Help me review my wall and roof insulation plans to spot errors

I’ve read all the articles and threads I can find and I figured I’d ask some people on here and get an honest opinion.
My current plan is a 2×4 or 2×6 wall using advanced framing techniques 2ft oc and use rockwool bats in the wall cavity. Then exterior zip sheeting taped and liquid flashed to the best of my ability. Here’s the part where I have some confusion. How much insulation would I need to use to achieve the required amount of insulation on the exterior to prevent moisture problems. I see the 2/3 rule and then also there’s a chart that’s says something like 36% of the exterior wall needs to be rigid foam layer. This confuses me but I think it’s the last hiccup I need to work over. My plan is to use a smart vapor barrier inside such as membrane. My goal is to reach an r r 30 or better and if I can achieve that with a 2×4 wall that’s fine but if a 2×6 wall is needed I can do that as well.
I then plan on a trussed roof and again I run into problems. I’m fine with a thick layer of blown in above the ceiling but is the most efficient way again a smart membrain and then vent the roof accordingly? Should I be using say zip on the exterior ceiling to prevent air leaks or what would be the best way? I could also add several layers of insulation to the outside of the roof deck. I really haven’t gotten the exact way that roof insulating is done best I’ve gotten much further with learning about wall insulation.
really appreciate all the knowledge I have gained reading through everyone’s questions and seeing the answers this forum is a treasure of knowledgeable people and articles. I’m starting to better understand the principles of vapor mitigation and better insulting techniques but I still like to ask about my master plan
Thanks, Tom
GBA Detail Library
A collection of one thousand construction details organized by climate and house part
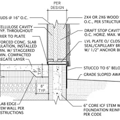
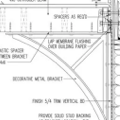
Replies
Hi Wiscoguy, I saw in your other post about windows that you're cz6, so that ratio you described is correct: 36% of your insulation needs to be on the outside. That quantity will of course depend on if you go with a 2x4 or 2x6 wall, but that's the minimum ratio in either case.
If r-30 is your goal, you can use a 2x4 filled with an r-15 Rockwool Comfortbatt, and then put 3 inches of polyiso on the exterior. That 36%-rule is a minimum; you can have more on the exterior without a problem. That thickness of polyiso is relative to it's r-value of course, which is at listed as r-6, but in colder climates is de-rated to somewhere between r-4 and r-5. That'd put your wall somewhere between r-27 and r-30.
If you moved to a 2x6 wall you could put an r-23 Comfortbatt in there, but would still need at least 3 inches of polyiso to meet that 36%-rule. Note that this is slightly under the 36%-rule if you use the conservative derated r-value, but there's evidence to suggest that it may be less risky than initially thought. This risk depends on some factors outlined in this article: https://www.greenbuildingadvisor.com/article/rethinking-the-rules-on-minimum-foam-thickness
Anything over a couple inches of exterior foam gets more complex to install, so just a heads up on that.
As for the roof, a vented roof is a safer bet; but I'll let those with more experience in the differences chime in.
I have xps foam readily available in my area is this an acceptable susititute also graphite foam board is in my area in many thicknesses is there any drawback to either of these. Appreciate the reply.
Xps foam is one of the worst, if not the worst, foams from an environmental standpoint. The blowing agent in XPS has a global warming potential of around 1400 times worse than cO2, if memory serves correctly.
The graphite foam board (Neopor?) is essentially EPS foam which is much better from an environmental standpoint as the blowing agent is pentane. I can’t remember the exact GWP off the top of my head, but way lower than XPS.
EPS is also much more vapor open. It depends on the thickness you land on, but I believe a 3” thickness would put you at a perm rating of 2.5 if my math is correct (and it may not be; someone please correct me if I’m wrong). XPS is much more vapor closed; 3” lands you at about .6 perms. Even if the global warming potential thing doesn’t resonate with you, the drying potential of EPS seems worthwhile.
Finally, both XPS and EPS have lowere r-values than PolyIso. You’d need to recalculate your assembly thicknesses to meet that 36% ratio.
You may be able to find reclaimed PolyIso (Craigslist seems like a good place to find it from commercial roof resellers) for a lower cost than new EPS or PolyIso, particularly if you’re close to the Milwaukee/Chicago/Twin Cities triangle.
Thanks for the reply. My understanding is polyiso doesn’t perform as well anyway in the cold. The other thing I thought I understood is if I use a product like zip or any other weather barrier I’m essentially going to be relying on the foam keeping the sheeting warm and the vapor membrane I’d be using on the inside for moisture mitigation. I guess otherwise I could use a product like delta sa which is actually vapor permeable the same way that neopor is vapor permeable as well.
The "doesn't perform as well in the cold" issue with polyiso is often overblown. Even if you derate polyiso from the usual ~R6/inch to R5/inch, it's still performing as well as XPS, and a bit better than EPS. All the rest of the time, polyiso is outperforming both.
I'm going to have to build up a test rig and publish some data on this. I actually have the parts, just not the time (yet). Hopefully soon!
Bill
Bill’s comment about the de-rating being overblown (which is a great pun, btw) is true.
It’s also worth mentioning that the de-rating only really applies to the outermost portion; that is, that outer inch keeps the inner pieces warmer which allows them to perform closer to their rating. So your assembly in a thickness of 3” may perform closer to r-5.5 (just a guess). And again, like Bill said, that’s just when it’s the coldest. The rest of the time you get the full rating.
