Home buyer with cathedral roof problem in Michigan.

I recently entered a home purchase in SE Michigan and now find myself with a cathedral roof problem. There are cathedral ceilings throughout the upper level of the 2 story home; built in 1979. The main floor living room area is open all the way cathedral roof, and also to the basement with an open stairwell (serious stack effect going on). There is evidence of condensation on the walls coming from the cathedral wood panel ceiling which is attached to the underside of the rafters. The seller reported that they had the “roof done about 8 yrs ago” and then added the current ridge vent a few years after (which is only ventilating about half of the rafter bays). The asphalt shingles are shot and at least 100 SF of rotted sheeting is present.
From opening up a soffit vent during the home inspection, it appears that the roof is constructed with 2×6 rafters (measured exactly 5” at soffit) running from the fascia to a center diagonal beam, like fletching on an arrow. It appears to either have blown in fiberglass or R11 batts in the rafter bays. Owens Corning R11 appears to be present in exterior walls behind the T1-11 siding.
From the research I’ve done so far, it sounds like the best approach to upgrading this roof may be to go over the current roof deck with multiple staggered layers of foil faced polyisocyanurate rigid foam since 4” of available space in the rafter bays will not allow for adequate insulation.
I plan on removing the current sheeting to check the rafter bays for moisture damage. After that I’m a bit lost to what should be done. Would there be benefit to adding insulation to the rafter bays since that would essentially become part of the interior when adding rigid foam above? Would staggered rigid foam atop the sheeting act as an effective air barrier once the soffits are closed off with foam above the exterior walls? Or perhaps it would be best to completely fill the rafter bays with 5” of open cell spray foam, trim flat so that it would be up to the sheeting, then add the amount of rigid foam atop the sheeting needed to get at least a combined total of R38 for the entire assembly?
Thank you so much for assistance, this is a bit overwhelming since we are scheduled to gain possession of the home Nov 16th and should probably have the roof replaced before the snow comes in mid Dec. Having a degree in biochemistry, I also wondering about the potential release of chemicals into the interior from the various insulating products?
GBA Detail Library
A collection of one thousand construction details organized by climate and house part
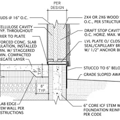
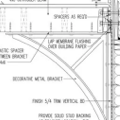
Replies
Brian,
There are many ways to approach your insulation retrofit project. First of all, you need to get a contractor on board. Your contractor should help you come up with a solution.
One problem you didn't mention: your ceiling doesn't have an air barrier ("wood panel ceiling which is attached to the underside of the rafters"). Unless you address the air moving through your ceiling boards -- and out your ridge vent -- your will still have an air barrier problem, even if you add polyiso on top of your roof.
If it were my house, I would install a new drywall ceiling. If you don't want to do that, you can carefully seal the soffit vents and ridge vents with spray foam, and then install dense-packed cellulose in your rafter bays. You won't have an airtight ceiling, but at least you'll stop the exfiltration.
I hope your ceiling doesn't have any can lights!
Probably your first order of business is: demo the roofing, demo the roof sheathing, and demo the existing fiberglass in the rafter bays. Use spray foam to air-seal the soffit and ridge. Then repair rotten rafters and replace rotten sheathing; cover with #30 asphalt felt. At that point you can install dense-packed cellulose.
Then proceed with your multiple layers of polyiso, parallel rows of 2x4s installed flat to the roof (soffit to ridge) to create ventilation channels, new plywood roof sheathing, and new roofing.
Choose a week without any rain. Good luck.
Good advice.
Elaborate further on what to do if/when; ' your ceiling doesn't have any can lights'.
Anthony,
If your ceiling doesn't have any can lights -- congratulations! You win a prize, because that's good.
If your ceiling has can lights, they are energy disasters, and should be replaced with lighting that doesn't penetrate the thermal barrier -- for example, track lighting.
Thank you for the reply Martin. I would likely keep the wood panel ceiling which looks very nice. No recessed lighting – all track lighting. I do understand the need for an air barrier in the roof assembly. That and the condensation control are what I was mostly thinking about.
Wouldn’t completely filling rafter bays to the top with open cell spray foam act as an effective air barrier? There isn’t enough room in 2x6 rafters for adequate insulation needed here in Michigan, but I thought that could be a good start. Then reinstall the osb sheeting and add the staggered layers of rigid foam atop to get a good combined total of R40 or more. When constructing such a roof assembly, I imagine an air barrier could also be made between staggered rigid foam and the pre-existing layer of sheeting.
What is the span of the 2 x 6 rafters? This sounds undersized to me. Normally a cathedral ceiling is 2 x 10, 2 x 12 or greater in order to get the needed R-value in a cold climate. I have used as much as 18" I joists to get superinsulation levels in MN. I would be leary of adding a bunch more weight and insulation to a roof with only 2 x 6 rafters, I would consider rebuilding this portion of the roof.
Brian,
Doug is right: you should talk to an engineer to determine whether your 2x6 rafters are undersized.
It's possible to open up a roof from the top and install spray foam against the top of the ceiling boards. One of the problems is that spray foam can ooze between the cracks of the boards -- and the spray foam becomes visible from indoors. That can be difficult to clean up. However, if the boards are tight enough, that method can work.