How can I solve an uninsulated basement slab energy loss?

I built a supper insulated house on a foundation that was not. I currently live in climate zone 5A in central Illinois, the house itself has R30 basement walls, R40 first floor walls and R60 attic. Double stud framing, air barrier is at the house sheathing. The house itself is 4400 sq ft total of enclosed space, 2100 first floor and 2300 basement. At the moment my home is heated and cooled with a single point source ductless mini split on the main level with a Zhender ERV for mechanical ventilation. It performed pretty well this past winter and does well this summer. However it could be better. I know my weak point is my basement. I poured the basement prior to gaining knowledge in thermal bridging and the importance of isolating the slab from the exterior. Basically, I poured the basement and it sat for a period of time at which I then changed my thoughts about building a good home.
At the moment I am trying to understand and figure out a way to solve this giant energy loss in my home. Here’s a little bit about the basement, it’s a walk out carved into a hillsode. All drainage is gravity, absolutely no water migration through slab to speak off. A plastic tape test has been installed on the floor for months wih no signs of water vapor transmission through the slab. The slab perimeter has 1′” extruded polystyrene underneath 4 ft in from the foundstion edge at walkout portion only. I do have radiant tubing in the slab and was not going to use it, but I ended up starting the install of the boiler this year and now I’m considering the giant loss iof btu when I fire up this heat source. I’m not sure if I even want to at this point.
I’m considering overlaying my entire basement in 4″ of extruded polystyrene then putting an osb subfloor over top. Other options would be polystyrene then pour another slab to utilize my combi boiler for a heat source. Head room is not an issue, I have an extremely tall basement. I’m looking for guidence and a planned approach to retrofitting my basement to match the rest of the house. I know radiant heat is not worth it in most super insulated homes, however I do like this as an option because if the low cost as a fuel source. I’m also considering that instead of pumping any money into the basement retrofit to instead spend those dollars on a PV system instead and installing another minisplit in the basement.
I’m looking for some help with this one.
GBA Detail Library
A collection of one thousand construction details organized by climate and house part
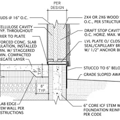
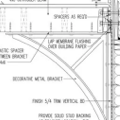
Replies
Joseph,
To balance the specs achieved for the rest of the house, you need a continuous horizontal layer of rigid foam on top of your basement slab -- at least 2 inches thick, or 4 inches if you plan to install new PEX tubing above the insulation. You can install a plywood subfloor or a new slab on top of the rigid foam.
You also need vertical insulation to protect the foundation wall at the walkout side of your basement. If I were you, I would make this vertical insulation at least 3 inches thick -- more is always better -- and I would extend it from the top of the slab down at least 2 feet (4 feet is better) below grade. Of course, the above-grade portion of this rigid foam needs to be protected with metal flashing, stucco, or pressure-treated plywood, and you need to install Z-flashing at the top of the rigid foam (with the Z-flashing integrated with the siding).
Martin,
Can you provide a general reference or recommendation for basement under slab insulation particularly for a walk out basement. I plan to build in climate zone 4.
Tom Cross
Joseph: 4"/ R20 XPS is going to cost about $2.50-2.80 per square foot just for the foam, not to mention the new slab etc. It'll probably add up to more than the cost of a 3/4 ton mini-split, but less than the mini-split + enough PV to cover the mini-split's operating cost. Unless the energy cost for the radiant floor is FREE, it's likely that the PV + mini-split would be a better investment.
Tom: If you download BA-1005 and look at table 2 p.10 it's a good starting point for figuring out what's financially rational on a lifecycle basis. In cheap energy/high construction cost areas those numbers are on the high side. Conversely with cheap construction costs and high energy costs they're a bit low.
http://buildingscience.com/documents/bareports/ba-1005-building-america-high-r-value-high-performance-residential-buildings-all-climate-zones/view
So for climate zone 4 they're suggesting R7.5 continuous under the slab. If it's a radiant slab, add R5 to that.
Rather than 1.5" of XPS (R7.5), use 2" of EPS (R8.4), since the latter is both cheaper, and doesn't lose R over time. In 50 years after the XPS has lost most of it's blowing agent 1.5" of XPS will be more like R6.5, whereas 2" of EPS will still be R8.4.
Joseph,
Dana is correct about the comparison with an investment in a PV system.
My recommendations were tailored to your case. You've built a home with R-30 basement walls, R-40 first floor walls, and an R-60 attic, so I assumed that (a) you are something of an energy nerd, and (b) you can afford to make a significant long-term investment in your house.
