How much oil to make foam?

Foam insulation was the miracle insulation for green builders.
Now it has a bad rap because of the amount of oil used to manufacture foam.
Does anyone know how much oil is used to produce the varios types of foam?
Would like to put in perspective what the foam really costs.
GBA Detail Library
A collection of one thousand construction details organized by climate and house part
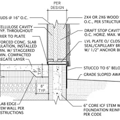
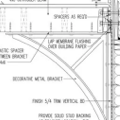
Replies
Richard,
For all intents and purposes, spray foam is 100% petroleum -- unless its is "soy-based foam," in which case it is 93% petroleum and 7% soy oil.
So, if spray foam is 100% petroleum, here is the math:
Petroleum has a density of 6.846 pounds/gallon.
So one gallon of petroleum yields 13.7 cubic feet of open-cell foam (at a density of 0.5 pound per cubic foot) or 3.4 cubic feet of closed-cell foam (at a density of 2 pounds per cubic feet).
Well, there are other "costs" to consider
https://www.greenbuildingadvisor.com/blogs/dept/musings/calculating-global-warming-impact-insulation
i think the better question is, what type of end products made from oil are used in foam, how much of each is used, and are the end products abundant anyway because they are by by-products of mainstream oil processing for things like fuels and such.
an example would be using ethanol in automobile fuel. if that ethanol is of the corn derived type, well then there are lots of negatives. however if it is cellulose derived, well it is made from the waste products of traditional food growth and wouldn't be so bad at all, relatively speaking.
many oil derived items exist only because we consume so much fuel derived oil, fuel processors had to create secondary markets for all the by products, waste, etc left over.
i'm not sure that you could say 100% of the product is oil derived. 100% of the product may use oil and other items as source ingredients, but it doesn't mean it is 100% oil. it is also possible that a foam is more than 100% oil by volume if it took more oil to create / synthesize all the chemicals that are in it, ie say a fire retardant.
you could even go further, although it would be difficult to know, and figure out if the oil used came from a more environmentally sound manner, or say something a bit more ugly like tar sand extraction.
i doubt any of the manufacturers would offer their trade secrets for us to get a final answer
i'll take a shot, but i'm no chemist...
the MSDS for DOW Styrofoam (blue board):
[also note that EPS insulation foam could easily be made from recycled styrene and recycled itself, but collection is expensive due to size and compaction needs]
> 2-Propenenitrile, polymer with ethenylbenzene cas9003-54-7 > 60.0 to 1,1,1,2-Tetrafluoroethane cas811-97-2 >= 5.0 to Styrene, polymers cas9003-53-6 >= 0.0 to with Extruded styrenic polymer foam containing a halogenated flame retardant system.
the first item is born from:
Styrene acrylonitrile resin is a copolymer plastic consisting of styrene(1) and acrylonitrile(2).
The relative composition is typically between 70 and 80% styrene and 20 to 30% acrylonitrile [unknown what it is for insulation board].
1)styrene (aka vinyl benzene) is produced in industrial quantities from ethylbenzene(4)
4)ethylbenzene is prepared on a large scale by alkylation(5) of benzene(6) with ethylene(7)
5)in oil refining contexts, alkylation refers to a particular alkylation of isobutane with olefins??
6)Four chemical processes contribute to industrial benzene production: catalytic reforming(8), toluene hydrodealkylation(9), toluene disproportionation, and steam cracking. catalytic reformats accounted for approximately 44–50% of the total U.S benzene production between 1978 and 1981.
8)catalytic reforming, a mixture of hydrocarbons with boiling points between 60–200 °C is blended with hydrogen gas(10). hydrocarbons are sourced from oil or natural gas
10)Commercial bulk hydrogen is usually produced by the steam reforming of natural gas
9)Toluene hydrodealkylation converts toluene(11) to benzene in this hydrogen-intensive process
11)Toluene occurs naturally at low levels in crude oil and is usually produced in the processes of making gasoline via a catalytic reformer, in an ethylene cracker or less often, making coke from coal.
7)Ethylene is produced in the petrochemical industry by steam cracking. In this process, gaseous or light liquid hydrocarbons are heated to 750–950 °C, inducing numerous free radical reactions followed by immediate quench to stop these reactions. This process converts large hydrocarbons into smaller ones and introduces unsaturation. Ethylene is separated from the resulting complex mixture by repeated compression and distillation. The process is extremely energy intensive.
