How to insulate a basement wall rim joist that is an inaccessible “cavity”?

Baltimore, zone 4A
On my addition being built, I have the first floor joists resting on the poured concrete basement foundation walls. The basement walls are 10″ thick with the sill plate 8″, to leave the typical 2″ strip of exposed concrete along the top of the wall (not covered by the sill plate). I was planning to place rigid foam over that exposed concrete and along the sill plate and rim joist and then complete with air-permeable insulation (mineral wool), as often detailed at GBA and BSC. The problem I have is that along one side, the framers placed the second joist only 10.5″ in from the rim joist, so that it almost touches the inside face of the wall. This now means I cannot access the cavity that is formed by the top of the basement wall below, the two joists on the sides, and the plywood subfloor above. How do I insulate?
I have insulated the basement internally with 3″ foil-faced polyiso up to the joist (the concrete wall will dry to the exterior in the 3 ft that go above grade).
Do I make a hole in the subfloor or access from the basement windows and fill the cavity with cellulose? It could be made airtight, but it would wick moisture from that 2″ strip of concrete it rests on (not covered by the sill plate).
Do I fill with blown fiberglass? It could be airtight, but what would be the relative humidity in the cavity, with that strip of concrete? Enough to ‘condense’ on the joists and accumulate to dangerous levels (on external joist in winter and inner joist in a/c season)? I know there is little vapor from interior air when there is a good air barrier, but from concrete? How much moisture will the concrete have? I have the water that is yet to dry. Also, the basement wall is exposed to rain above grade for 3 ft. It will also receive moisture that wicks up from the existing house (masonry house built 1938, basement slab direct on ground) through the poured concrete bench which connects the existing 7′ basement to the new lower 8′ basement floor (lacking a capillary break from a miscommunication with my builder) (but on the bright side, I hope it does help the brick pass water to the bench to help guard against efflorescence).
Do I fill with open cell foam, which wouldn’t buckle the joists? But 10″ deep foam for 21 linear feet is pricey.
Do I make a hole in the subfloor and pour some of the Henry liquid air and vapor barrier I have to make the capillary break on the strip of concrete, and then fill with cellulose? I’m not sure how confident I can be to get full coverage. And I’m not sure how wise it is to also cover the top of the sill plate with liquid vapor barrier (though it has a capillary break gasket under it).
Do I leave it uninsulated and call it an indentation of the wall ? I could extend polyiso internal to the 2nd joist, continuous with the interior basement insulation. What lies above the 10″ concrete is a same-sized 10″ stud wall (2×6 with cellulose, interior OSB air barrier, 2×4 interior service cavity also filled with cellulose, drywall). So the second joist in from the rim is under the drywall of the floor above. The problem is, I would have a cold corner, plus I’ve never seen a GBA or BSC picture of such an empty cavity.
Thank you for your patience in reading the details and in advance for your advice,
Richard
GBA Detail Library
A collection of one thousand construction details organized by climate and house part
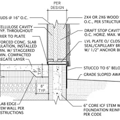
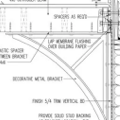
Replies
Richard,
Ideally, such hard-to-access areas are insulated during the framing stage. Of course, that requires using a framing crew that understands air barriers and superinsulation details. Such framing crews exist, but in many areas of the country they are hard to find.
At this point, it's time for you to call up your local spray foam contractor.