How best to insulate a 1935 small Cape; is blown in cellulose OK?

I have a 1935 small Cape in the Boston, MA area. We had bad ice-dams the winter before last. There is virtually no insulation (remnants of some exist in the ceiling of the knee wall areas behind the interior walls in those areas; I tore down some that was deteriorated in the knee wall areas when I bought the house 20 yrs ago).
MassSave has recommended blowing in dense-pack cellulose for the walls and either cellulose/netted cellulose w/ foam board or spray foam in the knee wall areas and ceiling.
I’m having a hard time coming to a decision. After reading some of GBA articles, I’m wondering if expanded cork board could be used instead of foam board. A friend cautioned against blown in cellulose without a vapor barrier, saying it could get wet and harm the house’s frame.
Am I safe in going with blown in cellulose in the walls? I’m sensitive and a little phobic about chemicals and after reading about foam board production, I’m wondering if there are options for the knee wall slopes? Is it better just to do nothing?
Any advice is appreciated. MCC
GBA Detail Library
A collection of one thousand construction details organized by climate and house part
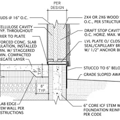
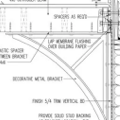
Replies
Miriam,
I'm a firm believer in the conclusion that most attempts to insulate the second floor of a Cape home from the interior result in failure. The only good solution to this problem is to add one or more layers of rigid foam insulation on the exterior side of the roof sheathing. This work is best performed when the house needs new roofing.
For more information on this approach, see these two articles:
Insulating a Cape Cod House
How to Install Rigid Foam On Top of Roof Sheathing
That said, anything can be done if you are conscientious, persistent, and have a big enough budget. To do a good job from the interior, it's important to know that (a) It will probably be necessary to demolish your ceilings, and (b) Your ceiling will probably need to be lowered.
If those facts worry you, you should perform the work from the exterior.
In most cases, the use of rigid foam or spray polyurethane foam is safe and doesn't cause any health problems for occupants. In a very small number of jobs, installation errors result in a lingering odor from spray foam -- and that small risk is enough for many homeowners to avoid the use of spray foam. You can use cellulose insulation to accomplish your goal, as long as you understand how to create the necessary air barrier under and over the kneewalls; as long as you can create a ventilation channel under the roof sheathing; and as long as you are willing to lower your ceiling.
Part 2 of my question - Is it ok to blow in dense pack cellulose to the walls of a 1935 small Cape without having a "moisture barrier"? A friend suggested because of the heat/cold differential, there might be condensation, which could moisten the cellulose and eventually damage the frame. The MassSave people say this is unlikely- only in case of ice-dam water damage, for example, would the dense pack cellulose get wet-enough to matter. Thanks very much for your previous comment.
Miriam
Miriam,
All walls need to be detailed to limit air infiltration. However, you don't need an interior polyethylene vapor barrier in your climate.
Most building codes in cold climates (including, as far as I know, the code in Massachusetts) requires an interior vapor retarder; this is a lower standard than a vapor barrier. You can install vapor retarder paint to meet this requirement if you want to -- but frankly, a cellulose-insulated wall will perform well even if you forget the vapor retarder paint.
For more information on installing cellulose, see How to Install Cellulose Insulation.
For information on the best way to detail an insulated sloped roof assembly, see this article: How to Build an Insulated Cathedral Ceiling.
Most 1935 vintage capes have plank sheathing covered with some variant of rosin paper or tar-paper, under shingles or clapboards, and plaster walls originally painted with a fairly vapor retardent alkyd/oil paint.
Even if it's a standard latex on wallboard rehab it's pretty safe to dense-pack the walls.
If you have vinyl siding, it's even MORE moisture safe to insulate with cellulose.
Insulating with cellulose is safer than other fibers due to it's higher capacity for wicking moisture away from the structural wood. Cellulose fibers are hollow at the microscopic level, which allows it to take on quite a bit of moisture as adsorb (not liquid) without damage or loss of function. Even when it feels sort of damp or humid to the hand, it's thermal properties are comparable to when it's bone-dry. Only when it's visibly wet has it lost some of that function.
What is your wall stackup?
