Help sizing HVAC – Hot2000 analysis included

Hi,
We are building a new home and have been attempting to get an Energuide auditor to analyze our plan for months. We finally received a report from one of the 5 parties we contacted and it is attached here. My issue is that the auditor is telling me NOT to use the report to size HVAC equipment because the Hot2000 software “uses too many defaults”. I am blown away by this response from someone supposedly qualified in this field telling me to let an HVAC company size my system with whatever rule of thumb they feel like after spending the time and money to have a load calc completed. I’m now concerned that he doesn’t know what he is doing and I may be relying on inaccurate data. I’ve reviewed the report and the physical properties of the home all appear to be correct although the windows are tri pane but have similar specs to the ones listed. Is there anything in this report that looks wrong to anyone with more experience at reviewing this type of information?
I note that he has not included air conditioning which is incorrect so I’ve asked him to add and send me the revised report. Our basement is on a separate thermostat as well but I don’t know how much difference that will actually make. The ACH is entered at 1.50 and I’m hoping to hit that. The entire home will be sprayfoamed and I have paid extra to have 2 blower door tests done, 1 after the home is completed for the final Energuide rating and 1 after the insulation is completed but before drywall so we have a chance to find any leaks and seal them up properly.
If I read this correctly the software has calculated I need 52,888 BTU’s of output which equates to approximately a 55,000 BTU furnace at 97% efficient. I will be using a Trane XV95 natural gas furnace so the appropriate size would be the 60,000 BTU model. Am I correct in my logic here? I’m hoping the revised report will also calculate required cooling capacity but it will be a miracle if I ever get that revised report so I may have to guess the AC size.
It literally took months to get this report and weeks to get a first response to my question about HVAC sizing and the missinf AC calc so I’m really hoping someone can review and put my mind at ease or refer me to a consultant I can trust. The house is framed and nearing insulation stage and they have already installed a 120k BTU furnace against my instructions (which they will be replacing) so time is running short.
Thanks for your help and apologies for the long-winded post.
GBA Detail Library
A collection of one thousand construction details organized by climate and house part
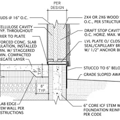
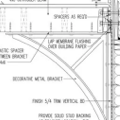
Replies
where is your project located?
Sorry, that is listed on the report but it is Edmonton, Alberta, Canada.
5700 heating degree days
56 cooling degree days
Shaun,
I'm not familiar with HOT2000 reports, but the key information in the report is the following:
[Annual] Design heat loss at -29.20 °F = 47,623.13 megajoules
Calculated* [space heating system] output capacity = 52,888 BTU/h
* Design heat loss x 1.10 + 0.5 kW
Since 0.5 kW = 1,706 Btu/h, we can work backwards from the reported calculated space heating system output capacity to discover the design heat loss.
52,888 Btu/h - 1,706 Btu/h = 51,182 Btu/h
51,182 / 1.1 = 46,529 Btu/h
So according to this report, your design heat loss at -29.20°F is 46,529 Btu/h.
According to what you tell us, your EnerGuide auditor told you orally "NOT to use the report to size HVAC equipment." But that advice is not found in the written report. I have never heard of a professional producing a written report and then advising the client orally that the written report should be ignored. It makes no sense. Either you can depend on the report as written, or you can't.
Mind you, a design temp of -29.2F is fully 6F below the ACCA listed 99% design temp for Edmonton. See:
http://www.energystar.gov/ia/partners/bldrs_lenders_raters/downloads/Outdoor_Design_Conditions_508.pdf
That adds about 5-6% to any calculated heat load. With just any amount of thermal mass inside the house (got gypsum wallboard or plaster on all walls?) designing to the ACCA 99% figure won't leave you cold during the hours that exceed that number, even if you sized the output of the heating equipment EXACTLY to that number.
