How can I be sure our contractor installed insulation correctly?

Recently our contractor indicated he was complete with the insulation installed with cellulose in the existing walls at our home and wanted a signoff for customer satisfaction. Our home has cedar shingles, tar paper and pine tongue and groove sheathing. He removed the outer shingle and drilled through the tar paper and pine sheathing to install cellulose. THen he installed a styrofoam plug and put shingles back over. However, my husband was concerned that the area that was drilled and then filled with styrofoam may have moisture or leakage. He also thinks some tar paper was ripped in the process. WHen my husband brought this to his attention he sealed the accessible holes with tyvek paper. Our contractor says that moisture will not get behind the shingles and placing protection over the already covered holes is unnecessary. What do you think?
GBA Detail Library
A collection of one thousand construction details organized by climate and house part
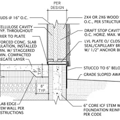
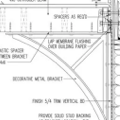
Replies
Have any pix?
Katie
You’re mixing a couple of issues.
With a cellulose install, two tests are used to calculate if it is correct – and should be done during the install for real time quality control - you can still do them:
- Infrared camera to make visual check for cold spots and consistency of application. If you installer does not use one there is a problem and a likelihood of a failed install
- Also, estimates of density and volume based on dimensions of the wall cavities and quantity of material blow into each opening. Done to rough figure material quantities needed and red flag installation gaps.
Your contractor is correct that your shingles stop (most) bulk water entry but you are right that the tar paper is the last line of defense and its integrity needs to be maintained so each drilled hole and tear should be sealed with building tape rated for contact with asphalt.
As for moisture in the form of water vapor and condensation, the matter is more complex and not addressed so much by the integrity of the tar paper as it is by temperature factors as they interact with your entire wall and house design/materials.
Flitch Plate, not sure why you're bringing up IR and bag count, her question is about sealing the holes.
Sounds like what was done is normal. If a shingle is removed to drill the hole, the shingle beneath it is exposed and that's where the hole is drilled. The felt is behind that shingle, so damage to it should be minimal. As long as the plug is tight fitting (any sealant used to install the plug?) and the outer shingle covers the hole nicely, I wouldn't worry about water leakage.
I have seen drill/fill jobs where the plugs are exposed because no siding was removed, with no apparent problems. My house was insulated like that by the previous owner. I gut-remodeled it and found no signs that the plugs leaked.
Thank you for your comments. A sealant was not used. I've attached a photo of the drilled hole for you to see. Appreciate your feedback on this...by the way, photo of wall shown above near my inquiry is not mine. Photo I am attaching is of styrofoam in the drilled hole.
Thanks,
Katie
Photo does not seem to be posting however if I tap on the above photo to enlarge my photo seems to come up.
The felt (tar paper) in your photo does not appear to be torn much, but they broke a piece of the shingle when they drilled the hole. It's unfortunate, but not a huge deal. A super-fastidious craftsman would have slid a piece of thick felt or perhaps thin sheet metal behind that shingle to help protect the wall there, but most would not. I have not seen the styro plugs, they are usually wood around here, and glued in place. Bottom line for me is that you have shingled sidewall, which is great at shedding water, and I doubt you'll have problems. I'll be interested to hear other opinions on the foam plugs.
Lookin’ at the photo and I don’t much like what I see. These are EPS foam plugs, suitable for drywall penetrations of interior wall cellulose installs and then mudding over, but not so good for an exterior install … especially in plank sheathing. I would have insisted on wood plugs.
http://www.insulationsupplies.com/products/wood-plugs
Sure, there might not be a bulk water entry problem, but if you examine the shingles they seem to show water stains and the under-shingle (the one penetrated) seems to be pulling water vertically by capillary action.
This wall is a sponge (shingles and planks); it is only protected by the roofing felt/asphalt impregnated paper. It is hard to tape or otherwise seal these holes when passing through a shingle, but the integrity of the bulk water shield is definitely compromised. I do not agree with the contractor on this job.
Dave, as for mentioning volume and infrared checks on the install. It was implied by the headline question and then it struck me that if the installer is this quick and dirty (as per the post) they probably do not have the controls and quality assurance to get the promised density right. Frankly, this one photo example looks like a “get in and get out fast” job.
