How can I insulate an exposed flooring system properly?

hi,. i have an addition on my house thats aproximately 11×14 on piers and 5 ft off the ground over sandy soil and exposed on all sides.It has a 2×8 ,16″ on center floor system framed lengthwise over 2 , triple 2×10 beams, one for each set of piers.The subfloor is 3/4 tongue and groove plywood and i will be installing prefinished 3/4 x 2-1/4 tongue and groove strip oak flooring. I insulated the floor a couple years ago and used 2 layers of owens corning unfaced R-13 in the joist bays and then a layer of 3/4inch polyshield by cellofoam with/metalized poly facer facing towards the interior , fastened to the bottom of the joists and then a layer of 1/2 osb over that to keep rodents out.When i pulled the existing carpet up to redo the floor i made a couple access hole to inspect the cavity and found signs of frost and condensation on the foam insulation but only certain areas, closer to where the addition is attached to the house.My questions are how do i avoid this?…The oak flooring manufacturer recommends 15lb. felt under their floor and im concerned i might make the situation worse because of possibly trapping the moisture in and slowing or stopping the drying to either side and causing structural damage and mold.Should i remove the foam and reinstall the osb alone to cover the unfaced fiberglass,then use the 15lb.felt under the oak as a vapor retarder and allow any moisture to dry to the outside ?Or should u add more foam to the existing foam on the bottom to isolate the floor system more from the cold?Or should i pull all the fiberglass down and foam and osb and install/friction fit 2 inches of some type of rigid insulation to the bottom of the subfloor and sill area where the addition attaches to the house and use that as the vapor retarder and then the 2 layers of unfaced fiberglass and cover that with the osb??…Also the existing poly foam on the bottom of the joists runs between the triple 2×10 support beams i previously mentioned and was wondering if that might be contributing to the condensation allowing air to seep into the floor cavity and if the top of the beams should be covered with foam , overlaping onto the existing foamboard,…any advice and info would be greatly appreciated,..thank you
GBA Detail Library
A collection of one thousand construction details organized by climate and house part
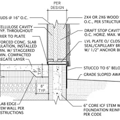
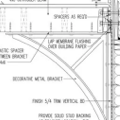
Replies
Where is this located?
im in the central new york area.. i forgot to include that
I'm going to guess the your foam isn't thick enough (it should either be omitted or made much thicker), and/or that there are air leakage issues from the interior. Do you have forced air heat, and is it possibly pressurizing the house slightly? Are the signs of moisture around the perimeter?
Mike,
David's suggestions make sense. This is either an air sealing issue, or perhaps the home is being pressurized. In any case, it's possible that the condensation is a seasonal phenomenon, and that the moisture will dry harmlessly as the weather changes. (The floor system will have some air exchange due to fluctuations in outdoor temperature.)
More information here: How to insulate a cold floor.
i dont have forced air, i have hot water baseboard,..i think i have air leakage on the sill/rim joist from where the addition is attached to the house where the warm air from the basement is/can enter the floor system,... the moisture does seem to be more in that area and i was considering installing rigid foam against it on the addition side.You mentioned adding more foam, i have 3/4 on there now.. would 2 inch be enough and if so what would u recommend?If i ad more foam should i also put the foam over the top of the support beams bridging the 2 foamed areas to have no breaks in the foam layer??i included a picture of the beam...Also if i do go with the extra foam can i still use the 15-30lb felt under the new oak flooring im going to install or will that trap any vapor in the floor system??..the other option u mentioned was to remove the foam which i also thought about but do i just leave the 2 layers of unfaced R13 insulation in the cavity and reinstall the osb underneath then use the 15-30lb vapor barrier under the strip oak flooring and let the floor breath outward,..or should i use the 2 inch rigid foam against the bottom of the subfloor with the unfaced fiberglass under that and then the osb to seal out rodents etc?..and if the 2 inch is used under the subfloor would that eliminate the need for the tarpaper for the oak flooring?,...very frustrated ,..lol
just saw the last response and thank you both David and Martinfor responding...Im not sure what you mean by air sealing issue.Do you mean cold or warm going in the floor?I did seal the perimeter with caulkover the osb where it butts to the perimeter and then nailed 1x1's over that, but i didnt seal the beam area and suspect cold air is leaking in ?maybe i should float over the top of the beams with foam onto the existing foam between joists?