Everybody's different. For some people, investing in more rigid foam to reduce heat loss through their foundation will seem like an excellent investment, and will help them sleep soundly at night. For others, it will seem like a waste of money.
It's your house and your money, so you get to decide which route to take.
A few additional suggestions and comments:
1) If you want radiant floor heating, you can do it with a wood floor without pouring a slab if you want. There's a special OSB sub-floor with channels for the tubing built in you can get for that. The steady-state performance will be a little less than in a slab, but with a well insulated house it will be able to deliver way more heat than you need anyway. And embedding the tubing in a slab actually makes it slower to respond if, for example, you keep the basement at 60 F during the week but want it at 70 F on Saturday.
2) How much the insulation matters and how much you might choose to install depends a little on how you use the basement and whether you keep it as warm as the upstairs. If you actually leave it at 60 most of the time it's not as critical.
3) EPS is not only cheaper than XPS per unit R-value, but it also has much lower environmental impact, because it doesn't use the high-global-warming impact blowing agent that XPS uses.
4) If you want to get creative about how to use the tubing that is embedded in the existing slab, connect it to low-cost solar collector made for solar pool heating, and pump hot water through it in the summer. That will help prevent condensation and mold on the slab in the summer, and it will pre-heat the ground underneath in preparation for the winter, at which point the lack of insulation won't matter.
5) In a lot of cases, the insulation thickness in this type of retrofit is limited by the headroom issue. Since you've got the room, go ahead and put in as much as you want to spend the money on, and definitely use EPS not XPS, because it's R/$ that matters for you, not R/inch.
Dana,
I believe that is probably the best utilization of resources as well. My concern at the moment is will the single sided approach be a better long term investment here? I am also am very concerned with the comfort of this space. I wanted to make sure that installing a layer of foam over top of this slab will not create any unforeseen problems.
Martin,
You are correct I am a bit of an energy nerd, although I consider myself a grade schooler at this point. I am looking at the long term investment in this home. I started this house with the assumption of installing a wood burning boiler which is free in a way for me, and as I gained knowledge and age I realized I would rather buikd a very energy efficient home rather than walk outside and stoke a fire. At the moment I'm using about 500kWh a month and I believe my major energy consumption is coming from this "open window" I have in a basement slab. At the same time I believe insulating the slab will actually make my home more comfortable.
My concerns with installing the rigid foam over top of the slab is I could not find any literature or studies pertaining to this approach. Everything I found was bringing the basement slab itself inside the controlled envelop so I was concerned sbout the possibility of causing another issue while trying to solve one. I wasn't sure if I should possibly finish the floor with a high strength epoxy on the surface, or possibly install a dimple mat prior to covering the floor with foam. I don't have any signs vapor diffusion through the slab but once I cover it up, I will never know what animal I may have created.
It's taken me over 3 years to build this home and the only part of it I didn't think out I now regret so I want to make sure I do it right this time.
.
From a creature comfort and summertime mold-hazard point of view it only takes 1-1.5" of EPS under a plywood or OSB subfloor over the slab at your ~52F - 54F subsoil temps. From a long term financial hedge on energy costs point of view, go with 2". But 1.5" would be more than sufficient for comfort & mold control. If heating with a radiant floor instead of a mini-split go with 3".
Installing a wood subfloor over foam on top of slab is a very common retrofit when finishing off a basement to make it living-space. If the slab was installed over a continuous vapor barrier (required by code in most locations) you may not even need a vapor barrier. If you're not sure, 6-mil polyethylene between the foam and the subflooring works.
I'm not convinced that the slab is as big a "hole" as you think it is. If you have a decent pistol-grip infra-red thermometer (even ~$50-60 box-store versions are fine), wander around the basement and take a bunch of temperature readings. If your slab is well-drained it's unlikely to be much below 60F anywhere, unless the basement isn't being fully heated, and there is insulation between the basement and first floor. Even in winter it's likely going to be 55F or higher. How many square feet of exposed slab is there?
Wood boilers are fairly high-pollution energy sources (the subject of many neighborly lawsuits in New England) and not all that efficient if installed outside of conditioned space. An EPA rated wood stove is both cleaner & more efficient (if less automatic than well a set-up wood boiler.)
The total square footage of exposed slab is 2300 sq ft. There is no heat source or air conditioning in the basement at all. I have no insulation between basement and first floor. I have two supplies and two returns from the ERV ducted into the basement so that is the only conditioning I currently receive in this space. it is completely unfinished at the moment. I did wire and prepare it for a second mini split that I plan to install in the future.
