Prioritizing Details of Construction Plans

Recently finalized the floor plan for our house rebuild post-fire
We are re-using the concrete foundation but everything else will be new from the sill plate on up. Circa 1974 the foundation is uninsulated. I don’t know if there is a vapor barrier under there. Water has not been a problem. Sump pump only runs during heavy spring snow melt.
Draftsman drawings have a few pages of construction details and was hoping you all could help me “value engineer” it. Builder is open to upgrades, but budget will be tight, even with insurance settlement.
Trying to come up with a prioritized list of quality/efficiency features that justify adding a reasonable amount of cost.
I read the PGH book and I’m trying to incorporate what I can, within constraints.
Context is the very northern edge of Zone 5 New Hampshire, about 20 minute drive from Zone 6
Some ideas:
-2″ exterior polyiso foam board over Zip sheathing. Or upgrade to ZIP-R9?
-1″x4″ rain screen battens over polyiso board, under vinyl siding
-how to specify air-sealing details? target 2.0 ACH50 in builder contract?
-omit R-30 first floor insulation, instead insulate basement walls (what R-value?) to bring basement inside conditioned space
-open web floor trusses for first floor to utilities, and to eliminate basement lally columns
-how much of an energy penalty is the R-30 cathedral ceiling in master bedroom?
–Raised heel roof trusses (energy truss) allows full-depth insulation all the way to the edge of the roofline
Any input on pruning this list, re-ordering it or adding to it?
GBA Detail Library
A collection of one thousand construction details organized by climate and house part
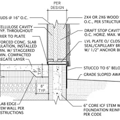
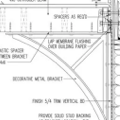
Replies
I went through this 2 years ago in CZ4. Went with a local builder in a small town that has no interest in energy efficient details. Fortunately, the builder was open to me doing some of the work, and open to any changes as long as they were discussed prior to the work taking place. Some thoughts:
1. 2" Under slab insulation and upgraded vapor barrier. Did the work myself. Builder would have done it for reasonable price (~3k) also.
2. 2" insulation wraps up interior basement walls. I did this myself and cut & cobbled the rim joist. This was easy enough, and brought the basement into the conditioned space. I did most of the work after moving in.
3. I mostly took care of air at the rim, but I also had the builders insulator caulk the rim joist. On the outside, I bought Siga tape and the frames applied it to the zip / foundation seam.
4. Rainscreen / exterior insulation would have not gone over well here. Too many expensive and different details. Zip R was an option. On a future home I'll do exterior insulation myself. I went with 2x6 24" OC, but 2x4 with Zip R would have performed better.
5. Open web floor trusses spaced 19.2 OC.
6. Rest of air sealing is drywall. I did have them flex seal the top plate. I also paid for a blower door test, and spot sealed. Manually sealed all electrical / plumbing / etc penetrations. Vents have a gasket and lid.
7. Standard around here is to not tape / flash window rough openings entirely. They just focus on water, and not air. So I had framers properly flash and air seal all openings with Zip Tape.
8. Raised heel trusses were a cheap and very easy upgrade.
9. I asked for deeper blown in attic insulation. Cheap and easy since they are already out there.
10. Better mechanicals. You can optimize a bit here.
11. Better windows. The builder grade windows were awful. I still stuck with the cheap, budget brand that they use, but got their most energy efficient window. It was surprisingly affordable.
12. If you have an attached garage, ask them to Zip the walls for air sealing, and then drywall over the Zip (fire code).
Overall I'm happy as this isn't my forever home. It was more of a PGH test home. On a ~$375,000 house, I spent about $11,000 on energy efficient upgrades + my own labor. Then another $3,000 on builder upgrades (trusses, truss spacing, subfloor type, etc).
Edit: Forgot to mention, blower door score was 0.87.
nice work @veeneck!
wrt to the floor-trusses, did you use a height exactly the same as what a normal i-joist would have been (ie 11-7/8"), or did you go with something taller that required adjustment of plan to accommodate?
Taller. Builder was OK with me doing one or two reworks with the draftsman within reason. Only cost change was the cost of trusses. Added siding, additional steps, etc was not factored in. But my change did not have any huge trickle down costs associated.
did you basically back into the required truss size based on a specific duct size that you needed to thread through them?
if so, just for a datapoint, what size/shape ducts did you use and what size truss did u use to accommodate?
were the trusses custom, or did u go with some pre-fab type?
what were the approximate cost diff between i-joist and trusses?
I was thinking about deflection more than duct size. For ducts, I wanted the extra space, but I didn't pay as much attention to that aspect of the build as I should have. My notes say $1,500 for upgrading to 3/4 advantech and the trusses, but that seems low. Sorry I'd have to dig through the details to get the specifics.
this is exactly the type of reply I was hoping for.
