How do I upgrade a low-slope cathedral roof?

The roof is on a Panabode that I just purchased Zone 4. Haven’t taken possession yet so don’t have detail pictures. From my investigations the roof is made up of 4X10 longitudinal cedar beams 4 feet apart. The ceiling is 2.5 inch tonque and groove cedar running from ridge to plate. On top of this is 1.5 inches of rigid insulation then half inch plywood sheathing and then torch on roofing. It is about a 1/4 pitch. Can I use the torch on as a vapour barrier and then frame it up with 2X8 and use fibre glass bats, vented? On top of that would be sheathing, self adhesive membrane and then steel roofing on strapping. I need to do the walls too of course but they are simpler not having the torch on roofing or rigid foam. The walls would have to be framed on the outside to support the new roof framing.
GBA Detail Library
A collection of one thousand construction details organized by climate and house part
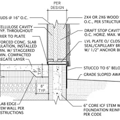
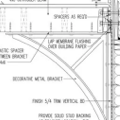
Replies
Ted,
The existing 1.5 inches of rigid foam has an R-value of R-6 to R-7.5. That's not much. The 2012 IRC calls for roofs in Climate Zone 4 to have a minimum R-value of R-49.
A low-slope roof like yours should be insulated like a commercial roof. The standard way to insulate this type of roof is to install rigid foam above the roof sheathing, some type of cover board, and new membrane roofing. You won't have to remove the existing roofing to proceed this way.
You probably want to install about 9 or 10 inches of EPS or polyiso to properly insulate this roof. For more information, see these two articles:
Insulating Low-Slope Residential Roofs
How to Install Rigid Foam On Top of Roof Sheathing
Thanks for your input! I am also concerned about structural integrity which is why I thought I should frame up with 2X8. The span is about 12 ft. and the longitudinal beams span just under 14 ft. I guess I could put rigid foam in between the rafters which would deliver about R35 plus the 6 existing and another 3 for the cedar would be R44 and I guess another layer over the rafters under the sheathing would bring it to R 50. The rafters would be isolated by the one layer of rigid foam on top and bottom. This would amount to 7 layers of 1.5" or 4 layers of 2 : and 2 layers of 1.5". I have looked at a number of articles and will visit the article you mentioned. I may have to get a structural engineer involved if I don't want to use the rafters as it is not a standard construction. Thanks again.!
I'm having a hard time converting the words to images as your intended stack up.
Are you talking about building a 2x8 framed roof with a vented roof deck above the existing roof?
The precise climate matters is this zone 4C? (I'm inferring from spelling conventions that you're either in British Columbia parts of which are essentially zone 4C, or are from one of the commonwealth nations, which means you could be living in US zone 4A or 4B too.)
I am in Zone 4A on an a Gulf Island or will be when we move at the end of the month. I am or was talking about a 2 X 8 framed roof with a vented roof deck above the existing roof. I can relate to your confusion and will make up a drawing. I am, after the first comment considering doing away with the venting except as part to the rain shield under the roofing. Please excuse me if I don't use the correct terms. Although I am a journeyman I have not worked full time as a carpenter for nearly 30 years and have not kept up with the latest developments over that period. I am still coming to terms with the idea of a rain screen. R20 was what we put in the roof and R12 in the walls when I last worked in carpentry. All this new science and the unconventional construction of this place is a bit daunting. I continue to be concerned about the added weight on the roof if I don't frame with 2X8 Rafters.
I have had a chance to digest everything and have a tentative plan. I don't think bringing the roof up to code is going to work for me financially because of the structural setup. I am thinking a retro that would bring it up to R30 will have to do. I don't like the idea of fastening through 8 to 10 inches of foam ( I guess I am more old school than I thought). I think 3 layers as in the drawings would be it for me. I would fasten the first layer of 2X4's(with foam between) through the half inch sheathing and first layer of foam into the 2 1/2" cedar ceiling. I would then apply a continuous layer of rigid (2") over all, fastening a 3rd layer of foam and 2X4's on top of this, into the previous layer of 2X4's. Then would come continuous membrane strapping and roofing. I think I can do this on my budget. I still have a lot of other upgrades to consider like the walls, windows, doors and hopefully some solar as I have a southern exposure to take advantage of. I am posting two hand drawn pictures, one is of the existing roof and in the other I have tried to illustrate my plan. Comments are very welcome. Thanks in advance.
Ted,
A continuous layer of rigid foam performs significantly better than rigid foam strips that are inserted between parallel 2x4s.
I know that you are worried about fastening, but I think you are overreacting. Here's a suggestion: Why not eliminate at least one of the layers of new 2x4s? Two continuous layers of rigid foam (plus one interrupted layer) will perform much better than one continuous layer of rigid foam (plus two interrupted layers).
"I am in Zone 4A on an a Gulf Island..."
OK, now I'm completely lost. The Gulf Islands I'm familiar with are in Mississippi, (on the Gulf of Mexico) which is zone 2A, not 4A.m
Coastal zone 4A in the US extends from Long Island, NY to the Virginia/North Carolina border:
https://www.greenbuildingadvisor.com/sites/default/files/images/DOE%20climate%20zone%20map.preview.jpg
In a zone 2A climate you can hit the U0.030 code-max with 4" of rigid polyisocyanurate clamped in place with 2x furring through-screwed to the roof decking 24" o.c. with pancake head timber screws, mounting the nailer deck to the furring.
The 2.5" cedar is good for nearly R4, the 1.5" of existing foam is good for another R6, the existing half-inch OSB is another R0.5-ish so you're up to R10+. With 4" of continuous 2lb roofing polyiso that adds another R22 and you're at 32+. With the additional air films of the cavity, the new nailer deck & roofing you'll be in the R 35-ish whole-assembly range, or U0.029.
In zone 4A you'd be under the U0.026 code max with 5" of contiuous polyiso.
Dana I am in Canada in the Vancouver Gulf Islands B.C., Sorry about that! I should have included the whole address. I tend to estimate on the conservative side using R6 for the existing foam and as you point out R4 for the 2.5" of cedar and ignoring the sheathing. I don't like OSB and always use plywood. Anyway just one of my fetishes. By the way thanks also to Martin. I will consider what you have suggested. I might wait until I actually get to the point of doing it and see what I think as I go. This is great I really appreciate the input. I may bow to getting a roofing company to do this for me as my wife doesn't want me on the roof. It's kind of nice she wants to keep me around! I want to know what I am talking about so they will do it my way.
OK, Vancouver Island would be Zone 4C, not 4A.
Plywood is fine- has better moisture handling characteristics than OSB in some applications (not necessarily this one) and about the same thermal performance.
The IRC calls out U0.026 max for zone 4C too, so 5" of continuous polyiso with 2x furring for venting the new nailer would still do it.