How is Zip-R safe in cold climates?

I assume I’m missing something, as I’m seeing Zip-R chosen by experienced and reputable builders. But it sounds like a dangerous assembly to me from a water perspective, and I’d love to be corrected.
Zip-R insulation is vapor-closed. The insulation is between the studs and the sheathing. The interior of the polyiso can be a condensing surface if the insulation is not thick enough. I’m seeing Zip R6 used in cold climates like Boston, which is not enough to eliminate the dew point in the winter (especially considering that polyiso does not actually perform as R6 when it gets cold).
Isn’t it almost a certainty that moisture will accumulate on the interior of the polyiso, leading to rotting the studs?
GBA Detail Library
A collection of one thousand construction details organized by climate and house part
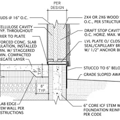
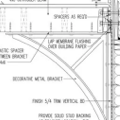
Replies
Zip-R isn't vapor closed; the OSB is the least permeable layer so it performs similarly to regular OSB. But I'm still uncomfortable using it without having enough R-value in the foam layer to keep the inner surface above the dewpoint temperature. In Boston, Zip R-9 over a wall insulated with R-20 cavity insulation would be safe. The polyiso performs worse at cold temperatures so Zip R-9 should be considered closer to R-7.5.
Thank you for the response!
Ah, I guess I was incorrect that it's vapor closed. I checked the product spec, (https://www.huberwood.com/uploads/documents/technical/documents/Product-Data-Sheet-Wall-R-sheathing-ZIP-System.pdf), the insulation is <1.0 perms, so it's a class 2 vapor retarder.
I can't tell from the product spec what the permeability of the OSB is, but I imagine it's more permeable than a class 2 vapor retarder? So won't the insulation be a condensing surface and trap the moisture more than OSB would?
No, the OSB is around 0.5 perms. That's when it's dry; when it gets wet it opens up to somewhere around 10 perms. 1" of the glass-faced polyiso they use is about 1.5 perms. The water-resistant coating is around 13 perms. They don't publish the OSB perm rating because it varies with location (aspen in the north, pine in the south), panel thickness and moisture levels, but there is information available elsewhere, including here on GBA, that shows typical ranges.
Thank you Michael!
Michael,
The R20+7.5 Zip-R wall in Boston will have an inside foam surface temperature of 41 degrees F, just 1 degree above the dew point temperature at 70 degrees F and 35% RH. This according to the methodology referenced in Martin's article "Are Dew Point Calculations Really Necessary?" which also references the dew point temperature at 70 degrees F and 35% RH as the "safe" wall metric. With respect may I please ask:
1. How has the dew point temperature at 70 degrees F and 35% RH become the "safe" wall metric?, and
2 Is that a sufficiently conservative "safe" metric even though many homes will have higher humidity?
Thank you.
70F/35% is essentially a reasonable number that the folks writing the code had to pick to come up with the tables. There is nothing special about it but if you conditions are different, you need to adjust your design, for example a wall around a pool built with R20+7.5R is guaranteed to fail.
If you like to run your house more humid than that number you can run it through one of the on-line calculators such as:
https://www.ubakus.de/en/r-value-calculator/?
One simple way to make a standard assembly safer with higher humidity is by including an interior class II vapor retarder (smart membrane or faced batts). This this work as a vapor throttle in the winter time but still allow the walls to dry the rest of the year.
Keep in mind that in colder climate your windows tend to be the limiting value on interior humidity. Unless you have high efficiency windows, in cold climate even 35% RH might cause window condensation.
If I recall correctly, the code language is derived from Building Science Corp testing or modeling at 45% indoor RH. The idea is that a vapor retarder will even out some of the extreme conditions and that the wall can survive a bit of wetting each year, as long as it doesn't occur long enough for it to be a problem. That's obviously cutting things very closely so I urge people to consider the code ratios the bare minimum, to upgrade the interior vapor control to a variable permeance membrane, to use aged, conservative R-values for the foam, and to monitor their indoor RH.
That's pretty much my understanding too. The thinking is that if things get below the dew point a few times at the coldest time of the year, that's OK as long as there is a lot of time for it to dry out throughout the rest of the year. The problems come when the moisture adds a little, loses a little -- but not all, then adds a little more, and gradually builds up to where there is a problem. As long as the insulation ratio is sufficient to avoid that "building up" part, the assembly overall is OK.
I like to be a little conservative and go with more exterior R, and usually an interior smart vapor retarder too, just to be extra sure. I did have one project where we had to allow for 40-50% interior RH values in the wintertime, so we used about a 60/40 exterior to interior R value ratio to design for those higher humidity levels and still keep things safe.
Bill
I guess part of my concern with the Zip-R6 (and even Zip-R9) assemblies in Boston is the fact that moisture is a certainty, AND it will be slower to dry given the polyiso's property of a class 2 vapor retarder.
It sounds like to be safe, a class 2 vapor retarder smart membrane is a must?
Lots (and lots) of people use exterior rigid foam, usually on the exterior face of the sheathing. As long as you use at least enough to hit the required ratio for your climate zone, you're fine. Zip-R puts the exterior rigid foam between the exterior sheathing and the studs, which means that sheathing actually has MORE drying ability to the exterior, since the polyiso layer in on the "warm" side of the sheathing, helping to keep interior moisture from reaching it. In this regard, I think Zip-R is actually a little safer than the usual way of putting up seperate exterior rigid foam.
An interior side smart vapor retarder will always make the assembly a little more robust, but it's not always needed.
Bill