Sounds like you did a great job on some DIY air-sealing. If my builder is hesitant to roll it into the construction plan, I'll offer to do some of that work myself. One convenience factor is that we're living onsite in a mobile home during the rebuild, so I'll be able to visit every day and I can seal any opening noted.
One thing to be careful of is getting the house too tight with no ventilation. I did much better than expected air sealing, so I had to add in some ventilation hacks. Lunos units in the basement that I installed, and timed bath fan vents with air intake. For this type of house I wonder if targeting 1.5 ACH50 would have been better?
I'm planning on adding a whole-house ERV. Do you not have an ERV @ 0.87 ACH? Just exhaust ventilation?
Regarding point 12, wouldn’t properly sealed drywall (think gaskets / sealant at top and bottom plates) also work to air seal the attached garage?
That seems like a reasonable assumption. I did it more as a safety, but you're probably right. The weakest air sealing detail of my build was the ceiling.
The ZIP sheathing will be the air barrier, as long as it is properly taped at all seams. Use some ZIP scrap and line the rough openings of the doors and windows and tape to those around the openings (I saw that on a Steve Bakzek video on Youtube).
Don't use poly on the interior under the drywall - use something like MemBrain instead.
Finish the basement about a year after the house is closed in - there is a lot more moisture drying out of all that concrete than you think and you don't want to trap it behind finished walls - install a good dehumidifier for the whole house, or maybe just in the basement for that year.
Is the attic vented or unvented?
You didn't say why the old house burned down. If it was a wildfire, vinyl siding is not a good choice in a fire zone. Same with vinyl gutters - they just melt and spread fire.
@rockies63 #2
I don't see anything about poly barrier under the drywall on builder spec. I can ask them about adding MemBrain. Is there an IRC code that I can refer to?
Attic is vented: R49 ceiling insulation, R30 in cathedral ceiling (which may be deleted from the drawings for a standard ceiling)
Sorry, did not mention that that basement foundation is not a re-pour. Foundation was not damaged by the fire, so we're re-using it. So concrete drying won't be a problem. There is no insulation under the foundation - is it still possible/smart to bring the basement inside conditioned space if I can't put sub-slab insulation down?
Fire was caused by electrical fault in kitchen stove, which arced across the propane line. We're not in wildfire country
thanks for the reply
I see Zip R+9 as a downgrade from zip covered with 2 inches of foam weaker structure and less insulation.
The rain screen is useful if you live in a rainforest not so much in a desert. It is not a free upgrade only you can decide if the costs outweigh the benefits.
Seem unlikely the builder will agree to any penalties for failure to meet ACH50 goals. I think the best you can hope for is to make it clear to the builder how important air sealing is to you and ask for the subs be made aware of the goal. My contractor allowed me to do a lot of the air sealing.
I like the Idea of moving the insulation from the basement ceiling to the basement walls. If the space will be unfinished storage consider Dow Thermax insulation. https://www.dupont.com/content/dam/dupont/amer/us/en/performance-building-solutions/public/documents/en/179-072601.pdf
Yes it would be nice to have the basement free of posts but unless you have a clear need for the clear space it is not likely worth the costs in dollars and the thicker trusses will add a step or two to the stair case making it a foot or two longer the loss of square feet is a real cost.
I say cathedral ceiling are self inflicted wounds and bests avoided.
Walta
I have heard many building science experts tout the benefits of including a rain screen in most climate zones, and definitely in climate zones 5 and 6. They provide more bang for the buck than almost any other upgrade from standard practice.
Absolutely insulate the foundation walls, not the first floor. The closer together you can get the four critical control layers, the better everything will perform. https://www.greenbuildingadvisor.com/article/an-intro-to-the-control-layers-of-a-wall
regarding bringing the basement inside conditioned space; I should have noted that the existing foundation will be re-used, not freshly poured. So there is no sub-slab insulation. Is it still wise to move insulation from the first floor to the basement walls in this situation? There will be a constant 55-degree heat sink under the slab but that seems a minor loss compared to uninsulated walls near the frost line
I plan to install some sort of drop ceiling in the basement, which will have a home gym and some TV/seating area. I'm hoping the drop ceiling will provide some sound dampening benefits as well even without fiberglass insulation in the joist cavities
I would still insulate the foundation walls; it's nearly impossible to adequately air-seal the basement space from the living space, so the basement will always be a weird in-between space if not treated like conditioned space. Drop ceilings do little for sound; you need mass, air-sealing and, ideally, different-density materials to dampen sound waves.
An uninsulated slab is a suprisingly small heat load even in cold climates. Because of air films and stratification, the cold air settles near the slab and the actual heat loss is minimal.
