Insulating With Cellulose Batts

I would like to build a small house. I can’t afford rent plus utilities any more.. I am on fixed income and we only have social security. I have scouted various house plans and kits. I was first interested in geodesic domes. I think, I, as an amateur could probably construct a dome from a kit with just a little help…I looked at log cabin kits but they are too expensive….FINALLY I have discovered the Arched Cabin which is made in Texas. You get metal ribs which you connect and lift up to form one side of the house and the roof….and you raise the opposite set of ribs and they connect at the top,.. finishing the structure. The siding/ roof is metal plates that resemble the corrugated tin roofs but the corrugations are bigger and the plates run the length of the house(hung horizontally). You finish the two ends using conventional framing techniques. I think this is doable and affordable ( for me). My big question is how to apply the insulation?…..I live in NY and they are crazy for wall board ( 3/4″ gypsum) as the interior walls. This costs a FORTUNE to have installed. I also don’t like fiberglass nor blown in foam insulation. To keep costs down I must avoid any crew work such as blow in insulation…even a concrete pour for a foundation is cost prohibitive.I plan to do a post and beam foundation…The company,.. Arched Cabins, provides two sheets of insulation that cover the outer side of the metal ribs. It seems inadequate for NY winters. When asked,. they told me their clients who wish more insulation have foam insulation blown in…Again, I don’t want foam and I don’t want any crew expense…..MY QUESTION:….Does any one have experience hanging cellulose batts on the inside of a structure like this? I understand cellulose’s fire rating is quite high; and can i cover the cellulose with plywood rather than the expensive wallboard gypsum to meet the fire code?……Any help would be greatly appreciated. I contacted Habitat for Humanity but they claim they have no experience raising this kind of structure. I want a well insulated home and want off grid electricity to do away with the expensive Central Hudson electricity bill which is one of the most costly utilities in the country….again…any help would be appreciated…thanks…barbuto, poughkeepsie NY..12601
GBA Detail Library
A collection of one thousand construction details organized by climate and house part
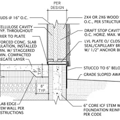
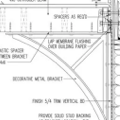
Replies
Barbuto,
You might have better luck meeting your budget by looking at modular homes designed for cold climates. My concern with a kit is that you might struggle to make it efficient and comfortable. The Arched Cabin, for example, only comes with R-13 insulation, which might work in Texas (not really) but not so much in New York.
It seems like if you plan to do the work your self you should learn to stick frame the house. Your labor is free and materials are cheaper than a kit. Double 2x4 walls with cellulose insulation. Then stick frame the roof with a flat ceiling and more cellulose. As simple as it gets. You just need to upgrade your skills.
PS. Dry wall is simple to install and very forgiving and fixable with drywall mud and sanding.
Spend time on youtube to understand framing and hire some one to draw a set of plans that are easy to build.
the two end walls will be stick framed and thats easy to hang the insulation between 2x6s...I like the idea of the kit because it is FAST.....and here in NY time is MONEY....Also I don't need to hire crews to close in the building if I get the Arched Cabin,,,,,Thats 50% of the framing for $20,000 and its erected in a few days....stick building takes time and money....I still need to know how to hang the batts between the metal ribs and over the top to cover the ceiling and down the other side...I don't want dry wall and if I could cover the insulation ( if code permits it) with paneling or ship lap I would be happy camper.....Time and Money...I must reduce...the idea of buying a modular home...too expensive...could never afford the mortgage.....I believe materials, land and everything else I need should come in around $100,000,,,I can afford a mortgage for that...Homes, even modular run around $250,000-300,000 around here...and I CAN'T afford that.....I appreciate your comments...if any one has experience hanging those batts please let me know.....thanks again
I think an under-insulated, unsealed metal home in upstate would be a comfort and financial disaster. If you are not a skilled DIY person, I think your best bet is to buy a tiny home and move it to your property. There are lots of options here: https://tinyhouselistings.com/countries/united-states/states/new-york
And many of them fit your budget.
Generally with a steel building for the insulation to be effective it must be on the exterior.
