How bad is my insulation?

New home build in zone 5 – about 40 miles north of zone 4. Wall insulation is fine with 2″ of foam outside for EIFS exterior walls and cellulose insulation in the 2X4 walls. Non vented flat roof 2X12 pitch with EPDM over OSB, interior closed cell foam on the bottom side of the roof sheating is 2-3″ thick and the rest of 14″ trus joist are filled with cellulose. I know that I’m shy with the foam thickness but how much trouble am I in? I do have a Panasonic intelli balance 100 ERV installed and no can light in the ceiling areas. I will caulk around all light fixtures in the celings to prevent as much air transfer to the roof joist area. If I am in trouble, what is the best way to correct? Thanks for the responses.
GBA Detail Library
A collection of one thousand construction details organized by climate and house part
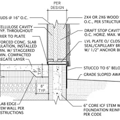
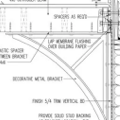
Replies
Matt,
Let's do the math. Here are the R-values for the spray foam:
2 inches = R-13
2.5 inches = R-16
3 inches = R-19.5
Here are the R-values for the cellulose:
11 inches of cellulose = R-41
11.5 inches of cellulose = R-42.5
12 inches of cellulose = R-44.5
Calculating the percentages:
2 inches of spray foam = 23% of the R-value of the entire assembly
2.5 inches of spray foam = 27% of the R-value of the entire assembly
3 inches of spray foam = 32% of the R-value of the entire assembly
In your climate zone, the percentage that you are aiming for is 41%. So I would conclude that you have a problem.
For more information on this issue, see Combining Exterior Rigid Foam With Fluffy Insulation. (Although the article refers to rigid foam, not spray foam, the same ratio rules apply to roof assemblies with closed-cell spray foam and fluffy insulation.)
It's easy to overstate the problem in this stackup.
The roof deck is going to be just fine, since the 2-3" of closed cell foam is well under 1 perm, and it can't take on moisture from the interior rapidly enough to matter over 12 weeks of winter.
The issue is how wet the cellulose gets, since it's in contact with the first condensing surface that's going to be a bit colder than the indoor air dew point over a zone 5 winter. But working in your favor:
* Cellulose wicks and redistributes the moisture and has a substantial amount of moisture buffering capacity before it loses it's insulating function.
** It's a 2:12 roof, a low enough angle that all parts of the roof get at least some wintertime sun, not a north facing pitch that gets essentially none. As long as the roof doesn't have a lot of mid-day shade you gain a lot of margin from the periodic solar heating. The IRC prescriptive is really about has to work for shaded, north facing roofs that get very little help from the sun. That is not necessarily YOUR roof.
If you're freaking out about it, run a WUFI simulation on it, but I strongly suspect you'll be in good shape even without interior side vapor retarders. Worst-case you may need to paint the ceiling with "vapor barrier latex" to limit the moisture accumulation in the cellulose (but I doubt it's really necessary.)
Read this document, but in particular seeTable 3, the column labeled " 2" ccSPF + spray fiberglass", and the rows labeled " 5A
, "5B", "6A", and "7A":
https://buildingscience.com/sites/default/files/migrate/pdf/BA-1001_Moisture_Safe_Unvented_Roofs.pdf
These are WUFI simulations of NORTH facing roof pitches. Even with spray fiberglass (at a fraction of the moisture buffering capacity of cellulose) and a dark colored roof (similar to EPDM roofing), 2" of closed cell is fully protective of the roof deck even in zone 7A.
Dana,
I appreciate your analysis and advice, which is more nuanced than mine. You state your advice with a lot of confidence, and I have every reason to believe that your confidence is based on accurate analysis.
That said, I'm always reluctant to go out on a limb and to recommend deviations from building code requirements (which admittedly are often based on conservative assumptions). The fact remains that lots of unvented roof assemblies have moisture problems -- and that fact makes me conservative.
The bottom line is that this is a judgment call, and Matt is the one who has to make it.
It's absolutely true that it's Matt's call- he knows it's out of spec per code, and seems to be trying to get a sense of just how bad his stackup is.
While I'd never RECOMMEND his sub-code stackup, pointing out the mitigating factors is appropriate, since that's what he seems to be asking. He knows it's "bad" (in terms of not meeting code prescriptives), and wants to know HOW bad. Spelling out just how far it is from meeting the prescriptives doesn't impart a sense of the risks, and what those risks are.
I completely trust Straube et al's WUFI analysis regarding the relative safety of the roof deck, but just how wet the cellulose will become depends on the particulars. Hiring a qualified engineer to run a simulation of his stackup (both with and without the half-perm latex on the interior) would put it completely to bed, but R-ratios that don't meet the IRC prescriptives and still survive the decades are not rare. The roof deck is going to be fine, but the moisture cycling of the cellulose has the potential to be too high, especially if it were a "cool roof" (light colored, highly reflective, which it isn't), or if the roof is heavily shaded, which is unknown.
He's practically spitting distance (in a high wind) from zone 4A, where the code prescriptives call out a hair over 30% of the R to be outside the first condensing surface, and would work even for sunless north facing pitches, even with fiberglass instead of cellulose. Even though it's not quite at prescriptive levels for zone 4, it's close enough, so the REAL solution is to just move the house 40 miles and get out of zone 5! :-)
The science & engineering nerd in me wants to recommend monitoring and tracking the moisture levels in the cellulose at he cellulose/foam boundary for a couple of seasons, but that's clearly not in the cards. It's unlikely to get wet enough to cause visible staining of the ceiling, but it may get high enough to support mold. The fire retardents & fungicides in the cellulose would likely keep mold spore counts from soaring at least for the first decade even if it did accumulate too much moisture. The roof isn't going to rot or fall down any time soon, and if it has problems they'll be fixable, even if it means new ceilings, an additional inch or so of closed cell and new cellulose. It probably won't come to that.
When it's time to re-roof putting an inch or three of EPS above the roof deck would clinch it, but there is little point to ripping any of it up and re-doing it before then unless problems show up.
Ongoing measurements will beat the accuracy of any estimate. If there is a problem, then you have take action (like lower interior humidity).
Thanks for the replies. Dana, you pretty much read my mind, and roof decking was my primary fear, The roof is pretty much full sun with some shading over the garage portion from the 2nd story. With the ERV, I should have a better chance at controlling the humidity.Sometimes the builder doesn't always turn out to be what you hoped/thought and dealing with issues the best I can for the best long term outcome.The builder is really out on a limb as the inspector did not approve the roof (or wall) and he went ahead and finished dry-walling. The inspector says that no cellulose is allowed with CC foam - I think they are using building codes from 2003 here in Indiana and he is still requiring an interior vapor barrier.
Matt,
If the building inspector is requiring an interior vapor retarder, make sure that it is a "smart" retarder like MemBrain.
Matt,
As I'm sure you know, there are two issues here. We've discussed the first issue -- the building science issue.
The second issue is the legal (contractual) issue. It sounds like your builder chose an insulation method that violates the building code. Moreover, it also sounds (if I understand correctly) that the local building inspector did not approve of the builder's approach.
If I've got these details right, it means that you have a claim against the builder. Perhaps the builder will agree to installing a layer of rigid foam above the roof sheathing, followed by new roofing, since this approach would be cheaper for the builder than going to court.