How can I limit the thermal bridging, and eliminate the potential for interior condensation, at a cantilevered steel deck?

I’m an architect working on the remodel of a single-family dwelling in San Francisco (Climate Zone 3C). My client wants to maximize the city view, so steel will be used for a rigid steel frame at the view side of the building, for the structural frame of a cantilevered deck, and for posts and beams at a number of exterior walls. The cantilievered steel deck will be welded to the rigid steel frame (no gap for a thermal break material), and the engineer has called for steel beams to be welded to the rigid steel frame at the ceiling of the interior opposite the deck beams to offset the torsion loads of the deck beams. What do you recommend to address the thermal bridging issues, and the related potential for condensation at the interior, for these conditions? To address these conditions, I anticipate that spray foam insulation will need to be used at the interior steel members that are linked to the cantilevered deck, and perhaps thin rigid insulation on the exterior sheathing where steel members occur, but I’d appreciate any suggestions.
GBA Detail Library
A collection of one thousand construction details organized by climate and house part
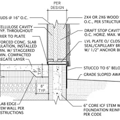
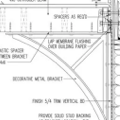
Replies
This is a classic problem. Rigid insulation on the exterior steel is hard to detail durably. Spray foam on the interior steel for the first couple of feet from the thru connection will certainly reduce the risk of condensation. You could also try reducing the total contact area of steel and thereby the thermal bridge by using the balustrade as part of the moment arm of the cantilever, and depending on the depth of the cantilevered deck you may also be able to go to a bolted rather than welded connection through a rigid neoprene separating layer.
Steven,
I'm worried that I'm about to channel Joe Lstiburek here; I apologize in advance... but...
Just because architects and engineers have been doing something for 50 years, doesn't mean it isn't stupid. Cantilevered steel beams that project through the thermal envelope are stupid. This detail was stupid in 1960, and it is still stupid today. It's time for architects to stop doing stupid things.
If you want to have a balcony, you can support the balcony on an independent foundation, or you can get an engineer to design brackets that support the balcony in a way that doesn't compromise the thermal envelope.
I'll end my rant with a photograph I took in Cambridge, Massachusetts. It shows a building owned by Harvard University -- evidence that smart owners can do stupid things. The photo shows a reinforced concrete beam, not a steel beam, but the problem is similar to the problem you describe.
The thermal bridge shown in the photo is cringe-inducing. It imposes a painful view on pedestrians, who have been suffering for decades as a result of one architect's stupidity.
.
Here are a couple of articles from BSC that address some of your issues: http://www.buildingscience.com/documents/insights/bsi-005-a-bridge-too-far/?searchterm=thermal bridging balconies, http://www.buildingscience.com/documents/insights/bsi062-thermal-bridges-redux/?searchterm=thermal bridging balconies
There are engineered solutions to the problem. Don't know how viable they would be for a single family house.
http://www.ecobuild.co.uk/var/uploads/exhibitor/1959/v41xduwlyi.pdf
i was going to mention the isokorb (KST) as well - however in this situation it sounds like that's not a structural possibility due to the size of the deck. martin's right - this is an issue that should be avoided or reconfigured... however the reality of clients/site/etc may not make that possible...
granted...this is a small balcony
however...the designer did some clever "outside the box thinking"
https://sites.google.com/site/trekhauspdx/home/building-progress/building-progress-3-august-2011
Thanks for the example, John. Where there's a will, there's a way.
Thank you all for your feedback. Yes, the cantilevered steel deck is a very undesirable situation in terms of energy and condensation concerns. The 1969 wood deck that will be reinforced with steel doesn't conform to the current Planning Code because it's in the required rear yard open space, so it can't be reconfigured with supporting posts to avoid the cantilever, and the 8' depth prevents the use of a bolted connection and integration of a thermal break material. So, tentatively, it looks like I'll specify spray foam insulation around the steel at the interior, and a thin layer of rigid foam insulation at the exterior face of the building adjacent to the steel members. The project is still in the design phase, so I'll take careful steps with the general contractor, the insulation contractor and the waterproofing consultant to address these concerns.