How the heck was Pittsburgh, PA named a green city?!

I need some help finding a home builder in Pittsburgh, PA (preferable southwest PA).
My husband and I have had passive solar home plans drawn up and I would really like to build with SIPs. After researching everything… it just seems like building with solar passive strategies and conventionally framing is it, is like wrapping a diamond ring in the comics.
For starters, I’m having hard time finding a contractor in general. I make phone calls, emails, but very few responses. Add to that, the ONE contractor we have had a sit down with, is not interested in building with SIPs (and I completely understand why if their fee structure would mean they’d actually lose money….but come on!) I’ve actually emailed all the SIPs dealers and asked them for connections, but most of them have installers, but no contacts to GCs.
So….does anyone have a friend or contact out this way (zip code 15312), that would be willing to GC a single family SIPs home??
I’m real close to getting an owner-builder loan and being my own GC and that just makes me want to cry (I DO NOT have the sanity for it).
Thanks in advance. I really appreciate any ideas or leads.
GBA Detail Library
A collection of one thousand construction details organized by climate and house part
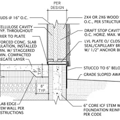
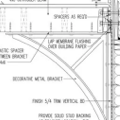
Replies
Just curious, but what's the magic of SIPs, for you?
They're easier to air-seal than stick built, but when all the insulation is 1.5 polystyrene (or worse, 2lb polyurethane) the lifecycle environmental impact of the polymer is pretty high. An EPS core SIP may be "green enough" at code min, but at higher R, not so much.
In a US zone 5A location R13 2x4 + R5 insulating sheathing is code min, which has a whole-wall R of about R15 "whole wall" after factoring in the thermal bridging and adding the insulating value of the structural sheathing, wallboard and siding. To hit that with an EPS core SIP takes a 5" SIP, which has ~4" of foam a bit more than 2x the amount of foam it takes to do with an R13 + R6 (1.5" EPS) assembly that's slightly better than code min.
If you want to go 1.5x code min you'd need R22-R23 whole-wall, which can be done with 2x6/R20 + 2" of EPS (or rigid rock wool, which is lower impact) sheathing, but with SIP you're looking at 6.5-7", which is again ~3x the amount of polymer of the fiber-insulated stick built with foam insulating sheathing of similar performance, but its' also starting to be a substantial amount of foam. At R30 whole-wall (about the most that's financially rational in a zone 5 climate, and maybe not if building with SIPs) It's a 9" SIP, whereas similar performance can be had with 2x6/R20 + 3" of 1lb density polyiso.
With polyurethane SIPs you can get there with thinner SIPS, but it's higher density (= more than 2x more polymer per R), and so far almost all of it is blown with HFC245fa, which has a global warming potential nearly 1000x that of CO2. Both EPS and polyiso are blown with pentane, at about 7x CO2. (XPS is blow with HFC134a, which is even worse than HFC245fa.)
The higher-R the assembly, the more the environmental impact of the insulating materials start to matter. Foam is great when used for moisture control, but far from green at high-R. You can hit any arbitrary performance point using much lower impact materials, and hit SIP performance with a fraction of the total amount of foam.
Well Dana, I'll admit alot of what you just posted is a foreign language to me. But here's the magic for me. I can't quantify it with code or R values. I'm merely a home owner that wants to reduce heating bills
1) A reported 50% energy savings (even if that if an exaggeration, I'll take 25%). A reduction in HVAC system because of the seal. I understand I can probably get this with a good build with spray foam insulation. Also, because of the passive solar design, there will be alot of windows. On a sunny day in the winter, hopefully it wont be much of a problem, but that's only 50% of the winter.
2) Having the house under roof in a week is very appealing to me. Our weather is a bit unpredictable here and I can drive around the area and point out more houses that have been sitting open to the elements longer then they should be. I dont know what the problems are there, but it seems unless you're building a mcmansion in a plan, you're house is going to sit in a half framed state for a while.
