is pretty flimsy. The reason for 3/4" is it gives you a bit more nail bite, but 1" should still hold well enough. You will need 2.5" nails with it though.
The reason for foil facing is for ease of taping plus the foil face also works as a vapor barrier.
No need to glue the foam to the rafters, tack it up with a couple of cap nails. The T&G is what will hold the foam in place.
Make sure to use a quality tape for the seams (acrylic sheathing tapes are the best, Zip or 3M 8067 tape is great if you find it locally). You want the perimiter of the ceiling sealed to the wall air barrier (typically drywall or the vapor barrier behind it) with either the same tape or acoustic sealant. Take care with the acoustic sealant it is a black mastic that will stick to anything and everything, I usually prefer to use Greenglue's sealant because of this as it is water based. Make sure there is continuity of the air barrier across the ridge as well.
You can seal the bath fan with some canned foam. Make sure the fan's exhaust duct is also sealed all the way to the wall cap.
You want a nice foam cap on the room with no way for any interior air to escape.