As other have pointed out, you are better off with insulating the walls and brining the basement fully into conditioned space. A well sealed and insulated basement is a much more comfortable space even with minimal/no heat. It seems a bit counterintuitive but the floors on the main floor will be warmer with a conditioned space VS insulated floors over an unconditioned basement.
A good way to get a poor mans floor heat is actually by overheating the basement a bit. Since this heat is staying inside the building envelope, this costs little extra in operating expense. This won't get you the warm toes type of floor heat but the floor won't be cold.
Michael, I've seen comments in various places that a rain screen detail is not needed with vinyl siding (which the OP noted in his description). Since properly installed vinyl siding requires a space (thickness of a dime) between the nail head and the siding, would that be "loose enough" for drainage? (Thinking of the "value engineering" factor)
That's correct, vinyl siding is leaky enough that you don't need a separate rain screen. Just be sure that the entire house is watertight before installing the siding.
“Water has not been a problem. Sump pump only runs during heavy spring snow melt.”
Before you get started consider replacing the ineffective foundation drains.
The fact that the house needed a sub pump indicate the old drainage system does not work well enough.
It sounds like a lot of the basement will be finished and the only thing keeping it from flooding is your sub pump. What happens when the electricity goes out the spring time?
Walta
automatic battery backup on the sump pump
we lived in the house for 8 years prior to the fire, and never saw a drop of water on the basement floor
I was very impressed with builder Scott True's budget methods. Simple ideas that appear to be very good. Mind you he is in TX I think, but you could adjust for your climate.
https://youtu.be/G3wBb2Z1FSo
Here is a link to the Matt Risinger video where he visited one of Scott's building locations. If you search his name on Matt's videos there are a few with him and I found them very good.
ha that video is in my "Recently Watched" YouTube history already!
basement floor. cover with 1" rigid. drop 1/2 hardi backer tile board on top. tap con each sheet with 6 screws and in my experience....it will not move. the weight of the hardibacker alone keeps it in place. I did this just north of you in Campton, NH and made a huge difference. Totally respect Akos he is wicked smart, but, disagree for zone 6 applications
regarding open web vs i joists. I priced both out for my new build. the open web pre-manufactured joists were 2x the cost of i joists. custom open web were much more money. look on Menards site for current pricing.
I'm in the north edge of zone 5 (~7200 heating degree days). I have checked places with finished basement with an uninsulated slab with nothing but vinyl click over the floor. The floor temperature in the winter was generally only a couple of degrees bellow room temperature, that means the heat loss there is pretty small. This matches with the heat loss calculations pretty well.
This was a reasonably insulated and well sealed (spray foamed rim joist+batts) basement.
Usually the cold basement floors are not because of uninsulated slab but air leaks. Once you fix the air leaks, floor insulation is nice for comfort but not really needed otherwise.
I am not smart enough to dispute your claims. I have learned much from your posts and you have my deepest respect. My experience is real world, not computer based. I waited a season after doing my walkout basement over and airsealing and insulating to above code standards. The floor level was still VERY cold. Once I put an paltry 1" of rigid on the floor it got much better and more important more comfortable. On my 3 car garage, in different location zone 5, I put 6" of reclaimed insulation under concrete which I planned to heat with radiant (12 years ago). The garage ended up so warm that I never hooked up radiant and only heat sometimes with mini-split. I attribute this in great part to the floor insulation.
just my opinion for the OP who sounds like they live 1/2 between both of those projects.
Walkout is a different story. If there is no exterior foundation insulation the slab in a walkout will be very cold.
If you use the basement as a living space the inch or so of rigid does make a big difference in comfort no matter the house configuration, worth the additional cost in cold climate.
good food for thought from you both
my basement is full-foundation below grade, no walkout. Just a bulkhead door to a doghouse hut.
Basement will not be living space, but home gym and lounge/theater area
The IRC is getting pretty particular about the use of I-joists in floor systems: the I-josts are required to have a fire-resistant coating on BOTH sides of the OSB web OR be clad with drywall. There *was* a manufacturer producing coated I-joists but it looks like they've been discontinued. My local (Merrimack, NH) building inspector requires drywall installed across the bottom of first floor I-joists above a basement to increase the fire safety margin due to their reputation for collapsing during a fire. (The inspector may be pickier than some because our building department is associated with the fire department.)
I opted for TriFORCE open-web floor joists in our current build: they comply with the 2015/2018 IRC fire rating, are field-trimmable up to 24" eliminating the need for custom-manufactured trusses AND eliminating the hassle if a regular truss needs to be trimmed on site, and they don't have the nasty metal plates on each web-to-chord connection. That 24" trimmable section *should* be clad with drywall to adhere strictly to the IRC fire specs, but that beats cladding an entire I-joist.
