How to get gravel to center of pad without driving on the insulation

My design calls for a thickened edge slab on top of 4 inches of foam, with the center of the slab having 6″ of gravel directly under it to take up the extra space. Picture attached.
Obviously you can’t use a skid steer or anything like that to move the gravel around, and doing it by hand would be a herculean task. What is the name of the tool/machine that has a boom with a conveyer belt on it which could move the gravel from a trailer directly onto the pad? I was going to leave this up to the contractor, but certain things he’s done so far leave me with little confidence in his ability. Without spelling it out for him, or perhaps even taking this particular task out of his hands, I think it’s possible he actually would drive a skid steer right onto the insulation.
GBA Detail Library
A collection of one thousand construction details organized by climate and house part
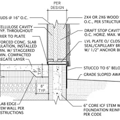
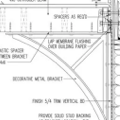
Replies
Trevor,
It's called a Slinger Truck.
ISTR someone telling me that you could get a concrete truck to deliver stone. Never asked but it seemed like a good idea if it worked and didn't cost a mint.
Seems like a bad design for a number of reasons, from moisture retention to practicality of build. I dont know what stage your at but you might consider modifying.
Edit:
Plus, how do you ensure compaction of gravel? Even with washed gravel you generally want to run a pad foot over it.
You run the vapor retarder over the fill so there are no moisture issues. You run a jumping jack over it to compact it. I think it's easier to do a good job with that type of system than to try to run rigid foam on an angle for a monolithic pour. I've used a similar approach a few times with WarmForm: https://warmform.com/wp-content/uploads/2023/05/WarmForm-Instruction-Manual-s.pdf. They recommend using EPS to fill up the space, but I've done it with gravel and with Glavel instead.
I dont know, I’m not convinced.
While yes you may not have slab issues with vb on top, you are still making a potential pond under your slab. It also seems to forget the purpose of gravel in the first place, to make a drainage plane and solid substrate for slab. With this assembly you insulation will be much wetter and more susceptible to bugs. And it’s harder to build to boot. With the detail attached, you could just leave out a section of the perimeter insulation and fill in center with skid steer and get great compaction. Then just lay your insulation on top and trim a slope on the edge insulation.
I think the only benefit this detail has is looks in section.
freyr_design,
I've still not seen any convincing explanation for why the interior face of the thickened footing benefits from being tapered. Maybe it is just because it's easier to contour fill that way than having a vertical face?
The only reason I can think of is an attempt to reduce stress concentration associated with sharp angles. Though if this is the case a rounded corner in the foam would work better than the standard slope.
This article discussed it in relation to a products but same principle applies. https://www.fictiv.com/articles/stress-concentrations-how-to-identify-and-reduce-them-in-your-designs#:~:text=Stress%20concentrations%20occur%20because%20of,reduce%20the%20stress%20concentration%20factor.
Also I highly recommend this book:
https://www.amazon.com/Structures-Things-Dont-Fall-Down/dp/0306812835/ref=asc_df_0306812835/?tag=hyprod-20&linkCode=df0&hvadid=693633693503&hvpos=&hvnetw=g&hvrand=13213478202601840034&hvpone=&hvptwo=&hvqmt=&hvdev=m&hvdvcmdl=&hvlocint=&hvlocphy=9033354&hvtargid=pla-433805920483&psc=1&mcid=4392b037b6883e75a30108143fccfac6&gad_source=1
It is by far the most interesting engineering book I have ever read. It has an interesting story about how we learned about stress concentration when we first designed steel ships (and a few sank). This is why all the doors and openings in ships are rounded.
freyr_design,
Wouldn't you get the same reduction by just tapering or rounding a 2" area where the slab meets the footing?
Yes probably true.
freyr_design,
Makes your detail even easier.
I don't really like any monolithic slab details except for raft slabs, which require a level surface and everything is built up from there. It's easy to specify and for excavators to get right. When you start adding multiple layers of fill at multiple different times, you risk mistakes and drive up costs. Maybe if I were the one doing the physical work I'd feel differently, but it's hard enough to convey all the right information on a sheet or two of paper; I've found that I need to keep things relatively simple for the builders.
When you have a raft slab, you can either use more concrete than necessary, more foam than necessary or use a relatively inexpensive, low-carbon material such as gravel or Glavel. I've done all three multiple times and my current favorite is Glavel.
ya, i suppose that is a valid concern. though there are much more complicated aspects to a build then layering your slab base so I would be a bit hesitant with a builder who couldn't figure that out. Glavel does seem like a pretty cool material, hopefully I will get to try it soon.
I tried to get the engineer to draw up a raft slab, and he wouldn't do it. He's used this design before, so was comfortable with it. I couldn't find any other engineer to even entertain an insulated slab of any kind.
I just had a similar slab poured last week. Had my excavation contractor place the gravel using an excavator. Took almost no time and we just raked it out to level. As for someone not liking the design, my concrete guy has worked here for many years and says it's now common here in Maine. We installed wire mesh and much rebar (12" grid) so I have no worries.
I had my shop back filled by a rock shooter.
Back when we were young and stupid, we sometimes used to get the rock for perimeter drains delivered by a slinger truck and stand behind a sheet of plywood to defect it into the right spot.
Notice how I used We to try and spread the blame a bit.
I've only seen it done with a relatively large excavator. One company I know of uses flowable fill instead.
I've had gravel delivered by concrete mixer. Super convenient, but a little expensive compared to a dump truck.
Trevor,
FWIW, all of the washed stone placed placed around my foundation perimeter drain system was delivered in ordinary cement trucks. The stone was then placed via conveyor with a drop tube at the end just the same as the footings and wall concrete. (pic below) Site limitations made this the only viable method. The interior washed stone was delivered the same way, although there was still some hand work due to the radon tube placement. I don't see any radon piping on your plan. Are you sure about not needing to place piping against future surprises?
Like others, I am a bit perplexed by the drawing you provided. It seems as though the slab pour will just meld down into the stone if done as drawn as there is no plastic barrier indicated. Freyer_design's suggestion makes a lot more sense and would be better for soil moisture management. I am surprised that compacting over foam board would be practical, but then I have never tried it. If not smooth pea stone it would seem to be a recipe for a very mangled VB.
I also am curious about the very extremely cantilevered 2x10 base plate. I can make out the two additional base plates for a double wall construction, but can you really be sure all the load will be borne by the inner most 2x4 wall? The foam on the perimeter is not much of a support. The foam is also shown as 6" not 4" and there is no indication of how you intend to protect the perimeter foam.