3) And while I understand that the "costs" balance out (material cost is higher, labor cost is lower), I'm a big fan of efficiency. I know the foam isn't the MOST environmentally friendly, but I would consider It and OSB more environmentally friendly than lumber and the inevitable waste that goes into stick framing. I don't see why anyone wouldn't want to shave 2-3 weeks off a project and cut waste.
After reading some of the cons on SIPS, mainly the foam issues....I can't help but see that contractors are only avoiding it because they wont make as much money putting up SIPs in a week versus the take on 3 weeks of framing labor...(or they just don't want to put in the time to learn a new skill). What I see is, "I can give you the same R value with "this", 'this" and "this" and it'll cost as much as a SIP (and I get paid for an additional 2 weeks of labor)....and then we're actually more expensive then a SIP.
Melanie, it seems to me that if protecting the framing and air and water sealing quickly is very important to you, then zip sheathing is your product. The R6.6 variant for walls should just squeak you in under the limit for 2x4 wall framing. Plus, with the Huber recommended tape it should be a very airtight assembly. It also has a low global warming potential since it's made with polyisocyanurate. I hate to say "should" but in this case I will: that should be important to you.
In the case of roof sheathing one would use a different zip sheathing that only provides the quick air and water sealing, no insulation. Unless you're going with cathedral ceilings then you potentially lose nothing using this approach. Plus, the trades will love zip sheathing as it is a simply product that "generally" install easily and is pretty fool proof. It will then protect the inside trades and stop a lot of the headaches you're worried about.
Now, if you're going for 2x6 framing of walls, well then you'll have to use something else than zip for your location.
Eric,
I think you missed a couple of Melanie's concerns while recommending zip sheathing.
1. The length of time for stick framing. Zip sheathing won't address that problem. It will take just as long as regular sheathing, if not longer due to the taping.
2. Cost. Not only do you still have the same cost due to the framing time, you have the additional cost of zip sheathing.
True, cost and efficiency are my two biggest concerns. Would love to be that person that has 1 million to spend on a house, not so unfortunately. IfI can't find someone to build SIPs, then stick framing it is and I'll look into the Zip sheathing, but I'm pretty sure my architect has it specified at 2x6 because we had the plans drawn at 24" on center in the case we can't do SIPS.
Aaron, I think you are oversimplifying what I said and how it might address Malanie's problems and concerns. First, if she can't find someone qualified to do what she want's locally using SIPs then how is that going to work? Also, training and ordering of the correct SIPs is a much bigger deal.
You are wrong that zip sheathing takes longer because of the taping. It is much faster, even with the taping, because on windows and doors, which are the major components in creating a good air and water seal you just nail sheathing over the framed openings and cut the windows and doors out later. There is not nearly the complication and room for getting things wrong as with the normal stick built house and the type of flashing that generally requires. Flashing windows and doors in a zip system is pretty easy.
Framing a house isn't a very time consuming part of house building. The time consuming part is sealing it up from rain, including the outside sheathing itself. That is why zip is such an advance over normal sheathing in stick built houses, EVEN with the added cost of the sheathing.
Melanie, just saw your post. Yeah, it would probably make it hard to use zips if you are using 2x6 framing. However, I think there might be some on this site who would think it's OK as long as you use dense packed cellulose walls for your location. Cellulose buys you time during the wetting season by migrating the moisture to less moist areas of the insulation, effectively keeping the zip from rotting. You are in a "borderline" so you might be able to get by. This may be far from the kind of construction that you are now planning and are comfortable with, though.
Melanie
I had architectural plans drawn up over a year ago that included SIP's in the Pittsburgh area. They were drawn by Yoki Tai an architect in Pittsburgh and were to be built by John Cummings of Cummings Construction, who is very reputable. I posted a similar question about SIP's and had a similar post response by Dana which I did in fact heed. I have the same builder and architect but am half way through an addition that is now stick framing with thick EPS exterior foam insulation with a frost protected shallow foundation. Cummings construction is doing the work. It is an excellent outfit- honest, quality work, and reliable. He certainly is not cheap but you get what you pay for. He can do quality SIP construction for you if that is what you want.
