How do I install rigid foam board around windows ?

I am near the point of installing vinyl siding on my new construction house. The location is southwestern Arkansas.
The walls are 2×6 with taped Zip panels for the sheathing.
The insulation between the studs will most likely be Roxul.
For my climate zone, according to the advisors at Buildingscience.com , I should not use a poly vapor barrier beneath the drywall, but instead just let the painted drywall act as a vapor retarder so that the wall can dry to the interior.
I was concerned that I might need to have some foam board on the exterior of the sheathing to keep the sheathing warm enough to prevent condensation on the interior of the sheathing in the colder months.
However, again according to the advisors at Buildingscience.com, it would not be necessary in my climate zone since they say the interior of the sheathing would not reach the dew point.
Now that I am at the point of siding the house, I am toying with the idea of installing about 1″ of foam board anyway to add to the thermal envelope of the house.
If I do so, the concern is how do I transition at the windows.
The windows are already installed with the nailing fins directly over the Zip sheathing. The window sills are flashed, using a 1/4″ dam along the interior edge of the sill, and the side and top nailing fins are flashed to the sheathing.
The windows are vinyl with a built-in ‘j’ channel.
If I add the 1″ foam board, the vinyl siding will no longer, of course, fit into the built-in ‘j’ channel.
What are my options for weatherproofing this juncture of the siding to the windows when the 1″ foam board projects the siding outward 1″ from the sheathing ?
GBA Detail Library
A collection of one thousand construction details organized by climate and house part
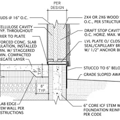
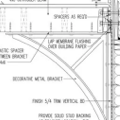
Replies
Jim,
If you add exterior foam, you will end up needing exterior jamb extensions and an exterior sill extension. On a new construction job, it would have been much better to plan your window installation and flashing details to accommodate the thickness of the foam, instead of scratching your head after the windows are already installed.
I have heard some experts -- mostly the type of consultants who specialize in water-intrusion issues -- who say flat-out that you cannot do a good job of flashing and water management in a situation like yours, and that the only good way to do it is to remove the windows and flash them properly from the start, with details that account for the foam thickness.
However, I'm not one of them. I think you can probably do it -- as long as you aren't in a location with extreme exposure (like an ocean-front lot) and as long as your roof has decent overhangs. In fact, I just did something similar on my own house, retrofitting flashing details on an existing window that got "buried" by 2 inches of polyiso. (However, that window was tucked up tight to a generous roof overhang, so I'm not too worried.)
You'll need to retrofit a sill under the existing sill; use flashing-coated wood or a durable species like cedar. Slope the sill extension and be sure it extends beyond the siding. Put a kerf on the underside to help the water drip off the end of the sill. Use silicone caulk and stainless steel nails to secure it. The sill should be long enough to accommodate your jamb extensions.
Think like a roofer and follow the raindrops. Do a good job detailing the flashing. And next time you build a house, make the decision about exterior foam earlier in the process.