In terms of dollars per square foot buying a pre owned home is the lowest cost option.
If you can no longer afford New York it may be time to leave the high tax state.
The shell of a building is probably the leas expensive major line items for a house. Don't get caught up on focusing on that as it is not what will drive your overall budget. This a trap that a lot of people fall into when they think container housing is cheap.
Dealing with a curved structure is not easy but doable.
Probably your best bet is to add layers of rigid insulation on the inside over the steel ribs (NOT in between them as thermal bridging from the metal kills 50% to 60% of the R value). I would go with thin layers of unfaced EPS so it can be easily curved. Something like 5" of EPS plus the R15 from the factory would make for a pretty wall/roof in colder climates. With the seams taped on the foam it will be a great air barrier and you can finish the inside with T&G, no drywall needed.
Trying to install batts or dense pack a curved wall will be more work. The amount of wood and labor it will take to do that, you might as well build a stick framed wall and skip the metal shell.
I've built a couple of these buildings as workshops, but never insulated them. Seeing as the shell is also the structure, I'm having trouble understanding what you would fasten the insulation and interior finish to?
The difficulty with integrating standard building details into these building is what stops them from being used as houses. They really aren't great workshops either, as it's difficult to place shelves against the walls. What they are best at is as barn buildings or garages.
On a side note: I've never heard of cellulose batts.
Their technical details are not the best but it looks like the siding/roof is installed over a metal skeleton.
You should be able to fasten rigid insulation held in place with strips of plywood to these with self taping deck screws. Essentially a reverse rain screen. Your interior finish can now attach to these plywood strips.
I have seen condo presentation centers built with similar structure, looking at the details, dealing with curves is a pain in the @#$. Straight walls/ceilings are your friend.
A useful link: https://www.greenbuildingadvisor.com/article/insulating-a-metal-building
On the off-grid element of your project, I would just make sure you have a clear vision for what you're trying to achieve. You likely can't rely entirely on solar, unless you put a significant portion of your budget towards batteries. I think most here would recommend a small solar array and possibly a single battery as budget allows - and then falling back to Central Hudson to get you through nights with heavy energy usage, cloudy stretches, etc.
From their website, it looks like as an upgrade they will provide up to R25 insulation for the walls for you. As for drywall, labor is the main cost there. Installing drywall is not fun, but really very doable if you don't mind not having the highest grade installation. I have no clue how one would install it on a curved surface surface like your arched cabin though. I would also really reconsider the arched cabin for this reason - building a simple box will make everything go in easier and shouldn't really cost more. There are quite a few kit based companies for building small panel homes. It's really a shame there isn't a main global equivalent to the old Sears homes that used to be prevalent across the country prior to ww2. It's my understanding that most of those were built by the family that bought the kits, often with no prior building experience. That may be a big plus of going with a kit over just building it yourself, there is a lot to think about when building a home in terms of meeting code and making the home work. Following step by step instructions from a kit company is likely (hopefully) a lot more straightforward and faster and less prone to permitting issues than someone with no experience building from scratch off of construction drawings.
here is an example of a more conventional home kit after a quick google. $23k+engineering, but that includes preinstalled siding and windows, etc. https://www.zipkithomes.com/plans-pricings/configure/kit-homes/skyline. Shipping would likely steer you towards a local company.
Deleted
These kits from Australia (https://ecokit.com.au/) and France (https://www.brikawood-ecologie.fr/home/) look interesting. Not sure if there is a US equivalent though.
I'm not going to tell you not to build your own house. In fact, I'm in the middle of building my own right now, and by building my own, I really do mean building my own as in framing, plumbing, electrical, finish work, everything except the foundation pour where I was just a helper.
Not having enough money to do it right is a huge challenge. Not insurmountable, but it is a challenge and chances are it will cost you a lot more and take a lot longer than you think it will. It always does. Keep a contingency fund of at least 10%.
Be very wary of the out of the ordinary designs and techniques. They aren't common for a reason. Sometimes that reason is just labor cost, but usually there's a few more reasons that aren't immediately knowable.
