How green is passivhaus?

I’m looking at common passivhaus details, which basically consist of wrapping the house in a very, very thick layer of petrochemical based insulation and I’m wondering, has anyone done a comprehensive study on the greenhouse warming potential (GWP) of a house detailed this way, compared to other high insulation options such as wood framed double walls packed with cellulose?
I’ve seen plenty of data on individual building materials. But it’s the total system that matters, as that is what gets built in the real world. And of course it would have to be considered over the life of the structure, say 100 years minimum.
If any of you know of such studies I’d appreciate some pointers. Thanks.
edit – in response to the comments received, yes, I know already that Passivhaus is a performance, not a prescriptive standard. Passivhaus is not what my question is about. My question is about comparisons between achieving high insulation levels using insulations like XPS and polyiso, (a solution I’ve seen in many recent Passivhaus projects) versus using insulations like cellulose or mineral wool. How do these compare in terms of GWP? I’ve seen plenty of data on the insulation products individually. But I’d like to see some analysis for whole house systems, and considering a long time frame, such as 100 years.
I’ll put it like this. Suppose people are considering building a new house. They want to bring it to a very high insulation level, along the lines of what is found in Passivhaus type homes in their area. They have the option of wrapping the house in XPS or doing it all with cellulose. All other factors being equal (shipping distances from product manufacture point to house site for example), and considering a long time frame such as 100 years, because in my view the houses we build should be expected to last, what is the global warming potential difference between the options I’ve mentioned?
GBA Detail Library
A collection of one thousand construction details organized by climate and house part
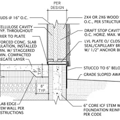
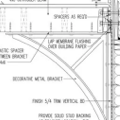
Replies
I think you're asking the wrong question, and let me explain why.
When the modern environmental movement started in the late 1960's, it was all about systemic change. We got the Clean Water Act, the Clean Air Act and the EPA. Very quickly, the people who ran polluting industries realized that systemic change would affect their profitability disproportionately, so they pushed -- quite successfully -- an alternative vision, where the key to protecting the environment wasn't systemic change, but rather personal choice and social responsibility. Because they saw -- quite correctly -- that if it was left to consumer choice people would choose what was easiest, cheapest and fastest for them. That's how our capitalist system works.
Getting back to the original question: in many situations, the easiest, cheapest and fastest way to insulate a house is to use XPS foam. Until very recently that foam was only available in formulations that produced significant amounts of greenhouse gases in their production, to the extent that there was probably net negative environmental benefit to using that foam. Recently available new formulations are somewhat better and probably deliver net positive benefit. But the question isn't why were people using that foam -- they were acting in their own self-interest. The question was why was it available for sale, or more subtly, why was it available for sale at a price that didn't factor in its environmental consequences?
The problem isn't with the passivhaus standard -- which doesn't mandate foam -- but with our entire framework of environmental regulation.
Any building that qualifies for the Passive House/Passivhaus standard is going to require very little energy to operate. The electric bills will be minimal, because the home is well insulated, airtight, and designed with purpose. That's the point.
But that only covers _operational_ carbon. You can calculate, essentially, how many barrels of oil, or cubic meters of gas, etc. would be required to generate the wattages required. And to that end, Passive is superior to the average building by a huge measure.
The next level of building design also concerns _embodied_ carbon. Architects and designers are indeed asking these questions. Can we use less concrete? Can we use local materials? Can we use plant based materials to replace petrochemicals? And you're seeing some really cool results. Mass timber is replacing steel structures. Foam glass is lessening the concrete needed. Hemp and wood fiber are replacing foam for insulation, etc.
The Passive standard doesn't govern embodied carbon, yet, so you can't at once say "Passivehaus is green" — you could have two buildings achieve the qualification with two very different levels of embodied carbon. But anyone know even knows what Passive House is, is going to be thinking along the lines of "how we can have less impact, be more resilient, and use better materials. "
An interesting question.
Googling "life cycle assessment of passive house buildings" yields quite a few results, though many are pay-to-play.
