How do I explain the inefficiency of 2″ polyiso walls in Northern Vermont politely?

Hi, I have some clients who have had experience with building Timberpeg homes in the past. They continue to insist that the homes they built were energy efficient despite being insulated with 2″ polyiso in the walls and 3″ on the roof. This is wildly inefficient in my experience. I build timber frame homes with SIP walls that are 6-10″ thick. I have presented them with charts showing r-values and also sent them links to your articles about rigid foam.
They built a house in Victory, Vermont using that 2″ wall and 3″ roof and say it was very efficient. They claim that during a period of -20 degree weather the power went out for three days and with no heat source the inside temp stayed at 68 degrees. I know this could not have happened. How can I explain the impossibility of a heat loss scenario like that in a clear, polite way without insulting their intelligence or worse, possibly loosing my chance to build them a beautiful timber frame. I am only doing the frame and they will be doing the rest of the house, but I feel the need to express my concern about their design.
Note: After much back and forth they are asking if 3″ walls and 4″ roof is better. While I agree it is “better”, I still do not think it is “enough”. It is a single story 1500 sq.ft. house and has the same footprint walkout basement. It is being built in East Charleston, Vt.
GBA Detail Library
A collection of one thousand construction details organized by climate and house part
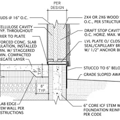
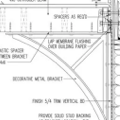
Replies
Luke,
It's certainly possible for a house to stay at 68 degrees if the sun shines during the day. Solar heat gain is real.
Airtightness makes a huge difference when it comes to energy performance. A fairly airtight house with an R-13 envelope will outperform a leaky house with an R-30 envelope. So there are many variables.
Don't try to undermine people's reports of performance unless you are sure they are lying.
Of course your basic premise is correct: if all other factors are equal (including airtightness), doubling the R-value of an assembly cuts the heat flow through the assembly in half.
You might also mention that 2 inch polyiso in walls and 3 inch polyiso in roofs doesn't meet minimum code requirements. Of course, most Vermonters don't care about building codes...
IRC 2012 code-max U-factors for roofs and walls in climate zone 6 (all of VT), is U0.026 and U0.048 respectively. That's a "whole wall R" of 38.5 for the roof, or R21 for the walls.
If you credit R2 for the combined interior & exterior air films + sheathing & wallboard means you would need a minimum of 6" of continuous polyiso over the roof, and 3" for the walls to meet the letter of code. So in your proposed stackup, the walls might hit code-minimum, but not the roof.
And that's using the labeled R-value, not the true performance of polyiso at the mean temperatures you'll see in a VT winter, which is a double-digit percentage lower than labeled.
Martin,
Thanks for keeping me in line. I don't want to accuse these folks of lying. I don't think they are. I have a lot of respect for them and their building experience. Perhaps it was a very sunny stretch of weather and they had good exposure. I don't have all the variables so I won't dwell on that example.
What I would like to do is give them some good advice.
Can you make a polyiso thickness recommendation? The timber frame is to be wrapped with 3/4" t+g pine and they are using an aluminum vapor/ air barrier paper of some sort that also protects the interior from off gassing of exterior materials. They plan to use rigid foam and then attach strapping through that to the frame and then clapboards.
I want them to have an energy efficient house and my instinct says 4" minimum walls and 6" minimum roof if using sheets of polyiso.
Is there a system that would be considered energy efficient using only 2" polyiso in the wall and 3" in the roof?
Yes, two layers of each works to make it "energy efficient" at least in terms of at least meeting/beating code minimums, as explained in response #2 above, and in your separate thread.
It would hit the letter of code min on the walls with as little as 3" of continuous polyiso, but the roof needs at least 6" of continuous polyiso to get there.