Mike,
When you have wintertime condensation in a cold area of your thermal envelope, the source of the moisture is usually interior air, not exterior air. (Exterior air is dry; interior air is moist.)
It is unlikely but possible that there is a path for warm, moist, interior air to reach the cold rigid foam. However, the stack effect usually prevents this kind of air leakage.
It is even possible that there was no condensation until you opened up the floor. Once you opened up the floor, interior air had access to the cold foam (for the first time).
You are probably overthinking this. I would relax. Go ahead and put rosin paper or asphalt felt under your new oak flooring. (Some people prefer rosin paper to asphalt felt because they are worried about asphalt odors. However, as long as you don't have hydonic tubing in your floor system, I would use either one without worrying.)
Martin,....i do have some tubing in the corner .Do you mean hydronic floor heating system or tubing feeding a baseboard?..I rerouted some 1/2 copper in one corner of the floor and up a wall but its right under the subfloor ,roughly 4 feet total,and i wrapped it in that black styrofoam pipe wrap all the way to the baseboard,... The moisture was found in the floor previously,.i thought about your concept on the warm air reaching the foam once i opened the floor but i dont think thats the case because as soon as i opened it i reached in and felt frost on the foam....The flooring manufacturer recommends felt,...ive always used rosin...if i use the felt should i remove the foam from below and would i still have the option of the 2 inch rigid foam( no foil faced product) under the subfloor with the fiberglass beneath as i previously mentiond or could i possibly risk rotting the 3/4 subfloor by sandwiching it between the foam and felt??...and yes im overthinking it,..lol..can u tell?
Mike,
There is no moisture issue with the asphalt felt - only a (potential) odor issue if it gets too warm.
Don't worry.
I would leave the rigid foam in place and stop worrying. It wouldn't hurt to install more rigid foam from below, as David suggested.
ok, so i think ill use felt,..the floor warranty requires it,..and leave the foam on the bottom and add to it,..would u recommend over the beams and against the sill also ???..the top of the beam felt moist/damp .....and if i decide to take everything out and go with the 2 inch foam up under the subfloor ,friction fit and the fiberglass under that with just the osb closing that in will that be ok if i have the tarpaper under the oak??..will the tar paper be safe to use with both options,.and if you had to choose, which would you advise as the better option???...........again thank your very much for your advice/expertise and time and patience
yes ,no,.. maybe?..lol
Mike, without inspecting in person, it's hard to give detailed advice. As a general rule, you need to locate and seal any air-leakage sites, places where humid air (presumably from the interior) is leaking into your insulated floor and finding a cold, condensing surface. You need to use foam that's thick enough so that the interior surface is not going to get cold enough to condense. You should make the insulation continuous wherever you can, rather than interrupting it with framing. That's the general picture, the specifics are up to the guy putting his hands on the job and figuring out the issues.
The felt under the flooring is a non-issue. Assuming no radiant tubing in the floor, or other source of heat that will bake it, install the felt. I put felt under my wood floors and have done it on many jobs for others over the years.
david,..thanks again,..ill use the felt under the oak,...and eliminate any warm air entering the floor and add more foam underneath or apply the other concept of foam under the subfloor ,unfaced fiberglass below that and the osb,..........again thanks for all your help and advise
Mr. Mike,I'm not sure if anyone has suggested it,but you probably have an ice cold triple 2x10 that isn't helping matters any.It's way more than a thermal bridge,being that two large surface areas of it are within an inch or so of a warm joist cavity. .I can't tell by your photos,if the condensation is in the area of this girder.I'm sure the air leakage around that girder is quite is pretty generous also.