I agree with the above posters that the question is perhaps a bit too broad or imprecise. Scott hit it on the head in that Passive House (or Passivhaus) is really an efficiency standard and nothing more. It is not a system of building. Analyzing the materials themselves (and sure, the labor to install them perhaps) probably IS the more useful way to go about it in a practical sense.
If one really wanted to get into the weeds of life cycle assessment (as perhaps we should) we would have to include quite the range of factors that has little to do with the passive house standard. One could conceivably imagine a list of buildings from 'most green' to 'least green,' and what determines the order for all but the margins would very likely be things that have nothing to do with a building standard. Like where the building is located, how far away the occupants work and shop, how dense the housing is, what the climate is like (HDD), the size of the structure, etc. One could go deeper. Living in a yurt in a fair weather climate will probably always be greener than any passive house by an immense amount.
Insofar as the question is "will the extra work/materials to get to the Passive House standard FOR AN OTHERWISE IDENTICAL HOUSE pay back it's debt" it's one that perhaps some studies have attempted to answer. But again... will depend on the specifics of how the standard was reached. I think there is a sense among many here that Passive House goes too far in some cases (in other words, the capital expense is too high for the small future benefit). I think the goal of building a very 'green' house is not likely identical to trying to meet PH standards. Many if not most of those interested in PH (in my opinion) care more about performance than sweeping environmental paradigm shifts (and hey I'm guilty of getting caught in the world of performance, as is much of GBA's literature and discussion). But surely it's not mutually exclusive, so a little bit of myopia on performance here and there I'm sure is not the worst thing. At the least we don't want our expensive and high embodied carbon structures to disintegrate via wetting brought about from poorly conceived building strategies.
One last thought. One approach to determining whether meeting a standard pays back it's debt is via simple ROI (how long if ever will we recoup). The problem now is that monetary ROI is a poor proxy for environmental ROI. If it were better, we would probably have an easier time financing the capital in order to lessen the future burden.
So this is what I was getting at in point #1 about systemic change. If monetary cost were aligned with environmental cost, there would be no difference between monetary ROI and environmental ROI. People would be free to make the decision that works best for them, and at the same time would be doing what's best for the environment.
This isn't a new idea, economists have been talking this way since the beginning of economics. They like to talk about taxing externalities. Central to this idea is the belief that environmental issues are practical problems, not moral ones. The notion that environmental issues are moral problems, to be solve through virtuous behavior, is a relatively modern idea, arising in the mid-1970's.
And here's the important point: it was the polluting industries that pushed the idea that environmental issues are best dealt with through a moral, rather than a practical, framework. And they pushed this idea because they didn't want the problems to be solved!
"Living in a yurt in a fair weather climate will probably always be greener than any passive house by an immense amount."
I understand your point here. Any such study, OF COURSE, would have to include some limitations. The study would need to be designed to try to isolate variables as best we can. The point of the study would be to compare specific building components such as a wall or roof section (rather than just isolating the insulation materials and look at those alone). So if comparing the components is what we're trying to do than we need to make some assumptions such as all the materials for various options are being shipped similar distances from their point of manufacture to the construction site.
That way we're not unnecessarily introducing more variables, in this case shipping to the site.
If we're concerned about how THOSE variables, such as shipping, influence GWP, then we need a study designed to isolate those as best as possible.
Conceptually this is pretty straight forward. The actual study design might be a bit complicated, but this sort of thing is done all the time.
There are kinda sorta two views to "green" building. The first is energy efficiency, which is trying to minimize how much energy the home uses, which typically involves insulating and high efficiency appliances (I'm in this group). The second view is to use materials primarily derived from things that can be grown (plant stuff, mostly). There are some tradeoffs either way, as is usually the case.
I don't like thinking about energy as if it's equivalent to carbon, because it's really not, so I generally don't consider that part of things. I look at this more as a resource allocation problem, and in that case, the economics of the materials help to guide you towards the most efficient use of resources. If polyiso will save enough money to at least pay for itself during some interval of time, maybe your mortgage term, then that polyiso was a good use of resources, since it essentially offset the additional energy that would have otherwise been required to heat or cool your home. In this way, you are maximizing your efficiency in terms of resource utilization, getting the most for the least -- and "least" here doesn't just mean cost, it means less "stuff" used as input materials (for either building materials or energy generation).
