High density fiberglass batts vs. blown in cellulose for parallel truss.

I am currently building a house in climate zone 6. My walls are
2×6 24 o.c. with two layers of 2″ recycled fiberglass faced polyiso with staggered seams that are spray foamed. I used Resisto Red Zone VP for my weather barrier. My windows are Enerlux casements and fixed units with U values ranging from 15-18.
The structure is dried in and my next step is to insulate the ceiling so we don’t freeze while working on the interior of the structure. The roof structure is a 6/12 parallel chord truss with a 24″ energy heel. I plan on using continuous eave to ridge site built baffles with a 2″ air space using rigid foam. I also plan on not having any penetrations in the ceiling by using 1 1/2″ recycled polyiso against the bottom of the trusses then using 2×3 or 2×4’s strapping running perpendicular to the trusses for the drywall attachment. I will use the space created by the 2 x strapping to run my electrical for ultra slim recessed lighting..,
I have read several GBA articles about potential problems with blowing in cellulose into cathedral type ceilings. My solution was to install two courses of 1 1/4 ” polyiso (8 feet) up from the walls on each side. I would add the strapping to support the foam, then blow in the cellulose. This would be done in stages. I have a very simple roof, two planes, each side running 13′, no hips, valleys or dormers. With this technique, I was thinking I could visually monitor how full the cavities were getting. I was hoping if I filled the lower portions of the ceilings full, there wouldn’t be much room for the cellulose to continue to slide down towards the walls. Towards the peak I anticipated that this would get a bit more tricky, but I would only have 5 feet of ceiling down from the peak to fill.
Just tonight I started reading about the use of high density fiberglass(HDFB) as the HDFB was mentioned in a post debating whether or not Rockwool was worth the added expense vs. fiberglass. The article mentioned that HDFB was a viable option that was priced somewhere between standard fiberglass and Rockwool. Rockwool is not an option as I currently, I can only get 4 inch batts in widths of 16″ in my area. I am not a builder and I have only used HDFB on one occasion, but I remember being quite impressed with how stout it was as the 6″ batts could practically could stand on their own.
In the same article in GBA that discussed insulating cathedral ceilings and the challenges of cellulose, they also mentioned difficulties using batts. I would think the Certainteed 23 1/4″ x 10 1/4″ batts would friction fit between the trusses and that two staggered layers would provide and r value of 76. These batts are advertised to be made for cathedral ceilings. However, my biggest concern is that I’m not sure what would happen in the webbing of the trusses. With cellulose I would guess those voids would be filled. I was wondering if there would be voids every 24″ with the HDFB.
As always, I very much appreciate your input. I read and study GBA practically every night. As stated previously, I am not a builder but I feel I can handle some of the time consuming details required in pursuit of a high performance house.
GBA Detail Library
A collection of one thousand construction details organized by climate and house part
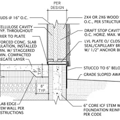
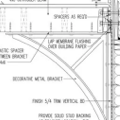
Replies
It is interesting that what you are planning is very similar to what I am contemplating for a future project. The idea is to find the most affordable high efficiency building techniques. I love the idea of recycled poly iso from commercial roofs (this should become more common as many commercial office buildings and malls reach the end of their useful or economic life and get torn down). I also like the parallel cord trusses and simple roof and wall designs instead of the parapets and needless nooks and crannies that are popular around my neck of the woods. I will be interested to see how the experts answer you.
What type of roof material are you using? Steel?
I went with a standing seam roofing and was extremely impressed the roof and especially the vented ridge assembly. A small Amish crew of three came and installed it in about three to four hours. They used rolled steel right off the trailer.
Look around for polyiso. I bought 100 sheets of the 2" material for $11 a sheet and ran six sheets shy of what I needed. I think it's possible to buy straight from the roofing company, a laborer on the job. He got his foam for free. The house is a simple 24' x 36' footprint and a modern raised ranch. I would have liked to have built on grade with a FPSF, but the house is built on a site
where I tore down a house. So my lower level is ICF with 1 1/2" high density foam added to the ICF.
Good luck!!
Batts are possible but a bit more work.
I would get batts made for steel studs as these are true 16" wide, you would have to notch them around the truss members, but each batt would then touch so no gaps. Simpler for the bottom layer to be for wood studs but the same depth as your bottom chord. You can get batts for steel studs from most commercial drywall suppliers, they are a stock item.
I would skip the foam baffles with HD batts, these aren't doing much if anything.
If you end up going with cellulose, with a 6:12 roof, you'll get settling at the ridge. The cellulose will compact towards the walls and slowly slide down over time. The solution to this is to frame a very small mini attic at the ridge where you can blow in extra cellulose to make up for this. The mini attic might also make it easier to fill as you can go in through an exterior gable vent for access.
Thank you for the reply, I have considered adding a small flat section at the peak for the reasons you mention. It would not be deep enough for access though, plus I'm a bit claustrophobic. But the flat section would minimize the sliding. I have started the baffle process and so I have a vented ridge and vented soffits so I will continue down that path.