Consider the end product and its value. "Resale value" is often a poor excuse for things we don't really need in houses, but on some level it should be considered. If you pour $100,000 of your money into something that nobody else would ever want to live in then you don't have an asset. You may have somewhere to sleep for now, but you won't have any flexibility to make changes if your life situation changes later on. If you're able to build a more conventionally appealing home within that budget then you'll most likely have a lot more value than the $100k invested. Mine is about 2.5x value vs investment right now, but that's also a bit of luck with the local market demand. If I wasn't emotionally invested in this house I could sell it on completion and have a lot more options open to me.
Just something to think about before diving in.
Andy,
Sound advice.
I only wish I had heeded all the sound advice I was given before starting.
i would like to thank all who gave replies to my question.....I have some answers to some of your concerns/questions...1) square is easier to construct than odd shapes....I agree with this. But the fact that the Arched Cabin provides two floors....(17ft tall in the 34x26ft version) means I have the efficiency of a two floor house using small sf.....884 sf on the first floor and about 400 sf for the loft. Building vertical walls in the interior first floor....I loose about 9" from the curved wall to the flat vertical inner walls. this space will be filled with insulation and also run conduits on the floor for electric...etc...2) how to attach batt insulation....while studying dome designs I noticed they used a wooden "arm" extending out from the dome structure long enough to contain the insulation....In some super efficient designs they had as much as 12" of insulation. I am using a 9" thick batt I saw on line of cellulose(R35). At the end of this "arm" is a piece of wood nailed on rt angles to the arm. This piece holds the net which holds the batt in place and allows the inner wall to be nailed.As you go up the wall and the walls curve....u attach the arms with metal sheet screws to the metal Cabin rims and adjust the arms so they are all the same length from the ribs..Hang the net and cover with thin flexible ply wood...or ship lap boards in some areas for contrast....If it works for the domes it should work for Arched Cabin.....3) amateur workers.....I have contacted habitat for Humanity. They are not keene on building this claiming that they have no experience building Passive homes. this will not be truly passive, but I plan on using some of the principals of passive design...air tightness, reduce thermal bridging, maximum insulation, air circulation system, super efficient doors and widows....etc.I think they will come on board if I have the plans drawn up by a Passive trained architect and they meet NY state codes...4)Efficiency... It will be filled with low wattage, hi efficiency appliances. We have a gas furnace/air conditioner in our apartment. It works great. I will get one just big enough for the cabin and use ducts and the natural design of the cathedral ceiling, with fans to circulate the air. My wife has health problems so we need the a/c in the hot humid summers we have here in ny.Gas is far cheaper than electricity which we shall generate from the solar powers and batteries....5) I have done a lot of solar power research and believe the smallest sized unit we need will be within our budget if we have local qualified people ( Habitat for Humanity?) install it....I can buy the system as I will buy the appliances...sending out bids to various companies. In fact I have 15 years experience in Industrial sales so I know how to write bid requests and proposals. We have three sources for lumber and hardware up here so all three will get the bill of materials and the best quote gets the business. By being my own contractor I think I can save a lot of money. Habitat for humanity claims thru them houses cost( and the mortgages u need to get) about $50-60,000...When you consider houses run for $250,000-300,000, stick built from contractors or house builders...thats huge savings....Of course I will have to have all the code work done by licensed people; electrical, septic, etc...unless Habitat has qualified people.6)..design for the future..I and my wife are in our 70s...What future?....10 years or so?...I have two kids..When we pass on they get the house . They will be grateful as my daughter has a miserable 1 bedroom apartment she pays $1,000 a month for and our son, who is not a full time teacher, but a substitute teacher makes half the money a full time teacher earns. Because of that he lives with us in a small 2 bedroom apartment. He gets the couch and half the kitchen dinette area. In the Arched cabin he will get the entire upper floor...SO I think we have two people who will love our house, when we are both gone......I am not thinking about selling it. the solar batteries should last about 8 years and possibly some will need to be replaced at that time. I think the Arched Cabin with NO Central Hudson utility cost and a small budget for the batteries ( replacement allowance) should cost less than what I am paying now for apartment and grid electricity........Thanks again for all your comments...I learned a few things and if u have any other pointers...." keep em coming"....regards