If you think in terms of efficiency instead of trying to minimize your use of any particular product, you always win, since you are always minimizing your use of everything -- materials AND energy -- overall.
Regarding a few of your specific points, 100 years is probably excessive for the life of a typical home. Also, plastics do not necassarily mean "petrochemical based" for two reasons, the first is that natural gas is often used as a feedstock, not oil, but sometimes ethanol is used (look into "biopolyethylene" for an example), in which case the plastic material was essentially made from corn. Regarding "polluting industries" not wanting to solve anything, that's probably a bit extreme. I think most would agree that they don't want to make problems, but there will be some bad players out there. Some regulation is certainly required to set standards in terms of emissions and the like. The issue is that the regulations will sometimes go overboard, usually due to well intentioned regulators that don't really understand the complexities of what they are trying to do, and then you end up with a regulation that requires more "stuff" than it reduces -- you can sometimes create a worse problem overall by trying to go overboard fixing some relatively small issue. It's important to always consider the entire system, and not to become overly focused on any particular part of a complex problem.
Bill
Bill -
"plastics do not necassarily mean "petrochemical based""
Yes, there are alternatives such as corn based products. But the 4 'plastic' insulations that are far and away the most common in house construction are XPS, Polyiso, EPS and PUR. The feedstocks used primarily come from the petroleum industry. Natural gas IS a fossil fuel and its production and use have a significant greenhouse effect, though not as much as petroleum.
The point of my question was clear. There are alternatives such as cellulose. I was curious how they compare, when viewed as a whole house system. That's all I was asking.
You all wrote interesting things. Thanks.
Unfortunately no one seems to have an answer to my question which was characterized as "the question is perhaps a bit too broad or imprecise," although I think it was specific enough to get my point across.
"has anyone done a comprehensive study on the greenhouse warming potential (GWP) of a house detailed this way, compared to other high insulation options such as wood framed double walls packed with cellulose?"
It seems people latched onto the word "Passivhaus" and kind of missed my main point. Yes, I know it doesn't mandate petrochemical insulations. It's basically a performance standard. (I'm not entirely new to this.) But wrapping houses in thick layers of polyiso or XPS seems to be a very popular solution. Many of the houses I see being built and pointed to as models for some new, better approach, are using massive amounts of petrochemical insulation. There ARE alternatives. I'd be curious to see if any good studies are being done that consider whole systems, life cycle assessments and GWP. If anyone knows of such studies I'd appreciate a reference.
As an aside -
"Regarding a few of your specific points, 100 years is probably excessive for the life of a typical home. "
Why? I live in a home that is 120 years old, with stone walls, a slate roof, and its original windows. With minimal maintenance it should last another 130 years at least. I put 100 years because some time frame probably needs to be considered to do a study and anything less than 100 years seems to me irresponsible. The notion that we should be building things like houses to last 50 years or less is very dubious, especially when we can build them to last 250.
DCcontrarian, no, I'm not asking the wrong question. I'm asking the question that interests me, which has to do with an analytical look at the GWP of various insulation approaches to achieving an energy efficient building shell. Your questions and points are interesting as well. But they weren't what I was asking about. Nonetheless I appreciate your comment. Thanks.
Jollygreenshortguy,
I understand the frustration of feeling like your point is being missed (happens here all the time and we mostly like to talk about what we know). I wouldn't take it personally. I think i understand the gist of your question I find it interesting. and I did mention search terms that seemed to yield many-- perhaps relevant-- results. Did any of those results look like what you are after?
>"Conceptually this is pretty straight forward. The actual study design might be a bit complicated, but this sort of thing is done all the time."
I guess im still not clear what you are teying to isolate. On the one hand you are talking about a system, but on the other you seem focused singularly on the petrochemical foam and want to isolate variables. Are you essentially saying you want to include the other system components like fasteners or additional strapping, membranes, etc. In addition to said foam?
Hi Tyler, your original reply was helpful and I am following through on the search terms you mentioned. Thanks.