Katie, what density of blow (i.e. lb’s of cellulose per sq ft) did you pay the contractor to achieve? And how did they prove to you (and themselves) that they did achieve it? What price per sq ft of wall did they quote you?
I believe I was charged about $3.12 per sf to blow cellulose into the existing walls. It was proposed to be dense packed from R-0 to R-13.6 .This is what it says on proposal however elsewhere on the proposal it also says walls should be R-15 so I imagine I should ask for clarification.
Sincerest thanks for all your thoughts.
Where are you located? R13.6 is right for dense packing 2 X 4 walls. I can't tell from your photo: are the wall's 2 X 4" or 2 X 6"?
For the price you have been charged, you should be offered a "void or cold spot call back warranty", and given proof that you got what you paid for. That would be done with a sign-off sheet that specifies the (1) quanity of material installed, (2) the square footage of the installed surfaces plus the volume in cubic feet, (3) the density of the installed cellulose, and (4) a complete walk though using an infrared camera to show you the quality of the work and prove there are no voids.
Thank you. Would an infrared camera work this time of year in Connecticut? We were told that the infrared would not work as well when there is not that much of a difference in the inside and outdoor temperature.
Also our walls in this part of the house are 2x 4.
Lastly,Dave mentioned wood plugs are mostly used in his area....I wonder where that is?
If you look at my email above, you will find a URL with a line on wooden plugs.
The infrared camera works fine on cool early mornings and cool evenings.
And Dave is in the pacific nw.
Thanks again,, I'm drafting a letter to our contractor and a question occurred to me as I was writing. stryofoam repels water so I was wondering why that was considered inferior in an exterior wall? Is it for structural reasons or protection from anything hitting the outside wall? Also, when we do mention the wood plug should we also recommend a wood glue sealant?
Lastly, 60-70's are pretty cool for us in the evenings and mornings...are u thinking that's fine for infrared now?
I don't know how common it is for dense-pack contractors to verify their jobs via IR after blowing, but there are established standards for inspecting insulation installs via IR, such as RESNET's, and the necessary conditions include 18-degree temperature differential for a period of hours, which can be hard to get right now, and you need a good camera and an experienced operator to do the inspection. If you actually want to do that, it might be better to hire a third party. It is very easy to get false positives in the wrong conditions. My opinion is that you should verify fill via bag count. My insulator leaves a bag count sheet on the job after finishing, and will leave all the bags out if I ask.
If your installer is good, they packed everything no problem, and found whatever obstructions there are in the walls when they tried to insert the hose.
As I said, the wood plugs are what I am used to seeing here, but they are exposed after installation and painted over. The styro plugs seem OK to me since they are covered by a shingle. However, you could call an insulation supply and ask if the styro plugs are OK for use on the exterior side.
There is no need for "glue", the plugs are tapered and will stay put once knocked into place.
Seems to me, Dave, that what makes a good DP Cell installer is the use of an IR camera to set a baseline ahead of the job and then to quality control installation during, while then showing the before-after results to the homeowner at the end.
Flitch, how many insulators do you deal with, and are they inspecting each job with IR? To me, you seem to be saying that people could or should, but you haven't said explicitly that you know a bunch of insulators and they routinely do this.
I deal with three, and they don't check everything with IR. They know their machine and the bag counts required to get dense packed material in walls because they do it all the time. I sometimes check their work and haven't found problems. My impression from reading about this stuff from people all over the country is that most insulators are not scanning every job, and probably a lot aren't scanning any because they don't have the equipment.
If Katie's guy has IR and can get the delta T, then by all means I think he should give her a tour of the completed job. Better than that would be to get someone impartial.
IR imaging wouldn't tell you anything about the density of the dense-pack, but would tell you if there were framing obstructions that created voids.
Most experience dense-packers have well-calibrated fingers and can tell you with startling accuracy the density at the fill-hole where they can poke at it directly. Average density can be estimated by counting the bags and a bit of napkin-math. Some dense-packing contractors will do random spot checking by taking core-samples, measuring the density of standard volume cores directly by weighing the samples.
I've seen cellulose insulation contractors using blower doors during installations to verify that all thermal bypasses were taken care of, but never IR imaging.
Foam insulation contractors often use IR imaging during slow-rise pours in wall cavities to estimate where the initial rise will stop. That enables them to top it off without adding so much material that it a blows out the wall (which is a slow-rise foam installers nightmare scenario.)