Cellulose in netting in the kneewalls creates no risk, but isn't necessarily the best way to insulate that area. MassSave probably wouldn't subsidize it, but a couple of inches of closed cell foam on the underside of the roof deck followed by damp sprayed or cellulose netting under the closed cell foam would convert that mini-attic into conditioned space. Air sealing kneewalls and attic floors in those micro-attic spaces is something of a fools errand- often very difficult to do adequately (trust me on that, having played that fool several times.) Sealing & insulating the soffits & roof deck with 2lb foam works, and will protect the roof deck from interior moisture drives. With 2" of foam (R12-R13) you can then install as much as 5" of cellulose (R18-R19) below that before wintertime moisture accumulation at the foam/fiber boundary becomes an issue. That's a full-depth fill on a milled 2x8 rafter or a full-dimension 2x6 rafter. That's still below code-min for new construction, but probably WAY better than what you have. If the rafters are on standard spacing you could also compress batts designed for 2x6 cavities into the remaining rafter depth to get there. With batts you'll need an interior side air barrier to get the thermal performance, but dense packed cellulose in netting not so much.
The most important thing is to limit bulk water intrusion, which means you have to reliably fix the ice damming problem, which means getting the R-value between the top-plate of the walls and the roof deck as high as possible, so there may be cause to use foam-only right at that location, and foam/fiber hybrid elsewhere.
How deep are your roof overhangs?
Thank you both Martin and Dana. Our roof rafters are 2x6". I'll check on the overhangs .... Currently we only have two roof vents on the rear of our roof. One roofer has recommended sofit, proper and ridge vents to help prevent the ice dams. All this means getting into those knee wall areas too. It sounds like Dana is suggesting sealing the vents if we were to do the 2" of foam and not installing new vents. Am I right? By "wall stack up" do you mean what are our walls made of? They are plaster for sure. I'm not sure about what is inside between the shingles/frame/plaster. Miriam
Miriam,
You have to decide whether you want to attempt a vented roof assembly or an unvented roof assembly. Either approach can work, as long as you get the details right. Your options are explained in my article, How to Build an Insulated Cathedral Ceiling.
Dana- Our roof overhangs about a foot. Miriam
With 2x6 rafters you'd do just fine going unvented, with 2" of closed cell on the underside of the roof deck and 3.5" of cellulose in this climate since that would be ~R24-R25 center-cavity, an the R-ratio would be about 50% foam. Even with R15 rock wool you'd be at nearly 45% foam. That alone would dramatically reduce ice damming potential, but not necessarily eliminate it entirely. But the closed cell foam would prevent the drip-drip-drip from getting to the ceilings even if ice dams formed. As long as you were diligent about using a roof rake to pull down snow from behind the line of the walls whenever snow depths on the roof exceed a foot you'd probably never see an icicle forming. Then when it's time to re-roof, 3" of polyiso would bring it up to a code-max U-0.26 (or R38 "whole-assembly"), which is about the performance of R49 heaped on & over attic floor joists. At that level you might see ice damming in a record snow year if you let 6' cornices build up, but otherwise it would be rare.
The foot of overhang is good. Some capes have about zero overhang, so when ice dams form water backs up behind the siding of the walls, often before it shows up elsewhere. Those housed are a bit harder to treat due to that higher susceptibility.
The foot of overhang also limits the amount of direct rain-wetting of the shingles, which also reduces risk when retrofit insulating an antique.
An example of a wall stack up on 1935 cape might be something like:
outdoor air | cedar shingles | #15 felt | ship lap sheathing | empty 2x4 stud bays | wood lath & plaster | paint | indoor air
I'm pretty sure there's some other layers between your shingles and framing (you can't nail shingles to air), and there might be paint on the shingles (or not).
Thanks again, very much, Dana for your suggestions. Yes, we have paint on the outer side of the cedar shingles. I have no idea what's inside between the shingles and the plaster. Is there a way to figure that out? I also have to read Martin's articles in greater detail. Also, we will need a new roof on the back of the house (it tends to get mossy and a roofer recently recommended replacing at least the back half) so I'm thinking that maybe next year, we could replace the roof and add the insulation. I did buy a roof rake but didn't need to use it this year. Still have to assemble it. Lots to learn....
Miriam