How to fix existing walls with 2 vapor barriers?

Hi everyone. Like to get input on the best way forward as we replace our masonite siding with fiber cement lap siding. I’m concerned that if the existing wall structure is kept it won’t breathe. The 1989 home has polyethelene sheeting on the interior and Polyiso foam on the exterior. The current wall inside to outside is sheetrock, Polyethelene sheeting, 2×4 studs w/R13 fiberglass batts, 1/2″ Polyiso foam (foil facing inward, mylar facing outward), 7/16″ masonite lap siding. Polyiso foam joints are not taped/sealed. Structural support is from 1×4 diagonal let-in bracing. We are in IECC 2021 climate zone of 3A (changed from 4) above the warm-humid line so ‘mixed-humid’.
I have not yet opened any exterior siding to check for damage, but preliminary pin-moisture meter spot checks from the inside shows 11-12% in the studs. I think the energy bills have been helped by the exterior foam so hesitant to delete that. I’ve thought about removing the exterior foam then reaching through the batt insulation to slice the polyethelene sheeting to remove it, then reapply the exterior polyiso, seal/tape the polyiso to use as the WRB, then fiber cement siding. However sounds pretty labor intensive and I’m not sure the existing polyiso could survive without damage. I would really appreciate any opinions out there – what would you do? Oh, the wall cannot easily get thicker because the gable ends have no overhangs.
GBA Detail Library
A collection of one thousand construction details organized by climate and house part
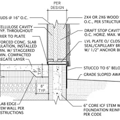
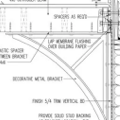
Replies
I know very little about warm climate construction, but..
11-12% moisture content is quite good, over 19% will encourage mould growth.
The exterior insulation may be keeping the sheathing warm enough so that condensation does not form. Without evidence of deterioration I would not assume there is a problem.
If you're at 11-12% now your wall is working fine.