If you want to take a dumb none-too-accurate rule of thumb as a sanity check, heat loads for code-min houses in an Edmonton climate won't usually be over 180-200 BTU per square meter (16-18 BTU/ft^2) of conditioned space, and tighter-better houses (especially those with lower than average total window area) would often come in under 150 BTU/m3 (14BTU/ft^2). Since your house has more than 11 corners (per the Hot 2000 report, but exact number unknown) it might have more thermal bridging than the average house, but odds are it won't be above the rule of thumb numbers. Two story houses tend to have lower exterior surface area to floor-area ratios than single-floor homes, which also helps lower the BTU/floor-area ratios. Complex designs with lots of bump-outs increase the exterior surface area to floor area ratio, increasing the BTU/floor-area ratios.
It takes a pretty huge house to actually NEED a 120KBTU condensing furnace, but they're pretty commonly installed "just in case" (in case the next ice age occurs? :-) ), since the upcharge is small and the efficiency hit negligible. Real heat loads tend to be much lower than most people believe, until you make them track the fuel use per heating degree-day, using the efficiency rating of the heating equipment as the measuring instrument to calculate the heat load. At 2x oversizing you get more rapid recovery when using setback strategies for fuel savings, but with "learning" thermostats like the Nest or some Honeywell models those recovery ramp start times fairly automatically adjust for seasonal/weekly weather patterns (but not sudden cold-snaps) making it perfectly comfortable most of the time even with UNDERSIZED heating equipment.
Thanks for the great info Martin and Dana. I'm now fully comfortable sticking with a 60k BTU furnace but the builder and HVAC company owner want to meet with me to discuss another reason the smaller unit will not work. They are claiming the blower on the smaller unit will not efficiently get air to all areas of the house. When I meet with them I will be expecting to get a calculation that proves this. Is there a somewhat simple method I can use to do my own calculation? I know the specs of the fans on each furnace so I have CFM ratings for all possible furnace settings and if needed I can go into the house and measure all the duct lines.
Dana, are you an industry professional in the Edmonton area?
Shaun: I'm not in the HVAC industry anywhere (and the closest I've been to Edmonton was Calgary, where some in-laws of mine currently live & work.), but why should that stop me? :-)
But I know how to run heat load calculations, and how to accurately estimate U-factors on different types of stick-built construction, certainly with sufficient accuracy for sizing heating systems, and I run those kinds of calculations with some regularity.
Adjusting the BTUs per conditioned space floor area averages to different locations is simple a linear function on the delta between interior & differing 99% outdoor design temps. In my neighborhood the code-minimums on R values are similar to those in Alberta, the inside design temps the same, but my 99% outside design temps are about -15C rather than -25C. Knowing the range typical BTU/floor area ratios when calculated out with my local ~35C delta between indoor outside design temps, extrapolating similar construction to your ~45C delta is done by multiplying my local typ numbers by 45/35. It won't be a high- precision number (it's a range, after all) but it's not going be off by much.
I don't know enough about issues surrounding duct sizing & cfm requirements to hazard whether your contractors are spot-on vs. out having a spot of lunch. (I'm much better at what's down in the weeds on hydronic heating & ductless heat pumps than ducted-air heating.)
I'm curious how this turned out ... has the house been built yet?
The report assumes a natural ventilation rate of 1.5ACH @50 Pa (p. 10).
Up here (in Yellowknife) when we do plan evaluations as part of the government program or to meet the municipal EnerGuide-80 by-law, we are required to assume 4.5 ACH because it is so hard to be sure that the final building will be air-tight.
Once the home has been built and blower-door tested, the model is revised.
I would think that assuming that a typical Alberta builder can hit 1.5 ACH is asking for a lot.
So ... how has it turned out?
It turned out amazing. We hit 1.3 ACH on the initial test. Getting close to completion but not really expecting much improvement on the final test.
I agree that a typical builder would probably not achieve1.5 ACH. My builder builds a quality house and about 10 years ago he had a blower door test done on one of his homes that taught him a lot about air sealing and he implemented a lot of changes into his standard builds. He only does about 10-15 homes year and builds them with care and attention to detail. He knew the ACH was very important to me so he really went above and beyond with directing the spray foam crew and window and door installers.
Who is your builder? I am struggling with the same issue of hvac sizing for an air source heat pump on a new build right now. I also live in Edmonton.