High relative humidity in below-grade slab and flooring

I live in the Denver area and am remodeling the below-grade area of the house. It’s slab on dirt, without capillary break (1958), about 4′ below grade, and with soil that is 60% Sand, 20% Silt, 20% Clay.
I have a lignomat concrete moisture meter, that uses the bored-hole approach, and have tested a number of locations.
I’m consistently getting readings 80-93% RH, and I had the RH probe calibrated to confirm it is not off.
Significant drainage work has occurred around the house, with no evidence of bulk moisture, though a seasonal irrigation ditch/stream runs in the front yard, about 100′ away, and this soil drains very well. It is also an atypical year with high precipitation.
If I was to seal or vapor barrier the exposed slab, would this potentially lead to rot or dry-rot of the framing that rests on the slab and stem wall? New framing is treated with a thick layer of glue underneath, but who knows about the 1958 framing.
Thanks.
GBA Detail Library
A collection of one thousand construction details organized by climate and house part
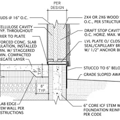
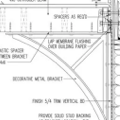
Replies
Ross,
The usual approach to solving this type of problem is to install a layer of polyethylene above the slab, followed by a layer of rigid foam and then plywood or OSB subflooring. For more information, see this article: "Installing Rigid Foam Above a Concrete Slab."
I wouldn't worry too much about the bottom plates of the walls that now touch the concrete. Ideally, these bottom plates should be pressure-treated, of course, but you are correct that with older houses, there is a lower likelihood that treated lumber was used. That said, I wouldn't worry about rot that hasn't happened yet -- the chance of a problem is relatively low.
> If I was to seal or vapor barrier the exposed slab, would this potentially lead to rot
Sure, less inward drying of concrete will lead to wetter concrete. This increases risk for wood in contact with it. Enough to cause a problem? I'd be more interested in the current wood moisture content when it comes to guessing about this. Ie, if it's well below danger levels, then a little more moisture won't hurt.
Martin and Jon, thanks for your feedback. Yes, I was considering a similar assembly, but using MgO board instead of Plywood, which is mold resistant and not affected by water/moisture. I've had water pipes break previously, as well as sewage backup and would only consider a water tolerant assembly. With this (using 5/8" high PSI EPS), I can get to an R3 at 1-1/4" thick, which helps a lot at stairs, etc. This is similar to Basement System's assembly, though they use thicker graphite EPS and very thin MGO.
My primary concern was not being with the current level of moisture, rather if I would drive up the moisture to a dangerous level by covering the slab where framing doesn't exist. I spoke with many flooring persons, and was eventually directed to a mfg sales rep who does large mitigations and is very familiar with this situation, and sees these types of RH values somewhat regularly here in CO (oddly, the flooring guys all were surprised by my numbers and he was not). He was not concerned about a dry rot situation, even with very high slab humidity. The below product would create a tiny gap and vapor barrier between the subfloor and flooring material and allow for air exchange and breathing at the wall. So, I would not have to worry about driving up slab moisture levels as much as a traditional vapor barrier:
http://www.uzin.us/uploads/tx_dddownloadmatrix/RR_185_PDS.pdf
In the event of a bulk water issue, my thought is to remove the Vinyl Plank, pull up this material, hole-saw through the MgO and insulation and vacuum out some moisture in each room, then run a lot of flooring fans and dehumidifiers until dry. After that I could replace the vapor barrier and waterproof flooring. Not that it would be easy, but I wouldn't have to replace the subfloor or buy new flooring.
My only concern is that many of the manufactured subfloor manufacturers create channels on the concrete side of their foam for air exchange and I would not have those. That said, the EPS and MGO would have pretty decent permeability (60 psi foam would have 2.5 perms and absorb only 0.03% H2O).