But you’re correct, the ZIP sheathing is your air barrier, and the insulation is just keeping it warm. If you were so inclined, you could ditch the foam and use Rockwool Comfortboard on the exterior as well.
As far as the trussed roof goes, vent the attic. Air/vapor seal the ceiling (air seal the drywall layer). Insulate the attic with whatever you want, usually loose cellulose or Rockwool, and since you're in a reasonably cold climate I would order raised heel trusses so you can get more insulation near the eave area.
For the roof itself, use whatever sheathing you want (ZIP works well, but not necessary) and then full 100% ice and water shield on the entire roof. The roof won't "breath" anyway. There are several studies proving there is effectively zero drying to the outside of any shingled roof. So in my opinion, you may as well pay a little extra in cold climates and ice and water shield the entire roof for better protection in case some shingles blow off or break down early. Skip any other membrane as it would be redundant.
Thanks guys
I struggle with the super air tight nonpermeable zip sheeting I have considered plywood or osb with the delta sa barrier that’s self adhered because of its permeating and then roxul on the out issue for more breathability being in zone 6 I’m not sure if this would give better piece or mind or just complicate the whole enclosure.
I say this reference to the suggestion of using rockwool. Not that I disagree more that I’m wondering if a better breathable wall would do better in this climate or stick with the super air seal of a zip sheeting that has basically no perm.
Thoughts
I may be mistaken, but I thought the standard green ZIP (the coating; not the OSB itself) had a perm rating of 12-16.
I know that other Huber products like the roof sheathing and AdvanTech subflooring have lower; maybe you could point us towards a specific tech sheet?
Yea zip is less than 1 perm rating. This is why I’m slightly unsure of it up north although I’ve been told as long as you use a smart membrane on the inside and the correct amount of insulation you should be ok. That’s why my other thought was standard plywood or osb and then delta sa fully adhered membrane because it has a higher perm rating. I feel like there’s benefits to both.
Thanks for posting that; I think I see where the confusion is.
The line highlighted in red on my attachment is relative to the foam on their Zip-R (the Zip plus the foam); not the overlay itself. The line highlighted in yellow is specific to the overlay.
Since you’re using exterior foam, you don’t need Zip-R, just the regular Zip. Admittedly Delta-Vent SA does have a higher perm rating, but I’m not sure that it adds much in your case with the exterior insulation.
I gotcha now. So in theory then using rockwool on the outside of the wall would still allow for some breathability rather than foam. I’m not sure what the cost benefit comparing each which would work better. Polyiso is much easier to work with I’d think and to build out windows etc. that’s a tough one.
Would I still want to use a smart membrane on the drywall side of the wall to allow vapor to move through the wall both ways no matter which product I would use.
For walls, ZIP - hands down. Nothing else comes close in my opinion for quality of air/vapor seal, and ease and speed of installation.
For interior wall insulation my preference is Rockwool. And no additional vapor barrier or membrane on the drywall side.
For exterior wall insulation I'm still undecided as far as Rockwool comfoboard or EPS/XPS foam board. I believe the Rockwool board is a better technical solution, but I'm not sure about the installation. If you need 4" or more, I can see it being a process of running a string and tightening/loosening the screws to get the wall perfectly flat. And I don't know how well that will stay flat over say 30 years. If I only had to put 1" or 2" of external insulation it would be ZIP-R, no questions asked. Nail it up, tape it quick, and you're done.
It’s also probably worth pointing out that the OSB part of the assembly will only have a perm rating of 2-3 whether you go with Zip or Delta Vent.
But the rules still apply .36 more rigid insulation on the exterior of the wall and there’s shouldn’t be a moisture issue as long as a smart vapor barrier is on the inside of the wall. If I’m thinking about that correctly.
Yup, you got it. The sheathing should be warm enough that it’s not a condensing surface at that point. That’s why the vapor permeance becomes less of an issue; or at least less worth worrying about 16 perms vs 31 perms, or whatever.
And, as far as the interior vapor retarder goes, a double-coat of paint over gypsum that is sufficiently airtight will work since you have exterior insulation. However, you may have to have one depending on your inspector/code. In that case, MemBrain by Certainteed is probably the most economical choice.
And relative to your question above, exterior Rockwool would be more vapor open, but would need to be thicker which will probably complicate things a bit.
I’ve also heard that at those thicknesses Comfortboard can be compressed slightly when you’re putting your rainscreen battens on which can make your siding look wavy. I don’t have any direct experience with that, but worth considering.
My problem would be convincing the local building inspectors that no 6 mil plastic is necessary in a wall assembly a smart vapor barrier would be easier to make happen in my area of Wisconsin. Many inspectors will come back to jobs just to check the vapor barrier is installed but then again many of them do not have experience with heavy exterior insulation techniques either. I may have to print off the building irc chart that shows drywall is acceptable.
Thank you for all your insights. I don't know if this makes sense at all but I have become absolutely fascinated by this subject. I'm planning to take the passive websites classes and courses for builder and designer. For some reason this resonates with me on a deep level. Not only building green because I'm an outdoorsman but also to try to find ways to build better homes and try to get others on board and i feel like through these discussions and with others that i will be able to convince others to also develop better building practices that are cost effective for those builders building on shoestring budget.
I totally get the inspector thing. The nice thing about the MemBrain is that it won't really hurt anything in your assembly, so if that's what it takes to satisfy the inspector at least you know it's not doing harm.
I'm with you on the fascination with the topic. I've been the beneficiary of a ton of smart answers on GBA over that past few years where people have really gone out of their way to walk me through the concepts, so it's nice to be able to help out where I can.