A 2015 code min house isn't the energy hog a 1980's code min house was. The 2" walls/3" roof might have been comparable to code-min in 1990, but if you're not at least at IRC 2012 levels of performance it's not exactly "energy efficient" in relative terms, and it's techically not a legal house to build. See Table 5-1 on page 33 (page 38 in PDF pagination) of the 2015 VT energy handbook, which varies slightly from IRC prescriptives:
http://publicservice.vermont.gov/sites/dps/files/documents/Energy_Efficiency/RBES/2015_VT_Energy_Code_Handbook_V4.1.pdf
In particular, note the Package 3 column, specifying R-values if done in continuous layers, such as a foam-over. It looks like you'd need at least 3.5" of wall polyiso, but could skate by with as little 4.5" of roof polyiso, if continuous. That's the MINIMUM LEGAL amount that needs to be there. To consider a house to be particularly "efficient" it would need higher performance than that, but it's not a terrible performance point.
Luke,
Q. "Can you make a polyiso thickness recommendation? ... I want them to have an energy efficient house and my instinct says 4" minimum walls and 6" minimum roof if using sheets of polyiso."
A. Your instinct is correct. Dana has also given you good advice.
You might also tell these clients that if they manage to barely meet the minimum R-value requirements of the building code, what they will have is a code-minimum house. Here at GBA, a lot of readers distinguish between your goal -- an "energy-efficient house" -- and a code-minimum house. Most of us believe that if you want to brag about energy efficiency, you should try to do a little better than minimum code requirements.
Thank you Dana and Martin. I love this website. Such a wealth of information. Great job.
So my clients have asked me to do construction drawing for their house. I will be erecting a timber frame for them and they will be taking over after that. They has refused to add additional insulation to their design. They are at 3" polyiso on the walls and 4" in the roof. I have explained the r-value and the not meeting minimum code and they have not budged. Well actually they have budged slightly, from 2" walls and 3" roof to 3" and 4".
My question, Is there any risk to me personally me if I do drawings for their house construction using their requested specifications that do not meet code? Other than my reputation as an energy efficient builder being at risk. I would really like to Raise a nice timber frame for these folks and let them do want they want. What do you think?
Luke,
Vermont now has a residential energy code. It isn't well enforced, but it's the law. If you build a house that doesn't meet code requirements, you are probably breaking the law. Moreover, if your clients change their mind at the end of the job, they might be able to sue you.
Ok. If I just raise a timber frame for them and then walk away, and I refuse to do any construction drawings, beyond the frame drawings, for them, would I still be at risk? or would all the responsibility be theirs?They are if fact their own general contractor and I am just a framing subcontractor.
Luke,
It sounds like you'll probably be OK with your approach -- but I'm not a lawyer. When in doubt, consult your attorney.
It's possible to meet IRC 2015 code minimums based on a "total building performance" basis rather than R-value/U-factor prescriptives. That's going to be difficult (but not impossible) at the raw R-values you're looking at.
If raw insulation cost is the issue, consider using reclaimed roofing foam (at 25-35% the material cost of virgin stock). Nationwide Foam in Framingham MA will drop-ship to pretty much any location in he lower 48. Green Insulation Group in Worcester MA would probably ship to VT as well. These vendors typically have truckloads of 2" and 3" pretty good used-once fiber-faced polyiso at $10-20 for a sheet of 4 x 8.
For a design like this using 4" reclaimed goods for the walls and 6" for the roof would even be cheaper than the proposed sub-code 2" & 3" non-solution using brand new goods. Those vendors also often have brand new factory-blemish reject goods priced at roughly half cost of distributor-perfect foam.
Luke
RUN don't walk from these clients. They don't trust you. They don't value your judgement. The project will likely become mired down with more disputes. Things won't end well. Consider it a blessing that you learned this early in the process.
It doesn't matter if there is an energy code, or if its possible to comply with the level of insulation they want. Its not a good idea, its not efficient, and its not up to your standards.
Putting up the frame and "walking" isn't going to help your reputation. Get out now before the harm is done.