2)Most industrial acrylonitrile is produced by catalytic ammoxidation(3) of propene(4):
3)ammoxidation is done using ammonia primarily sourced from natural gas (could come from natural waste though in small quantities)
4)propene is produced from fossil fuels—petroleum, natural gas, and, to a much lesser extent, coal. Propene is a byproduct of oil refining and natural gas processing. During oil refining, ethylene, propene, and other compounds are produced by as a result of cracking larger hydrocarbon molecules to produce hydrocarbons more in demand. A major source of propene is cracking intended to produce ethylene (see #7)
the second item is the gas aka HFC-134a [CH2FCF3]:
made from basic raw materials (crude oil, natural gas, sulphur and fluorspar). production requires limestone, water and transition metal catalysts, in addition to the basic raw materials, and that the energy required to provide these raw materials is the equivalent of 4.52 tonnes of CO2 per tonne of product. Environmental releases associated with HFC-134a included waste salt brine (to the sea), mine tailings (mainly “country” rock landfilled at the mine) and small quantities of calcium sulphate and spent catalyst (both sent to landfill). In addition, greenhouse gases amounting to the equivalent of 2.1 tonnes of CO2 per tonne of product were emitted to the atmosphere from the plants studied. The global warming potential of HFC-134a is 1300, meaning that, during the first 100 years following the release of one tonne, the effect on climate change is equivalent to 1300 tonnes of carbon dioxide. Consequently, the 6.6 tonnes of carbon dioxide equivalent, emitted during production in the form of energy required and other greenhouse gases, is of relatively little importance and the key requirement to reduce environmental impact is containment during use.
() i've grown to lazy to go into all the items used
the third item is polystyrene:
polystyrene is an aromatic polymer made from the monomer styrene(20), a liquid hydrocarbon that is manufactured from petroleum
20) Styrene (aka vinyl benzene) is most commonly produced by the catalytic dehydrogenation of ethylbenzene(see #4 above) also Ethylbenzene is mixed in the gas phase with 10–15 times its volume in high-temperature steam, and passed over a solid catalyst bed. Most ethylbenzene dehydrogenation catalysts are based on iron(III) oxide, promoted by several percent potassium oxide or potassium carbonate.
finally the flame retardant:
Halogenated flame retardants are chemical compounds containing chlorine(30) or bromine(31) bonded to carbon.
(30)elemental chlorine is usually produced by the electrolysis of sodium chloride dissolved in water.
(31)Bromide-rich brines are treated with chlorine gas, flushing through with air. In this treatment, bromide anions are oxidized to bromine by the chlorine gas. Bromine is mined.
Bob,
Wow. Thanks for this analysis. I get the impression that it's misleading to evaluate the environmental implications of different insulation products merely by that chart often linked on GBA, discussing blowing gas and global warming potential. That doesn't take into account the whole process. For example, there are evidently many different chemicals created or utilized in the process of manufacturing foam plastics, and potential hazards (say for GWP and toxicity) along the way to the final process included in that chart. In contrast, this is most likely not also true for shredded newspaper.
Bob,
Thanks for your informative answer. It provides a wider and more illuminating perspective, obviously, than my simplistic back-of-the-envelope analysis.
TJ,
Concerning your point that "it's misleading to evaluate the environmental implications of different insulation products merely by that chart often linked on GBA," I addressed that point in my article, as does David White when he speaks about it. As the article states, "White is forthright about the calculator’s limitations. 'We are not talking about any environmental impacts other than global climate change,' said White."
Martin,
What I'm thinking here is that the chart references the volume of insulation required to achieve a certain R-value, and extracts GWP based on the installed material density. What it doesn't measure is the material shaved off after installing open cell foam, or the residue inside discarded canisters for foam kits, or any byproducts of the manufacturing process. This last category could be quite significant, even many times greater GWP than the end product.
don't forget TJ that it is hard to calculate teh waste, transport, handling, or by products because even the same product can be down proper or improper.
by products often have uses, so it may not be negative. or those uses could be troublesome. using a by product could be a good thing, unless it encourages use of a product further up the chain that is not so good as it becomes more economical when its by product has a market.
sometimes it is more luck that certain products are 'greener', like blown cellulose.
we may reach a point where recycled newsprint is not available or cost affordable and raw sources would be used.
there is also the potential tradeoff...
say for example that cellulose, if i use recycled newspaper to make it, there is less recycled newspaper to say make more newspaper. while it may not directly do harm, it may encourage others too. this is an effect found in some home energy solutions. if you think your washer is effecient, you don't feel the need to ration its use and use it more often or use more hot water.
it can even boil down to how the end user uses a product