How to add insulation to our non-vented cathedral ceiling roof in central PA

I am hoping someone on this forum can help me. I have talked to numerous local contractors, architects, & engineers but I am getting so many different answers we can’t make a decision on it. We live in Central PA. We have a home built in 1969 with all cathedral ceilings. The ceilings are non-vented and we have 3″ x 10″ Hemlock beams 4′ on center with 4’x8′ stressed-skin panels on top of them of plywood, foil-faced fiberglass (both sides of fiberglass appear to be foil faced), then the roof deck. We have shingles on top. It is R-19 at best and the foil seems to be crumbling in most places we have been able to access. We would like to add insulation. We are down to 2 options…
1) Add 3″ Polyiso Nailboard insulation to the roof deck and re-roof the house. Our main concern with this is adding the extra weight to the 3″x10″ beams. Although they do not appear to be the least bit stressed now & it is not that much weight, they are spanning a good distance in 2 locations (24′ length of beam)
2) Fill between the beams on the interior with a blown in fiberglass adding R-41 and then install a new ceiling to the bottom of the beams (we do not need to keep the beams aesthetics). This should not be adding as much weight to the roof system as it is from below…we think….
Any thoughts or info are greatly appreciated!
Lara
GBA Detail Library
A collection of one thousand construction details organized by climate and house part
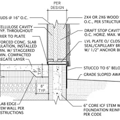
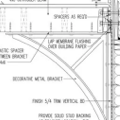
Replies
Recent thread on a similar topic:
https://www.greenbuildingadvisor.com/community/forum/general-questions/18212/how-do-i-insulate-my-cathedral-ceiling
thanks...yes I saw that thread...I am concerned about the non-venting and adding polyiso above the sips that are double faced foil fiberglass... just don't want to trap moisture between them...would that be an issue?
Lara,
A 3x10 beam, 4' oc, with a 24' span is considerably undersized for a roof load in snow country. I would not add any additional weight (above or below makes no difference) without an engineer's approval and whatever structural improvement is required.
Stressed-skin panels do not have fiberglass insulation. They have rigid foam cores which act as the web member of a truss. If you're considering re-roofing, it might be wise to remove the existing insulation boxes from above the rafter beams and either install SIPS and leave the roof unvented or install ventilation baffles and a new roof deck and then insulate between the rafters with strapping and drwall.
Alternatively, depending on the engineer's recommendation, you may want to completely reframe the roof with properly-sized rafters, vent, insulate and drywall.
I would advise against adding non-permeable insulation over the existing fiberglass-filled boxes.
Thanks Robert, We did have a structural engineer come look at it...he felt that adding the 3" polyiso at about 2lbs/SF would be okay. There is only 1 beam that stretches the 24', and it is a center beam in our foyer that is only 8' wide, so the other 2 beams in that space are resting on load bearing walls. The roof is steep on the whole house and 1 room has beams 12' long, the main room is an average of 17' long. We cut into the roof to see what was up there because the drawings from 1969 said stressed skin panel (we assumed foam cores also), but we found fiberglass with foil on both sides... so obviously the contractor at the time custom built the panels and used 3.5" of fiberglass with foil rather than the foam core. The cost to remove all of these panels and do all new SIPS is not anywhere near our budget I am afraid... we will need to wait several more years to be able to afford such a huge project.
Lara,
If you have an OK from an engineer, then go with the polyiso on top. And if you can afford it, it would be great if you could add more than 3 inches of polyiso.
What about opening up the insulation boxes from the top and replacing the FG with cut/fit polyiso foamed around the edges? Re-sheathe the tops, possibly with more polyiso and then plywoood.
I would be hesitant to add more money on top of the insulation boxes without at least looking inside.
As I understand it, you have a SIP roof which is a sandwich that consists of plywood-rigid insulation(fiberglass?)-sheathing-shingles.
From your post I do not get the impression that there is any additional insulation other than this panel.
It has been suggested that a SIP panel would be foamboard, not fiberglass. And this is basically true.
So, three questions:
1) Do you know for certain, what the insulation material is?
2) How thick is this insulation?
3) Why do you want to add more insulation? Do you have a problem you are trying to solve? Do you need more? Do you think you need more? This helps tailor the answer to suit your needs and address your problem.
And for the record I believe by definition a SIP roof can have mineral wool insulation. There was a product made in Vermont (I think) until the late 90's that used rockwool and dimension lumber that was made into a "Structural Insulating Panel." It wasn't that good, but it met the definition. I looked at one house that had it. The IR images were horrible.
-Rob
Sorry, I somehow missed your post where you answered questions 1 and 2.
So question number 4. Is there any airspace above the 3.5" fiberglass board?