I edited my question and added a portion. The last paragraph might make my intention clear as far as systems. I'm not being nitpicky about the number of additional straps and screws. Things like that will have next to no additional GWP impact anyway. I just want to see a larger context considered, thus a reasonable figure for the lifetime of the building. I want to be able to make a decision that actually considers a building over its lifetime, not just the GWP impact of a material's manufacture.
I've seen data that compares insulations to each other in terms of GWP. But they look at the insulation materials in isolation and apparently only consider their manufacture. The table in this article is an example of that. https://www.buildinggreen.com/news-article/avoiding-global-warming-impact-insulation
That kind of data is no doubt a necessary component of the type of analysis I want. But it's just the start. I want answers about real buildings over the course of their lifetimes, with insulation being the variable examined.
What difference does it make if I choose R-00 mineral wool for my exterior continuous wall insulation instead of R-00 XPS? That's the kind of question I'm getting at.
I have found one article that's helpful. Here's a link to it if you're curious about this as well.
https://www.greenbuildingadvisor.com/article/choosing-low-carbon-insulation
I guess more work needs to be done in this area.
Thanks again for your replies. They have indeed been helpful.
Many homes will get demolished within ~50 years or so. If you're trying to be green, it doesn't make sense to try to build a house to last longer than it's likely to need to last, since making it last longer will generally required more or different materials. I'm not saying that's the ideal situation, but that seems to be reality in many areas. The house itself, if no one decides to demo it and build a new one, should be able to last 100 years, although there will be maintenance items in that time frame, especially regarding any "active" systems (mechanicals like a furnace, blower, etc.).
There are some alternatives to foam insulating materials, but they all have their tradeoffs. Natural materials (by "natural" I mean things like wool, straw, etc.) tend to be more prone to decay, because little critters can eat them, and they can degrade (rot, etc.). Nature basically repossesses the materials over time. If you want to counter that to get to your 100 year goal, you either have to treat the materials with something to deter decay, which means chemical stabilizers, pesticides, things like that, or go with a synthetic material that nothing will try to eat so it won't degrade with time. That's the tradeoff. If you go with a material like mineral wool, which is long term stable and doesn't need to be treated, the tradeoff is a relatively high amount of input energy to manufacture the material in the first place. I don't think it's a good idea to try to rule out any particular insulating materials based on their feedstock for this reason, especially since they don't necassarily even have to be made from oil to begin with.
Regarding your original question, there have been some studies as to GWP of various foams. Comparisons of EPS to XPS, things like that. I can't link to any, but if you dig around you can probably find some. I don't remember seeing comparisons outside of that though, such as comparing XPS to a mineral wool batt, for example. I'm also not aware of any "overall system" studies, which would include all of the materials used to build the house, although that would be interesting to see. I think right now, you'd have to just look at GWP for various insulating materials alone, since the other materials haven't been looked at in that way as far as I know.
Where you end up is that you have to make some tradeoffs as is the case anytime anything get's built. A lot of engineering is about tradeoffs. Think about a car: a heavier frame means a better crash test rating, and less chance of the occupants being injured in a crash. A heavier frame also means more weight for the engine to move around, which means lower fuel economy. You are trading safety for the people in the car for fuel economy, basically, so burning more fuel to make a safer car. Most houses tend to either emphasize energy efficiency (like Passivhaus), and that's what I am usually after too. Some people try to emphasize building materials, so they use dense pack cellulose, natural wool batts, etc. What you don't so often see is someone trying to do both, because of the tradeoffs that tend to be involved. Rigid foam, as an example, does wonders for improving energy efficiency with a relatively low impact on the rest of the construction process, for example. Thick double stud walls have much more impact on the design than a wrap of rigid foam in most cases.
Bill
Thanks, Bill. There's a lot of good points in you reply. I hope that other people who are new to this issue will read some of these replies because there's a lot of good thoughts. That said, yes, I'm quite familiar with it all myself. I've been doing this for a few decades. I was just hoping to get leads on some more recent information. But it looks like there hasn't been much study along the lines I'm searching.