The trusses ARE much more expensive than 2x12s (about 2x per linear foot), but they're a much better use of materials than a solid-sawn 2x12, they're absolutely flat, and the open webs making snaking utilities through them a walk in the park. FWIW, one of my neighbors-to-be had an issue with a "wild" 2x12 floor joist interfering with tile installation, and the builder had to replace the joist.
Weyerhauser had introduced "Flak Jacket" TJIs with an integrated intumescent coating but they were discontinued due to an odor problem: https://investor.weyerhaeuser.com/2017-07-18-Weyerhaeuser-issues-statement-regarding-TJI-R-Joists-with-Flak-Jacket-R-Protection. Like you, I use Triforce when they will work; unfortunately their smallest size is 11 7/8" so they don't work on every project.
for air sealing try Aerobarrier. there are a couple of reps in NH area. Not sure why it is not discussed more on this site. With a need to get a blower door test anyhow....it is an all inclusive package.
“For air sealing try Aerobarrier. there are a couple of reps in NH area. Not sure why it is not discussed more on this site.”
I like the idea but it seems Aerobarrier has decided their target market is lazy contractors that refuse to put the slightest effort into building a tight building.
The pricing seems somewhat reasonable in order to pass the code required blower door test as it is a flat price for new construction. If you want anything tighter the pricing seems very high.
Walta
following up on this post as we get closer to a final contract with the builder
from reading between the lines, he is willing to do energy upgrades but charging big bucks to discourage it.
For instance, adding 2" exterior polyiso insulation: $28,000 upcharge
Switching standard roof trusses to raised heel energy trusses: $18,800 upcharge
This surprised me because his base price of construction is near the low end compared to other local builders.
I get the impression he has subcontractors that have a certain way of building, and any deviation incurs a premium price.
I'll probably opt for the exterior polyiso but skip the raised heel trusses
Why not look for another builder?
Time and money
We’ve been living in a trailer for six months after a house fire. He’s available, reasonably priced, and does good enough work. I’m just trying to squeeze in some upgrades
I don't think he is reasonably priced anymore....
That is insane and unethical. Raised heel trusses cost a few dollars more than trusses that will create ice dams. Exterior insulation does cost more, but not that much more.
Unfortunately the 2" plyiso upcharge will never pay in energy savings. For a normal sized house that is about $3k in materials about two days to install, not sure where the rest of the cost is from. Feels like they simply don't want to do it.
I would find out if he will build a simple 2x8 24" wall with R30 batts instead for a reasonable upcharge.
From the "For what it's worth" department:
I would be nervous going with exterior rigid insulation IF you were not fully confident in the ability of your builder / his subs to properly detail the window openings. There's no "magic" involved but there *is* a great deal of attention to detail that is needed, and if you're dealing with someone who has "a certain way of building" odds are you're not going to be happy with the end result.
RH Irving Home Builders in Salisbury might be worth a look as an alternative to the builder you're currently dealing with - who quite frankly seems uninterested in *your* desires.
Talked with RH Irving a couple months ago and they declined the job as they are too busy
I do not blame anyone for throwing a high number at something totally new.....like exterior foam. A lot can go wrong if the person doing the work is not genuinely interested in getting the details right around windows and doors.
Leaks usually take years to show up because most are just the seeping type and not pouring thru a wall.
Personally, Taking on liability for something I have never done before is scary sometimes and deserves a high number. Sounds like thats where that guys head is.
However it sounds like you are getting outright shafted on the energy heel truss.
Unfortunately, right now everyone is busy. Just getting a return call is a huge bonus.
I would take the above advice with 2x8 wall....that way the guy can stay in his comfort zone.
dirkgently,
I agree. A couple of years ago I solicited a quote from a builder to replace all the old cedar siding on our 1930s community center. It was much higher than I had expected, especially as the builder had just done the same work on the fire hall next door, so he knew exactly what was involved.
When I talked to him, he admitted he really didn't want the work, and so quoted a price that would convince him the job as worth taking on if we accepted it.
There are all sorts of reasons for high quotes, ranging from caution to straight out gouging. It's often hard to find out which motivation is driving them.
It could be this contractors normal pricing strategy to bid low when seeing a poorly thought out set of plans reusing parts of the old structure that all but guarantee there will be mutable change orders that he can price outrageously and make big bucks.
If you have signed the contract the smart move maybe to never visit the job site so you will not be making any changes.
Walta
I've been in a similar situation during my home renovation. Prioritizing quality and efficiency is key. I'd suggest focusing on good insulation, air-sealing details, and raised-heel roof trusses for energy efficiency. Basement insulation can help, too. Start with those, and you can always consider other upgrades down the line. You can contact https://romanattorney.com/practice-areas/construction-regulatory-compliance-approvals-and-permitting/ to get clear on the legal side. Good luck with your project!
Deleted