Help! Insulation for exposed floor — nightmare reno

I bought an old cottage home on pillar and beam, climate zone 5a I believe (Nova Scotia Canada), used as a year round home.
Unfortunately during renovation work, found the building to have more issues than we thought.
After taking up the existing laminate floor, there was 1/2″ plywood sub floor with attached lino sitting over the original 3/4″ plank sub flooring over the joists.
The home has at least 1′ clearance all around after repairing the old posts and there was previously osb with old polystyrene used for a skirt / crawlspace boarding.
The home will now be heated by 2 split heatpumps and a wood burner leading to me to ask how to best approach the floor now its leveled, as I’ve no experience with this type of building.
I had thought of the following:
1. insulate with a 1″ layer of xps and then 1/2″ plywood – over the plank sub floor and covering with laminate floor.
insulate beneath in between the joists with R22 Rockwool batts (should be better suited than fiberglass ?)
2. spray foam underneath and cover with pressure treated ply / osb to keep rodents out
3 insulate under the floor between joists with R22 Rockwool and then re-skirt the building with pressure treated plywood backed with 1″ xps foam
apologies with the lengthy question but no local contractors can give me a solid answer and I’m racking my brain trying to solve this so we can move in before winter.
GBA Detail Library
A collection of one thousand construction details organized by climate and house part
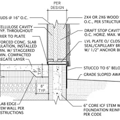
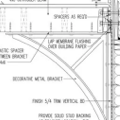
Replies
John,
The short answer is that you should read this article, which tells you what you want to know: How to Insulate a Cold Floor.
The longer answer would raise questions about the viability of a post foundation in a cold climate. The biggest problem is figuring out how to keep your water supply pipe and your drain pipe from freezing.
Eventually, you may get sick of the disadvantages of a post foundation, and you may decide that you want to install poured concrete foundation walls to create a true crawl space.
If that's too expensive, you can build an insulated skirt out of quality materials (pressure-treated plywood and rigid foam, installed with attention to airtightness).
You may want to read these two previous Q&A threads on this topic:
Insulating a crawlspace
Unvented, sealed crawlspace under pier foundation
FWIW, most of Nova Scotia is zone 6, not zone 5, which may make a difference if following IRC prescriptives. Warmer southern coastal areas moderated by the Gulf Stream (eg Yarmouth to Halifax which see ~3800-3900 HDD base 18C per year) are warm enough to be the cool edge of zone 5. If your location averages over 4000HDD (eg Truro: http://truro.weatherstats.ca/charts/hdd-25years.html ) it's zone 6.
It often takes less material to close-in a pier foundation in an air tight fashion & insulate the skirting than it does to air seal & insulate the floor.
Thank you for the quick replies and feedback,
Unfortunately this is my first home and I neither have the finances or ability to change to a different foundation type, I have to work with what I've got.
I replaced the old posts (treated railway sleepers) with cinder blocks on jack pads and then filled the holes in the cinder blocks with 1/2" rebar and concrete for rigidity / mass - I should be able to bold a skirt to this using gasket material and pressure treated 2x4 as the Crawlspace article lists.
In regards to this method, would there be any Pest / Moisture issues associated with spray foaming under the floor ? - this would enable me to get the floor air sealed but I'm worried about Moisture / Pests getting to it, the previous extension that was tore off had been eaten through by ants.
Thanks again, GBA has been the biggest help with this disaster so far and I'm extremely grateful for the site and contributors.
John,
Q. "Would there be any pest or moisture issues associated with spray foaming under the floor?"
A. Concerning pests, there are no guarantees. Lots of creatures like crawl spaces, including raccoons, squirrels, and mice, and these creatures know how to gnaw and chew.
If you want to install insulation between your floor joists, you should protect the floor system with a continuous layer of OSB or plywood fastened to the underside of the joists -- no matter what type of insulation you install. The OSB or plywood will reduce the chance that pests will enter the floor assembly, especially if the OSB or plywood is installed with attention to airtightness.
Concerning moisture, I wouldn't worry. In general, closed-cell spray foam is associated with fewer moisture problems than open-cell spray foam.
If you're going to foam the floor as a means of sealing it, 3" of open cell foam does the trick, below which a full joist-depth fill of fiber insulation is in order. Rather than OSB or plywood, sheath the bottom with asphalted fiberboard. The combination of 3/4" + 1/2" subflooring has a vapor permeace that meets the Canadian code definitions for a "vapour barrier", and as long the bottom sheathing isn't too vapor tight there will be no accumulation of moisture in the cavites. Asphalted fiberboard is ~10x more permeable than your stacked subfloor at any humidity level, and it's quite moisture tolerant, even if there is a plumbing leak. OSB/plywood sheathing is at once more moisture-retentive, as well as more susceptible to damage from moisture.
If you went with a full layer of rigid foam board under the joists it would have to be pretty thick to achieve dew point control, and would be too tight for the assembly to dry to the exterior. If you wanted to get some amount of thermal break on the joists to avoid chill-striping on the floor during breezy -20C days, cut strips of 1.5-2" thick foam board (any type, whatever is cheapest) and cap-nail it to the joist edges, and continue the fiber insulation all the way down to the fiberboard sheathing layer.
If rodents are a serious risk in your neighborhood, half-inch mesh hardware cloth stapled to the underside of the sheathing is a pretty good barrier. (I once had to resort to prevent some very ambitious squirrels from re-chewing through the siding & sheathing of a wall, after other deterrence methods had failed. It was never clear to me what the attraction was in that section of wall, but they were persistent!)
Building up the skirting in to a reasonably air-tight configuration will offer a substantial benefit on windy mid-winter days, and limit plumbing freeze-up risks.