How to Detail Tile to Allow Drying to Interior?

I’m about to tile the subfloor of a tiny house on piers. The crawlspace is open, and the subfloor is foam-insulated (so, it can’t dry to the exterior). Questions:
1) What backer material should I use to make this assembly safer? Ditra is plastic (impermeable). They say it remains a little permeable if you don’t seal the seams, but that seems very minor. 1/4″ Hardie Backer is ~2.6 perms.
2) The subfloor is dry right now, and has a VB on the outside. And the porcelain tile is vapor-closed. But I’m afraid of the moisture I’ll introduce via the thinset used to install the backer. How will that moisture ever escape or diffuse? Just through the grout-line gaps in the tile before I grout? There’s also incidental water getting through grout lines in the future… but could I safely assume that water would get out?
3) Any recommendations of vapor-open grouts/sealers? Any research/guesses on how much drying potential these actually offer?
Thank you! And P.S. This is the long-delayed followup to my vapor-barrier-sandwich post: Floor Insulation and Moisture Concerns in Hot Climates, Vapor Barrier Sandwich – GreenBuildingAdvisor.
GBA Detail Library
A collection of one thousand construction details organized by climate and house part
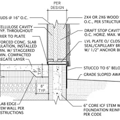
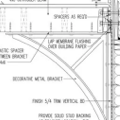
Replies
Much of that depends on the type of tile you install. Glazed / ceramic tiles obviously have little vapor permeability, but others may be more vapor open.
One method you could use is a dimple mat, for separation between the tile backer board and the plywood. That would create a small air space above the plywood, and while there wouldn't be active air flow, there's enough room for a vapor pressure gradient to diffuse out into the main volume. They've got way more compressive strength than you would require, and are pretty cheap and easy to install.
https://henry.com/fileadmin/pdf/current/tds/HEDB650_techdata.pdf
Alternatively, you could go all in and detail the floor as a shower pan. I'd use a PVC liner for a little bit of flexibility over something like Red guard. That would essentially ensure that no water or water vapor from the interior reaches the plywood. Sure, it makes an impermeable sandwich, but if it's dry when installed, it'll probably be fine for a long time.
The tile is porcelain, vapor-impermeable. It would be easy enough for me to detail the subfloor like a shower pan -- except that, again, that requires covering the subfloor with thinset (Hardie Backer and every plastic decoupling membrane I've seen require embedding in thinset). So, I'd be significantly wetting the subfloor immediately before making the impermeable sandwich.
James,
I would suggest you are overthinking this a bit. Unless you are planning on showering in the middle of your tiny house, long term moisture is a low problem. Hopefully the underfloor foam used is closed cell for best control of exterior humidity. You don't include your climate zone and humidity profile. There are some risks to air conditioned cold floors driving moisture build up in a subfloor over an open crawl. Batt insulation would provide the very least protection, open cell not a whole lot more and closed cell the best.
The total moisture you would introduce to your subfloor with thinset is probably less than two gallons depending on total area. More to the point of ensuring the longevity of your tile work is controlling the flex of your sub-flooring. This becomes very important with plank or large tile formats. Provided your subfloor material and joist spacing is adequate, you could just RedGard two coats over the whole floor area and tile directly. If you really splash about a lot or live next to water and come home dripping and leave wet towels and suits on the floor repeatedly then maybe adding the tileboard of your choice would add to your peace of mind. I would still put RedGard or equivalent on the tileboard first. You set tileboard in thinset to ensure support for the tile to be set and to bridge floor deviations.
Not using tileboard may sound like a shameful recommendation to some, but I have torn out enough bath and kitchen floors to know it takes more than casual drips from washing dishes to degrade even a completely un-waterproofed subfloor. Leaking toilet seal rings, soaked bath mats and misplaced shower curtains have been the most frequent culprits. RedGard over the subfloor would have slowed all but the toilet ring failures. Some cement boards (mostly historical now) freely passed moisture into floors and walls which I have needed to replace.
Many people took the idea that cement board doesn't degrade when wet to also mean it won't pass water. Please note that cement walls don't degrade when wet, but certainly can make for soggy basements. Showers and foundations experience lots of water. Living spaces and kitchens not so much. Dimple mats for foundations are fine and effective with proper drain tiles, dimple mats under an interior tile floor is not necessary.
For added water security you could use epoxy grout. It is expensive and a bit tricky to install though less so than 15 years ago. Not sure if it is quite DIY yet. The amount of water penetration through grout depends on how long the water sits on the floor. A soggy bath mat left on the floor day after day can drive a lot of moisture downward. Same with slow leaks at the toilet seal ring. Potted plants that get over watered repeatedly are another culprit. Just think through how you live.
The total area of grout is higher with small tiles, less with big tiles. Sanded or un-sanded pass water equally well though you can put silicone treatments on both. Tedious and it needs refreshing periodically. There are other sealers available, but too much for this already TL/DR.
A last suggestion for extra safety in potentially bouncey floor spans. Use an Ultra flex thinset. I have saved a foyer with it when structural upgrades could not be done. Not proud, but it is still there almost 20 yrs out.
If this is your first tile attempt, check all of the floor and level patch it before the RedGard. Think through the pattern drops and where to start and exit a room. Check thresholds and door clearance, trim placement, flooring transitions, and so forth. And notch the thinset in straight lines not swirls. A trapped air bubble will never give up.
The above reply is super helpful and should be read by anyone a-tiling! But in my case, I don't want to detail my tile backer as a vapor barrier -- I want to detail it to be vapor permeable.
For anyone reading this down the road, here are the aspects of my solution to this problem:
1) Instead of Schluter Ditra, or 99% of other decoupling membranes, I'm going to use a product called Laticrete Strata Mat. It is covered with tiny holes to allow mortar to dry quickly... and since thinset is vapor permeable, it will also give the subfloor some drying potential.
2) I'll also use cementitious grout with a penetrating (not topical) sealer, to allow some drying-out through the grout joints. Ask your manufacturer, but most of these products are permeable.
3) I'm going to leave some areas strategically un-tiled (or only "superficially tiled," i.e. not thinset, which is possible with my 18x18s) to allow some drying potential (under a double vanity, e.g.).
4) And finally, for belt and suspenders, I'm going to hole-saw a few exploratory holes in my floor insulation to allow me to measure the subfloor's moisture content at several stages in the process. I'll report back if anything is catastrophic. If not, I'll fill them with canned foam.
Hope this is helpful to someone out there!