How to insulate a curved 0.25-inch-thick zero-perm wall (a.k.a. a “boat”)?

I’ve been contemplating the concept of tiny houses and, as a subset, boats. One major issue in both is interior condensation, but boats make it even harder since the exterior is zero-perms & about R1. Many folks avoid this issue by running for the Caribbean in the winter, but I’d like something more elegant. How can I insulate a curved zero-perm surface?
The most likely concept I’ve thought of so far is two (1/2″?) layers of flexible closed-cell foam continuously bonded to the surface beneath (yes, I realize this is incredibly time-intensive, but it is a small amt of surface).
Does anyone have a better idea or an additional idea? I’ve heard too many stories of folks running 3kw to heat 200SF of space….and barely controlling condensation…at an exterior temperature of 40degF.
GBA Detail Library
A collection of one thousand construction details organized by climate and house part
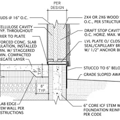
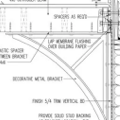
Replies
look at cars, they also use pre-shaped closed cell foam as you describe. I would definitely not risk using spray foam. In case it stinks you can trash your boat...
I would use XPS if possible, cut to fit and 'great stuff' to seal joints. it works under my roof it will definitely work for you too. open cell is out of question as it lets too much vapor pass. the vapor will condensate and get absorbed by the foam. yeah, they will tell you it's hygrophobic too, but that's a myth....or borderline false advertisement if you ask me
Dustin,
There are two factors that affect condensation: high indoor humidity and cold surfaces. You can correct either factor -- in other words, you can either lower the indoor humidity or you can raise the temperature of the cold surfaces -- to reduce condensation problems.
Good insulation is one step. I agree that multiple layers of thin rigid foam or spray foam would make the most sense. Good insulation will raise the temperature of the indoor surfaces in winter -- but only if the interior of the boat is heated.
To lower the indoor humidity level during the winter, you can install and operate a ventilation system.
You both agree with the principles I understand, but my main concern is in the details: what foam to use, how to get it to adhere fully to prevent moisture from getting behind it, and how to preserve access to the multitude of bolts that puncture the deck. As with a house, doing it wrong can create a whole host of troubles: this may be why no one insulates boats...
Perhaps I should clarify: I see this system as being analogous to the PERSIST wall in the humid south in that we have a non-permeable layer and closed cell insulation on the warm side, with the added issue that one would live on the warm moist side. If moisture works its way in to the non-perm surface and condenses, I may get mold and water. I don't mind water running to the bilge pump, but don't want it dripping onto furnishings and certainly don't want mold and decay.
Perhaps I could use spray foam, but can they apply it in a thin and fairly smooth layer? Or could one apply a couple layers of EPS and then cover it with an adhered zero-perm surface pressed into place?
Perhaps the trick would be to use EPS or polyiso on the walls with vertical drainage channels against the cold wall to allow water to run to the bilge where it would be pumped out, thus creating warm walls and dehumidified air.
Perhaps someone has another idea?
A boat is not a house (unless it's a houseboat, of course) so most of our standard assumptions about usage patterns etc. may not apply. Here are some questions for you, Dustin:
Where do you use it? When do you use it, how often and in what seasons? Do you spend a lot of time inside the cabin or just a little? How big is the interior space? Do you cook in it, shower in it, sleep in it?
What kind of heating and cooking appliances do you use? If combustion appliances (I'm sure they are) are they vented? And last but not least, is your biggest concern condensation or just staying warm?
Ultimately I have to wonder if there are not standard solutions to boat insulation that are unknown to us landlubbers here at the GBA forum. And if there are none, is there perhaps a good reason for that?
3lb density closed cell spray polyurethane used in roofing applications would be the right stuff for applying directly to the inside of a hull, and at 2" would be nearly as structural as the hull itself, but even at 1" would give you about R8, and be structurally reinforcing. The stuff is sufficiently waterproof to be used as the only weatherproofing layer on flat roofs- it can hold a pond up there on the roof without absorbing water or losing efficacy as insulation.
Polyiso would be a disaster anywhere in a boat, since it's hygroscopic and dries only very slowly once it's really wet. EPS has the best bulk water tolerance of any rigid foam (it is used as surf-board & Boston Whaler cores, after all), but cobbling it on and making/keeping it air-tight to the hull would be impossible.