I'm very familiar with the GWP research that's been done on various insulation materials seen in isolation. The table in this article gives a good example of that.
https://www.buildinggreen.com/news-article/avoiding-global-warming-impact-insulation
I just want to take it to the next step. Here's a hypothetical example. Suppose I'm designing a house and I'm considering several different wall systems. Two of these are:
1. R20 XPS continuous insulation on the exterior of a 2x4 framed wall.
2. Double frame my wall and fill it with cellulose insulation.
For the purposes of an "apples to apples" comparison we'll suppose the details have been tweaked so that both walls have identical U-values.
Which wall has more GWP impact, not just up front, in its construction, but over the course of its life? How much difference is there?
I've picked the 2 extreme cases, XPS and cellulose. The difference in their upfront GWP impacts is very, very large. However, how meaningful is that when considered over the life of the structure? This seems to me like a worthwhile question that should be researched.
A time frame is required. For that I've suggested 100 years because that seems to me an entirely reasonable and responsible age to consider for a single family home. I'm not interested in quibbling over whether we should use 25 or 250 years. A substantial portion of the USA's existing single family housing stock is between 70-130 years old. So 100 is a reasonable number for the purposes of this kind of study.
The discussion of whether or not we should be treating our houses as disposable commodities to be thrown away after 50 years is an interesting but complicated one and not what I'm trying to answer right now.
To add to Michael's comment, Builders for Climate Action also have a BEAM calculator which fairly easily allows you to tally up all the components of homes to give you the big picture of what's going on. This would then need to compared to the operational carbon of the building to figure out an environmental payback period. The same group also a nice report which I'll link below too.
https://www.buildersforclimateaction.org/beam-estimator.html
https://www.buildersforclimateaction.org/report---embarc-report.html
For what it's worth, this is a great question and good job not backing down with some of these replies which seem (to me at least) to be giving excuses to justify building super efficient yet disastrously carbon-intensive buildings.
Thanks, Steve, on all counts. The links will certainly be useful.
"excuses to justify building super efficient yet disastrously carbon-intensive buildings"
If that's what you gathered from my comment, or several of the others, then I think you severely misunderstood. But perhaps you are referring to one or two very specific comments?
Along those lines, one of the things that auto manufacturers have gotten really good at over the past 30 years or so is making sure that everything that goes into a car has the same life expectancy and lasts the same amount of time. If you're old enough to remember cars built before about 1985, they didn't last nearly as long as cars built today, and they often were taken off the road not because major mechanical systems failed, but because minor things would fail and couldn't be repaired. A car from the 70's would start falling apart at about five years -- the accessories would start breaking, the glass would fog, the mirrors would fall off, the seats would sag, and most of all, the body would rust. Meanwhile the engine and transmission would still be strong.
Manufacturers today put a great deal of effort into every part of the car having the same life expectancy. I believe that this approach is ultimately the greenest. I know we're conditioned to think of houses as lasting forever, but the reality is they don't.
I'm an American but spend roughly half my time in France. My home is 120 years old, made of stone, with a slate roof and still has its original windows. The stone is local. The 12o year old window frames were made from local chestnut and are in beautiful condition. My home is one of the younger homes in the area. Homes lasting for centuries is the norm here.
I think you have to be careful to weed out survivor bias, it's entirely possible that 120 years ago they were building lots of crappy houses too, but only the good ones survived.
That said, I live in a neighborhood of Washington, DC, that is mostly single-family homes or duplexes. Most of the neighborhood was built about 100 years ago, and I'd say that about a third of the houses have been torn down in the past 20 years and rebuilt. The reason they were torn down really had nothing to do with the quality of the original houses. Rather, they were functionally obsolete. Specifically, when the neighborhood was built it was an inexpensive, blue-collar neighborhood and modest houses were built. Today the economically rational thing to do is to build the biggest house on a lot that the zoning will support.
The reason that the houses are torn down is that when faced with converting a small, early 20th century house to a large, 21st century house, it's easier, faster and ultimately more cost-effective to just tear it down and start over. And the economics are favorable, I know several people who make a living buying small houses, tearing them down and building large houses.
There's nothing that could have been done when those houses were built that would have prevented that. Or rather, there's nothing that should have been done, nothing that would have made economic sense then or now.
There's nothing unique about this time or place, cities have worked this way since there were cities.