These roofs also work well if the outer layer of sheathing is removed and they are spray foamed.
-Rob
We have an access hole where we investigated and the current insulation is 3.5" of foil faced fiberglass (both sides foil) with plywood sheathing on top as the roof deck and plywood on the bottom that is our ceiling above the 3"x10" beams. There is no intended airspace. We need to add insulation because we are losing all of our heat through the roof... we have icicles everywhere and the snow melts off quickly. When we do have a lot of snow on the roof our house is actually warm! We want it to be like that all of the time. I have more drawings that I sent to the engineer this morning. I agree that we will investigate while we are up there...if the possibility of removing the upper section of the sip and replacing that fiberglass with foam seems reasonable, then we may do just that. I talked with our local Icynene contractor about that, but he felt that spraying from the exterior - leaving any airspace above the icynene toward the roof sheathing without any ventilation would be problematic.
It's hard to see how sprayed foam inside those boxes would make a uniform, flat, 3-1/2" thickness without air space under the upper layer of plywood. Is each box a single 4' x 8' cavity, or are they partitioned? Rigid foam board seems a whole lot easier. You can work with small areas at a time, rather than opening the entire roof to the elements for the spray foam guy, and you can use closed cell rather than open, which is probably better for your application.
Lara,
If the roofing doesn't need replacing, I would leave the current roof alone, hang drywall below the roof beams for a good air barrier (air leakage may be as much a problem as heat leakage) and then dense-pack the space with cellulose insulation treated with borates (no ammonium sulfate).
If you have a full 10" cavity, you will get R-38 from the cellulose plus whatever little the existing fiberglass boxes provide, and a much more air-tight ceiling (no can lights). And the cellulose will dramatically increase the ceiling's fire resistance as well as acoustic performance, and eliminate insect and rodent infestations.
Then, when you have to re-roof, have the existing fiberglass removed and convert those boxes into ventilation channels, with continuous soffit and ridge vents. This will dramatically improve the durability of the roof structure and reduce summertime radiant heat gain.
Thanks Robert... that was our first approach & we have not ruled that out at all. We will need a new roof in a few years...and because of the ice damming, it is slightly sagged just above the gutters, so we started thinking about adding it on top instead and doing it now, but we were concerned about the weight on the beams and creating any new moisture problems. I like the idea of venting it later also when we re-do the roof itself.
Yes David, I agree with you also... we don't want any airpockets if we go that route. Would we have any issues with a closed polyiso system in a nonvented application?
We have similar but different question. We have a modest sized (2000 SF) mid-50's modern home on Lookout Mtn. at 7500 ft. elevation in the foothills just west of Denver, CO, with an open cathedral ceiling with 4x10 beams on 52 inch centers and square (not beveled) 7 inch tongue and groove roof decking -- and no roof insulation. We are living here hear-round now and need to reduce the fuel consumption (natural gas hot water heat). We love the original aesthetic appearance of the ceiling with its full open architectural look and large view windows of both the city below us to the east and the Front Range above us to the west. Previous owner installed a very high quality composition shingle roof only 4 years ago that withstood a very damaging hailstorm earlier this year. We are deciding whether to add insulation internal to the house using about 3.5 inches of polyiso rigid foam and new tongue and groove between the beams, thereby leaving only about 4 inches of the beams exposed (and not reaching the desireable R-value); versus removing the roofing and adding polyiso SIPs above the old roof deck and installing new roofing, thereby getting a much higher R-value and retaining the original aesthetics inside the home. Any advice regarding the cost and other tradeoffs associated with this decision? Especially, roughly what the cost difference would be per SF? Thanks
Tom,
It is far preferable to put the polyiso on top of the roof sheathing, for two reasons:
1. To address thermal bridging through the rafters, and
2. To get a higher R-value.
You should be aiming for R-40 to R-60.
We are still working on getting the contract lined up for this. Would we need a vapor barrier between the fiberglass panels and the new polyiso panels or would this allow for trapped moisture? thanks!
oops moving comment to the new construction vaulted ceiling thread
Lara, you don't need an additional vapor barrier. Your polyisocyanurate panels are already acting as a vapor barrier.
Gents,
I'm curious, when considering the unvented "hot roof" approach, what R-value should someone like Lara aim for to be safe? Is it a matter of calculating the dew point to determine whether condensation would be an issue?
This last summer I noticed the failure of some Not-So-Old roof shingles.
The Location was Westford MA
The roof was compact, HIGHLY insulated and unvented.
The worst failure was on the West facing slope of the roof.
I wonder if the extreme insulation was causing the composition shingles to experience Extra-EXTREME temperature variations.
With any roof system, you aim for the minimum IECC R-value requirement for your climate zone, and then try to exceed it.