At the time when i started building this home, energy and pollution were not high on my list of concerns when thinking about an outdoor wood boiler. The abundance of trees on the 30 acre property of timber in which I built my home were. (I could heat a house from the limbs that fall every year). It wasn't until I began the study of building science and indoor air quality when I realized the long term impact and long term gain from designing and building a high performance home. That, and its hard to do. The details fascinate me. I'm a builder in my community and in the Midwest sub standard building practices are abundant. When word got around about me building a home wih a single point source hvac design, I was described as insane. (Those mini splits are for hotel rooms and garages). The concept of mechanical ventilation is not a common practice. I still often hear the term "you don't want to build a house to tight" When people drove by and saw my entire house with a rain screen going up, the calls came in. It isn't until you get the light bill in the mail that individuals take notice. That and the clean fresh air you breathe when walking into my home. I want to build great homes, and learning a long the way is part of it. Correcting my mistakes I made prior to gaining knowledge is also part of being a builder.
You should do some energy modelling to determine your actual loses, keep in mind in summer your actually gaining from the lack of insulation.
It would be nice to fix, but i suspect the actual payback will be several decades if ever.
The "payback" is in comfort and lowered mold risk, not dollars. A 55-60F slab isn't exactly comfortable in bare feet, and it becomes a mold hazard in summer when the outdoor dew points are north of 60F (which is most of the time in central IL. It doesn't take much foam over the slab and under a subfloor to fix that.
EPS has a typical installed cost on the order of 10 cents per R-ft^2, but for a big flat over-slab it'll probably be a bit lower than that. So just the insulation cost for 2300' of R8/2" EPS is about $1800. For R6 /1.5" it's under $1400. Whether the "extra" ~$400 for R8 vs. R6 ever pays off on reduced energy use is highly speculative, dependent upon future energy price inflation/deflation. Going to R20 with XPS at a higher cost per R-ft^2 would require truly daunting energy price inflation to ever pay off, even over in100 years. (Is there any chance of price inflation on the deadfall from the woodlot portion of your property? :-) )
The costs of the new subfloor & finish floor, and any adjustments necessary for stairs, etc would be extra. It's simply part of the cost of finishing a basement, not an energy efficiency, sustainability, or resilience measure the way the floor-foam is. At least 1/2" of OSB or similar over the foam would be necessary to meet fire code, so some fraction of those costs can be rightly apportioned to the insulation, but not the whole shebang.
Joseph;
Is it too late to consider digging around the outside of your slab, as Martin suggested, down X feet but also away or out from the exterior wall by Y feet, so that you can place some 2"-3" of rigid insulation vertically on the outside of the slab and 2-3 feet horizontally going away from the slab. That should be all you wound need to protect the slab since the more you go inwards into the home from the slab edge, the less cold will be there anyways.
Plus some cold/cool coming from the slab in the summer could replace some air conditioning load.
Insulating the slab from the outside creates a deflection zone around the slab were the cold now has to go down the vertical plane then away and around the horizontal plane then back towards the slab to reach the slab from underneath. But once it goes down enough, it gets to the 4' thaw zone where the cold will just lose its "potency". I'm in zone 6.
I don't think that you need to do so much work inside if it could be done from outside as a true thermal barrier keeping the cold away from the slab in the first place. This way your present basement floor radiant heating should be fine and no need to add endless layers of more work. With a radiant heated floor, maybe put some nice ceramic on that floor and enjoy the comfort. In any case, your home is already super insulated so the radiant floor does not have to dish out so much heat as to replace any major house losses, and heating the floor only slightly will lessen the overall heat loss down through the slab.
See the fifth diagram here......
http://naturalgasefficiency.org/industrial/insulation_Floor.htm
and this here .......
http://www.healthyheating.com/Radiant_heating_designs/insulating-underslabs.htm#.Vdh4ZZeZgZg
Leon
Joseph, you have a very common problem. Now do you feel better? No? I didn't think so! Ok, enough with the jokes. Here is another spin, different than Martin and Dana. Forget the radiant heat. Put a high efficiency wood stove in the basement. If, as you say, you have practically free firewood then a cord at most will cancel your total basement losses and make that floor toasty, even if uninsulated. It's a nice back up if the power goes out and if the stove has a glass door you might find yourself down there more often than upstairs. No muss, no fuss.
It's not to late for anything, other than insulating under my slab of course. I haven't decided on the direction in which I will proceed. I wanted some good sound advice on the matter. Which I got, and I thank you all for that. As for the small wood burner, I almost went that route, but the make up air situation had me a bit concerned. I do have vertical insulation, 2" thick on both sides of the walkout portion of my foundstion as well as the rest of the house. I used the insulation more as a capillary break on the exterior side, , so extending it up to the siding would not be a major undertaking.