How should moisture/vapor wetting and drying be considered in this situation?

Details:
– Climate Zone 6, Marine setting
– Stand alone garage(1970’s) to be converted to an overflow guest house w/ full bath no kitchen.
– Guest house to be used in summer only.
– Existing structure on a floating slab w/ no vapor barrier beneath, sitting poorly drained soils.
– 20′ by 16′ area w/ cathedral ceilings, 2×4 walls and 2×8 rafters
– 20 mil vapor barrier to be installed over slab (seams taped), may not be able to extend under existing perimeter walls.
-2×4 sleepers laid flat over 20 mil VB
-1 1/2″ xps fitted between sleepers
-1/2″ subfloor fastened to sleepers w/ engineered finished floor
– Walls/Ceilings insulated w/ rockwool batts
– 1/2/ drywall for interior cladding painted w/ water based paint
– Bath to be vented to exterior
– Existing exterior cedar shingle siding to remain, asphalt roof shingles to remain.
– Gutters and downspouts added to move bulk water away from slab perimeter
Questions:
– If VB cannot be extended under perimeter walls and there exists no capillary break between slab and bottom plates will moisture getting into wall cavities present a problem?
– Should vapor barrier extend along walls/ceilings to force slab moisture getting into walls to dry to the outside or should a smart membrane be used to to allow drying to both inside & out?
– Can someone walk through the building science concerns I need to consider here?
Thanks
GBA Detail Library
A collection of one thousand construction details organized by climate and house part
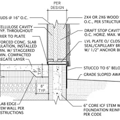
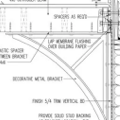
Replies
Keep the VB (10 mil would be fine), but skip the sleepers, and use EPS instead of XPS.
The sleepers are nothing but a thermal bridge, and will collect moisture on the cold underside over a winter unless the slab has substantial edge insulation, and even then would collect moisture during the summer if it's zone 6A (coastal Maine or the southern parts of the Canadian maritimes.) Instead, TapCon the subfloor to the slab through the foam. Don't sweat the amount of wicking you would get from the fastener penetrations of the vapor barrier- it's miniscule. When fully supported by a slab the foam won't compress much (far less bounce than 3/4" subfloors between 16" o.c. joists), even with just half-inch subflooring. Just be sure that half-inch subflooring has sufficient fastener retention for your finished floor's fastening system.
XPS is blown with climate damaging HFC blowing agents, and as it loses the HFCs over a few decades it's performance drops to that of EPS of similar density (about R4.2/inch when fullly depleted.) EPS is blown with comparatively benign pentane, which dissipates quickly (the bulk of which is often recaptured at the manufacturing plant and burned for process heat), and it's insulating performance doesn't drift over time. The energy use difference between an R7.5 floor (1.5" XPS) and an R6.3 floor (1.5" of Type-II EPS) in a room that isn't fully heated over the whole winter is pretty small, and the R7.5 is only temporary- it'll eventually become R6.3.
If the studwall's bottom plates haven't already wicked enough moisture into them to cause a problem they won't be much worse off after insulating. If it's easy to jack up the walls to slip in some EPDM or 10-20 mil polyethylene do it, but if not, don't worry. The bigger moisture threat would be if there isn't sufficient roof overhangs to limit direct wetting of the siding, particularly if the siding isn't back ventilated with a rains-screen. Vinyl siding would be good enough, cedar shake siding is only somewhat back-ventilated, but with roof overhangs of a foot or more per story of height (two feet or more would be even better, bungalow style) the amount of direct wetting is pretty limited.
In a zone-6 climate you'll need some sort of interior side vapor retarder for the walls, even IF it has back-vented siding. The cheapest solution would be half-perm paint, aka "vapor barrier latex" primer, but 2-mil nylon (Certainteed MemBrain) would allow faster drying toward the interior, yet would still be low-permeance during the winter, when it counts. For a building that isn't occupied during the winter the moisture drives from the interior are pretty low, and odds are it would be just fine without vapor retarders, but if you ever envisioned occupancy for the 10 coldest weeks of winter it would be good to have them.
The ceilings would need at least a 1" soffit-to-ridge vented airspace between the insulation & roof deck, so you'd be fine with R23 rock wool (5.5" nominal) and 2x8 rafters (7.25' nominal). You'd have 1.75" of vent space, which works fine with the 1-1.5" round retrofit soffit vent plugs with bug-screens.
Geoff,
You'll end up with a thermal bridge at the slab perimeter. The best solution is to install vertical rigid foam insulation (dense EPS would be best) at the perimeter of the slab. The rigid foam should be at least 2 inches thick -- 3 inches is better -- and should extend at least 2 feet below grade.
Of course you will need to protect the above-grade portion of the rigid foam with something like metal flashing or pressure-treated plywood, and you'll need Z-flashing at the horizontal seam between the bottom course of siding and the top of the rigid foam.