Melanie: There are also several Pittsburgh builders listed on the PHIUS website (phius.org), who have studied Passive House techniques and could build you the house you want.
Have you PRICED SIP construction? Versus stick or stick with Zip?
Hi Joe,
I've been trying to price alot of different aspects but running into brick walls with most GCs. For starters there are very few in our area interested in building with SIPS. We just found a guy 7 miles away from us, but he pefers not to GC, which is fine...because I'm pretty certain we're going to contract it out ourselves.
I have not been able to price ZIP but here are the numbers I'm coming up (for materials). These are for 1900 sq foot rectangular house with garage:
Conventional Framing "Dry-In" package as quoted by 84 lumber: $58k
Includes:Exterior and Interior Framing/sheathing, subfloors, roofing, windows (11K included in the package quote). I've probably over-estimated insulation at 5k (included in above number) to possibly get the same effect as SIPs.
SIPs "Dry-in" package: $70k
Includes: Shell of house in sips (4 quotes all averaged $40K). Interior framing, garage framing, roofing, and windows numbers were taken from my 84 lumber quote (included in the 70K).
I was quoted about $20K (by SIPs dealers) to bring in a team (from another state) to install the sips.Considering its only supposed to take about 3-5 days, I'm not willing to go this route. I also had a GC tell me SIPs weren't worth the added money (which doesn't look like TOO much added money to me if I can get a local install). I look at it this way....Sure, I can get stick framing with foam insulation probably cheaper in materials...but with labor costs, you're looking at 5 days with SIPS opposed to 15-20 days with stick and foam.
Not all foams have the same environmental impact. If you build with SIPs, PLEASE go with an EPS core (and a 50% fatter wall for the same performance) rather than a polyurethane SIP. The blowing agent used for closed cell polyurethane are more than 100 times more powerful greenhouse gases than those used for EPS or polyisocyanurate foam.
You don't need spray foam to make stick-built as tight (or tighter) than a SIP. A SIP is inherently easier to air seal than stick built, but that's not to say they are always detailed as tightly as a pretty-good stick built house. Caulking the framing to the sheathing at every stud bay and stud plate, and sealing the seams of the sheathing to detail it as a primary air-barrier is not difficult or very time consuming, but somebody has to direct & inspect to ensure that it gets done. Somebody has to direct & inspect the seams & transition sealing of SIPs too.
In a calendar-time-is-money perspective there is sometimes an economic rationale for going with SIPs, but only rarely on price/performance basis, even in high labor cost markets.
Regarding ZIP-R, in a zone 5 location you have to de-rate the ZIP pretty severely since the insulation used (polyisocyanurate) loses half it's performance when the average temp through the foam (not to be confused with the outdoor air temp) is below freezing, making it of limited improvement for you. From a labeled-R point of view 1.5" ZIP-R looks better than the R13+ 5 code min, but from an actual performance point of view it probably isn't. It goes up more quickly than an exterior-foam R13 + 5 solution though, and if you used R15 rock wool batts obsessively-fitted you'd do slightly better than code-min with a ZIP-R approach. Using a smart vapor retarder under the sheet rock is recommended as cheap insurance against mold, since the actual performance of the ZIP-R will be considerably lower than labeled performance in winter.
Don't make the mistake of too much passive-solar glass. More glazing means higher heating/cooling peaks, even if the average energy use goes down, and it's all too easy to go overboard and end up with uncomfortable overheating (even in winter), unless you design in sufficient compensating thermal mass.
If you are still looking you could try Chris Klehm with JENDOCO Construction Corporation or Ernie Sota. They may not do the work but would know contractors in the area who might.