I would have to believe that the triple should be wrapped in foam very well
Dennis,...hi,.. yes the top of the center beam/girder in the pic felt damp and smells musty and i can see some tiny black spots,..maybe mold starting??.. i asked about possibly covering them from the inside and overlaping onto the existing foam with some 2 inch foam.....but I wouldnt be able to do anything to the area where the joists rest on the beam .. unless i wrap the beam as you suggested..which would look like hell unless i cover that with some pine or something but might be the best solution,..............i suspect that that area might still have air leakage/condensation issues even after i do my best to stop them by adding foam at the interior sill area, over the beams and whole bottom surface,.......thats why i brought up possibly putting the foam up under the subfloor ,an unbroken run down the whole joist bay,and then the unfaced batt insulation, then the osb with the hopes of any possible condensation having the ability to dry outward through the osb................
Hey Mr.Mike,I missed when you described that idea earlier in the thread.It sounds like that would work well.I read your question with interest because it is a common occurrence to build a room like you have or to have a porch header beneath living space.I wonder what Martin's suggestion would be to build it from scratch from an energy efficiency perspective.
Mike,here is an interesting write up,that mentions insulating a floor in your situation.
http://www.buildingscience.com/documents/insights/bsi-064-bobby-darin-thermal-performance?searchterm=insulating+floor
Dennis,...Did you mean the concept of the foam under the subloor sounds like it would work well?.....I didnt frame the addition but if i could have i would have probably framed the floor differently, maybe 2x10 or 2x12' joists width wise with the girders under the bearing walls incorporating them in the floor system so that i could also cover the whole bottom surface without having to address the exposed beams...i dont know if thats what martin would do...but thanks for the link ill check it out tonight
Mike,
I agree with you analysis. There are two types of beams. Your beam supports the joists from below, with the bottoms of the joists resting on the top of the beam.
A flush beam, on the other hand, supports the joists with joist hangers. If you had installed a flush beam, it would have been easier to install a continuous layer of rigid foam on the underside of your floor system.
Dennis,
I am so glad you brought up that building science article. I was going to ask about that, but I was afraid it was off topic.
I do not understand the concept of including an airspace above the cavity insulation. Everywhere we hear to not leave an airspace around the insulation and here Dr. Lstibirek says in this situation to leave an airspace on underneath the subfloor and the floor will be warmer?
I don't really understand the mechanism for that. The house we will be building soon will be built on piers and I really intend for it to be energy efficient, so if someone could explain this to me I would appreciate it.
Lucy,
There are three points to remember if you want to use Lstiburek's approach (leaving an air space between the top of the insulation and the subfloor):
1. The reason that his approach works is that the layer of warm air keeps the tops of the joists warmer and therefore reduces thermal bridging somewhat and reduces the "cold stripe" phenomenon.
2. As Lstiburek points out in his article, "the airspace makes for a warmer floor. Filling the airspace completely [with insulation] reduces heat flow and saves energy but does not make the floor warmer." So there is somewhat of a tension here between two different goals -- saving energy and keeping the floor warm.
3. Lstiburek's approach -- leaving an air space between the top of the insulation and the subfloor -- is dangerous to follow if you are a builder with average skills, because air leaks in floor assemblies routinely allow cold exterior air to infiltrate the joist bays. Once that happens, this detail is a disaster. The detail only works if the builder has impeccable air sealing skills. That's rare, but possible.
Here's the bottom line: The insulation that is doing most of the work in this assembly is the continuous layer of rigid foam under the joists. If you want a warmer floor, beef up the thickness of the rigid foam -- and do an impeccable job of air sealing at the perimeter of the floor assembly (the rim joist area). Then it hardly matters how much fluffy stuff you put between the floor joists. You can put in a little (the Lstiburek approach) or a lot (my way).
Finally, that makes sense. Thank you, Martin.
Martin,Joe says "We learned this from Old Guys".One of his points seems to be that this way of insulating floors was traditional in Canada where he was from,and always worked well.I am pretty sure that would pre-date when framers carried caulk guns and foam in a can,and probably foam board also.You can bet that air sealing really helps,but even in the old days it probably wasn't a disaster.