How to avoid trapping moisture in a wall with interior and exterior gypsum?

I live in a wildfire zone in California and am building a shed with metal siding. With metal siding, FEMA’s recommendation and local county codes require a thermal break between the wood framing and external siding. The details are shown here:
http://www.fema.gov/media-library-data/20130726-1652-20490-4085/fema_p_737.pdf
Page 36, Figure 2
My concern with this setup is moisture being trapped in the wall. My layers from inside-out will look like this:
interior gypsum -> framing/insulation -> plywood sheathing -> exterior gypsum -> wrb -> metal siding
If I understand gypsum correctly, it acts as an air barrier. Recommendations from the above source recommend taping all seams of the exterior gypsum. Given this setup, it seems like the wall is going to be airtight and wouldn’t be able to breathe.
Am I right, or am I worrying about nothing? If this is an issue, how can I avoid this issue? Would a rain screen between the sheathing and external gypsum be the way to go?
Thanks for any advice on this!
GBA Detail Library
A collection of one thousand construction details organized by climate and house part
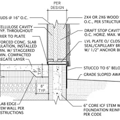
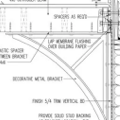
Replies
The wall doesn't need to "breathe" as in leaking air. It needs to be able to dry via vapor diffusion, and unpainted gypsum board is VERY vapor permeable (15+ perms), more vapor permeable than some housewraps, and more than 10x more vapor permeable than dry 3/4" plywood (less than 1-perm). With even the tiniest gap between the gypsum and metal siding the wall can dry toward the exterior.
But even it's it's vapor-tight to the exterior (metal laminated to the gypsum), as long as you don't have an interior side vapor barrier it can dry toward the interior. In most of CA you don't need or want a vapor barrier anywhere in the stackup. The places in CA where tighter vapor retardency might be necessary in that climates is at altitude, in US climate zones 5B or higher. In 4B or lower it just doesn't matter.
So, find yourself on this map, then take a big sigh of relief:
https://www.greenbuildingadvisor.com/sites/default/files/images/DOE%20climate%20zone%20map.preview.jpg
In zone 5B you could get there with a 1/4" rainscreen gap, but I'm not sure how to guarantee the gap with non-combustible materials. (Haven't thought about it very deeply.) In 6B you'd need a class-II vapor retarder on the interior. (Smart vapor retarders preferred.)
Peter,
You are describing a wall that will be airtight on both sides. That is a very desirable wall. Every builder should always strive to build a wall that is airtight on both sides.
Of course, any wall can be improved. If you have 2x4 or 2x6 studs filled with fluffy insulation, you'll end up with a wall R-value that is ho-hum or poor. If you want a higher R-value, that can be achieved by including a continuous layer of rigid foam sheathing on the exterior of your studs (presumably between the plywood sheathing and the exterior gypsum).
In a fire zone it's better if any foam in the wall stackup is rigid polyiso, which won't melt when heated, and has a higher kindling temp than polystyrene (EPS or XPS), which can melt and turn into a spreading puddle of flaming plastic. (Of course, the shed's probably gone by the time that happens if you're building with the thermal break, but still...)
In almost all of CA a 2x6 / R20 wall would meet or beat IRC code minimums even for a house, and in much of the state 2x4 / R13 cuts it. But this is a shed, and SFAIK there is no code requirement to heat or insulate a shed. But if you're heating it & cooling it even on an intermittent basis some amount insulation (as indicated in the stackup description) is a good idea. If it's going to be heated & cooled most of the time, the IRC minimums or better would be a good idea, even if not required.
Thanks for the answer. It looks like I conflated air permeability with vapor permeability. I understand the difference now. I'm in a coastal area, so it seems like I'll be fine without any extra interior barrier.
Martin - Thank you for the insulation suggestion. I'll definitely take that into account.