DC_Contrarian -
You wrote, "The reason they were torn down really had nothing to do with the quality of the original houses. Rather, they were functionally obsolete. Specifically, when the neighborhood was built it was an inexpensive, blue-collar neighborhood and modest houses were built. Today the economically rational thing to do is to build the biggest house on a lot that the zoning will support. "
Do you think that in this case the most "economically rational" thing to do is also the best thing to do with respect to climate change and the health of our natural environment?
jollygreensortguy wrote:
"Do you think that in this case the most "economically rational" thing to do is also the best thing to do with respect to climate change and the health of our natural environment?"
Once again I think you're asking the wrong question. We should be thinking about ways to set public policy so that rational behavior on the individual level is what's also best for sustainability.
Let me turn the question around: What public policies should be changed?
I'll also observe that if what you want is a large, new, 21st century house, tearing down an existing house in a city neighborhood is far, far greener than the alternative, which is driving out to where the houses end and subdividing a farmer's field, which is what has historically been the alternative.
DC -- "Once again I think you're asking the wrong question. We should be thinking about ways to set public policy so that rational behavior on the individual level is what's also best for sustainability."
While I mostly agree, there is an element of societal norms (culture, if you will) at play here, that sort of transcends policy and even economics. Certain cultures can value certain things differently without those values being entrained into policy or even economics (at least not directly or solely; though there will probably be filter effects). Perhaps that sounds a bit pie in the sky with American culture which seems to be built on individuality and personal choice— so in that sense there is a practicality to using policy as the main tool.
Of course as many here like to point out, accurately internalizing externalities would be a good economic policy to create an enviro-economic decision making model. But even then, people with money to 'burn as they please' will be able to make decisions that are not the best environmental decision. So I guess the option then is further regulatory policy, or as I mention above, attempts to shift culture (and by culture I don't mean individual moral decisions, but widespread worldview 'norms.')
I would also disagree that there is 'nothing that could be done' when an original structure is built to make it last longer. And I agree we're not talking structural soundness, but rather a form of built-in adaptability so that reasonable changes can be made into the future. I understand the challenge in that we cannot totally predict what changes people in the future will want to make (especially not way into the future), but it doesn't mean there could not be some element of better adaptability built in for a slightly longer lifespan. We don't design many things this way, but I think it is possible to see improvements. Not always and not in every facet of course.
Here's the problem with societal norms: this stuff is complicated. We've got a bunch of experts here and we can't always agree. I don't want to exaggerate the infallibility of experts, but you need to have people who know their stuff advising these kinds of decisions.
JGSG, to answer your question, yes--more or less, anyway. Chris Magwood and his compatriots at Builders for Climate Action have done extensive studies looking at embodied carbon vs operating carbon emissions for single family and multi-family projects, in several Canadian cities. I have seen several presentations about it, and Chris summarizes it one on of these shows: https://www.youtube.com/@thebsandbeershow4723/search?query=magwood. Unfortunately I can't recall which one at the moment. But the gist is that a code-minimum multi-family has less environmental impact than a superinsulated single-family home using similar materials, and a code-minimum home using low-carbon materials has less environmental impact than a super-insulated home using high-carbon materials. They have other findings but those are the main points.
Thanks! This looks like a really useful resource.
You're welcome! This presentation is a few years old but if I recall correctly, it was the first public presentation of Chris' research: https://nesea.org/buildingenergy-boston-2019-keynote-session.
Jolly Green,
Here's a link to another article with more information: "Another Look at Embodied Carbon."
Thanks, Martin. I've ended up with a lot of good resources here today. I feel like I should compile it all somehow, so it's easier for people to get at it all in one place. I've got a little blog. Maybe I'll do that.
The Passive House standard is a performance based energy model and building system. It does not specify what you use only the performance targets you need to achieve. So how "green" it is depends on your definition of "green" and then what materials you choose. The PHPP energy model use by Passive House now has a built in embodied cardon accounting function, so you can compare alternative wall assemblies easily. There are lots of training options available both online and in person to teach you how to use PHPP.
Here are some reports that have examined a number of different options and construction methods from an embodied carbon perspective.
https://www.buildersforclimateaction.org/our-work.html