How does the GWP of materials like XPS compare to other activities?

In considering different material choices, global warming potential (GWP) is one of my considerations, among many others. I realize that materials like XPS and closed cell spray foam have many times the GWP of materials like EPS. However, I would like to get a feel for the overall magnitude of the GWP of building material choices relative to other activities in my life, like driving a car. A big percentage change in a small contributor would be no big deal. A big percentage change in a big contributor gets more weight. Does someone on this site have data comparing the GWP of manufacturing a sheet of XPS to the GWP of burning a gallon of gasoline.
GBA Detail Library
A collection of one thousand construction details organized by climate and house part
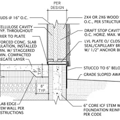
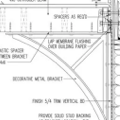
Replies
Reid,
According to this table, XPS has 0.08 kg. of evil blowing agent per kg. of foam, and each kg. of evil blowing agent has a global warming potential (GWP) that is 1,430 times that of C02. So 0.08 kg. of evil blowing agent has the same GWP as 114 kg. of CO2.
According to this document, the CO2 emissions from a gallon of gasoline = 8,887 grams CO2 / gallon.
According to this article, the average American household purchases 908 gallons of gasoline per year for automobile transportation. That much gasoline emits 8,069 kg. of CO2 per year.
How much XPS would you need to use to equal the GWP of that much CO2? The answer is 70.7 kg. of XPS.
1-inch thick XPS weighs 0.125 lbs. (0.0567 kg.) per square foot. So 70.7 kg. of XPS is 1,247 square feet of 1" XPS.
So, to create the same GWP as one year of driving a car, you'd have to install about 78 sheets of 2 ft. by 8 ft. XPS, 1 inch thick.
This calculation assumes that all of the blowing agent in the XPS is eventually released into the atmosphere -- an assumption that may be false.
Martin beat me to it, but I'll post my results anyway since I already did the calculation, and I put it in a slightly different format. Our results are consistent.
I considered 1000 sq. feet of 2" thick XPS and asked how much driving that would correspond to. I assumed 80% of the blowing agent was released eventually. And the result is that the climate impact is equivalent to burning 1500 gallons of gas, or 45,000 miles at 30 mpg. That might be 3-4 years of driving for an individual driver.
Most of my assumptions and numbers came from LDD Harvey's paper:
http://faculty.geog.utoronto.ca/Harvey/Harvey/papers/Harvey (2007c, BAE, Climatic Impact of Insulation).pdf
Thank you for the prompt responses. This helps me put the GWP in perspective.
Charlie,
Thanks for your calculation. It's good to know that our answers -- derived separately, using slightly different methods -- are in the same ballpark.
Don't forget to factor-in the climate impact of manufacturing the polymer itself, which is also pretty substantial compared to say, rock wool, or cellulose (which has quite a range, if using virgin stock paper rather than post-use reclaimed/recycled feedstocks.)
But the comparison to other activities is less relevant than whether it it's a net-benefit or a net negative to global warming on a lifecycle basis for the house due to the reduced energy use.
Doing the math on how long it takes to break even on climate impact is a bit more complicated, since both the heating/cooling energy sources and the total-R of the assembly both come into play. No matter what those numbers are, it's about 5x longer for XPS than it is for rigid rock wool, which can often be used in the same locations within the assembly. If using very low-carb energy sources like hydro / wind / solar the break-even on any of it is "never", whereas if heating with with high-carb fuel like heating oil it has a chance. But the break-even point on 2" of exterior 1.5lb density XPS on a 2x6/R20 wall in a house heated with heating oil is quite long (varies with climate) and may be never, depending on the anticipated lifecycle of the house, whereas with rigid rock wool or EPS it's (nearly) always a net-win.
If heating with mixed-fuel source electricity it gets even more complicated, since the grid sources are constantly evolving, and rapidly going low-carb in many locations. Over even a 50 year lifecycle of a house built in 2015 most grids in N.America will have become nearly 100% zero-carbon by 2065, even in places like West Virginia with a ~95% coal-fired grid (much of it low thermal efficiency sub-critical coal at that!) The financial learning curves of both wind and solar are still pretty strong, and will undercut the cost of any fossil fired generation sources by 2030. (Wind already has, in the midwestern US, where the capacity factors of wind power are pretty high.)
Dana,
The house will be heated with a 95% efficient natural gas furnace.
If I were choosing based on what I know now, I would choose EPS. I had not considered rock wool. I should learn more about that.
The reason for asking the question is so I know whether to be insistent on low GWP products or let my builder select whatever he is most comfortable with. He would prefer not to do any exterior foam. I certainly don't want to push him to include it if the life cycle impact is negative.
In most climates 2" of XPS on the exterior of 2x6 / R20 house heated with natural gas would eventually pay off on a GWP basis- you'd have to do the math for your climate and actual building assemblies to figure out just how long that is.
Under a basement slab in most climates the GWP break-even point of 2" of XPS is probably getting on never ( but there's pay-off in resilience- the basement doesn't get moldy. ) There could be reasonable return times on 1" though. With EPS even ~3-4" could still have reasonable break-even times, in colder climates with a fossil-burner heating the place.
I strongly question if there's ever a GWP payoff for sub-slab even for EPS at the very thick PassivHaus type levels. Maybe there is if the place heated (at the very low PassivHaus energy use levels) with resistance electricity sourced from a high-carb grid for 50-100 years, but it's highly unlikely that high carb grids will still be around in 50 years. For all of the good aspects the standard brings to the table, the high-R sub-slab insulation is one of the least credible factors, since it usually requires a material with a real global warming footprint.
The lifecycle GWP of insulating materials actually matter when installed high-R, but that hasn't stopped people from building a certified US PassiveHouse and getting accolades even when using things like 6" polyurethane SIPs containing at least 5" of 2lb-3lb density closed cell polyurethane blown with HFC 245fa.
eg: http://www.raycore.com/blog/sip-home-green-building-award/
OK. Congratulations, I guess. (sigh) Live and learn.
Eventually the worst blowing agents will go away, at which point we can relax a bit about 2lb foam, but at that density & higher R the quantity of polymer really counts too. Closed cell polyurethane and XPS have many wonderful properties, and many applications where it's for moisture control, but doing all the insulation in a high-R assembly with with 2lb foam is never going to make sense.