Hello to all! I’m looking at bringing the attic of a 1940s home into conditioned space

I have a few concerns: 1) there is currently a mix of blown-in cellulose insulation and fiberglass batts – does this need to be removed? 2) there’s quite a bit of K&T wiring on the attic floor and some on the lower part of the rafters – is that a concern? 3) I’ve read and agree that closed cell spray foam is probably the best option for our zone (5), however, given cost I’m investigating the possibility of about 9″ of open cell Agribalance (Demilec) – any thoughts on this? Thanks so much.
GBA Detail Library
A collection of one thousand construction details organized by climate and house part
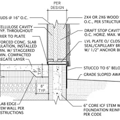
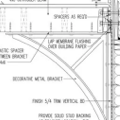
Replies
Luke,
You can leave the existing insulation on the attic floor if you want, but if it is dirty it might be worth removing.
If I were you, I would remove the knob-and-tube wiring. Of course, if this wiring is still in use, the wiring will need to be replaced, and this work will need to be performed by a qualified electrician. For more information, see this article (including the comments posted below the article): Borrowing a Cellulose Blower From a Big Box Store.
Either open-cell spray foam or closed-cell spray foam can work, as long as the insulation is installed correctly and detailed well. For more information, see Creating a Conditioned Attic.
Dear Martini,
Thanks for your speedy response.
I've read all the articles (and more) you mentioned and I've found them, as well as the discussions, to be an invaluable resource.
To respond, my customer is also having his roof addressed and is definitely working with a specific budget. I've recommended this approach so he can eliminate the need for soffit/ridge venting, but also stay away from addressing the K&T. I just want to make sure that this is the right approach.
With regards to the open cell, my concern is with moisture/vapor. I have a letter from the manufacturer stating that after thousands of attic encapsulations, they see very little issue with vapor issues. Wondering if that is true. My other concern that I just discovered, after speaking with Demilec's rep, is that open cell isn't an air barrier. Reading other resources, I thought that after a certain # of inches, it was....
Thoughts?
Thanks again for your help.
Luke
sorry for the additional "i" on your name...
9" of Demilec does not meet the R49 IRC 2012 code min for zone 5.
Closed cell foam between rafters is a waste of foam, since such a large fraction of it's R6/inch potential performance is undercut by the R1/inch rafters. Hitting R38 or R49 with closed cell foam is also a significant environmental hit- it's about twice the amount of polymer per R as open cell, and the HFC245fa blowing agent has a global warming potential ~1000x that of CO2, quite a hit compared to the blowing agent for open cell foam, which is water.
To figure out the greener-cleaner-cheaper way to go we'd need to know:
How deep are the rafters?
Are you planning to replace the roofing any time soon?
Open cell foam is an air barrier,and air seals at least as well as closed cell foam- the rep is simply mis-informed.
But the higher vapor permeance is still an issue depending on the stackup & thickness.
Thanks for your comment Dana.
The footprint of the attic is roughly 13' x 48', with 2 x 4 rafters, and is 4.5' at the peak. It is 16 OC and does have horizontal trusses. Originally, an option I was considering was 3-3.5" of closed cell but I knew I would only get about an R21-22. Then I thought some combination of ccsf and fiberglass batts could be an option, however, I don't really like the flash & batt approach.
He's already put down the deposit for the roof and will be proceeding shortly (pending weather). I thought at 9", approx R38, meet code requirements..?
Also, while we're on the subject of K&T, is blown-in fiberglass acceptable? I know that cellulose and spray foam are not acceptable, but haven't read anything about fiberglass. Some contractors say yes, some say no. Looking at the code, I don't believe there is any acceptable form of insulation that can be used against active K&T...
Thanks!
Luke
Luke,
Even though the chance of fire may be low, I strongly advise that you not install any insulation against knob-and-tube wiring. That would be a code violation, and you don't want to face the legal nightmare that would arise if there is every a fire in this house.
In Climate Zone 5, you want to aim for R-49 of insulation. That is the minimum requirement in the 2012 IRC, and it's a good idea as well.
In your climate zone, you definitely need an interior-side vapor retarder if you insulate this roof assembly with open-cell spray foam. The best way to achieve that is to install gypsum drywall on the interior side of the cured spray foam, and to then install a layer of vapor-retarder paint. This work isn't cheap, but it is necessary to avoid moisture accumulation.
Thanks for your response Martin.
We always insulate at R49, however, just to be clear, this would occur on the underside of the roof deck and not at the floor level. Given that, I believe the code is somewhat dictated by the rafter sizes - are we talking about the same thing? There is a provision in 806.4 for "condensation control" which says that R20 is required for our zone; this is achieved with rigid foam board but does not state any provisions with any other types of insulation.
Luke,
Q. "We always insulate at R49. However, just to be clear, this would occur on the underside of the roof deck and not at the floor level."
A. I understand that.
Q. "There is a provision in 806.4 for 'condensation control' which says that R-20 is required for our zone; this is achieved with rigid foam board but does not state any provisions with any other types of insulation."
A. The R-20 requirement refers to the minimum acceptable R-value in your climate zone for rigid foam installed above roof sheathing when you intend to install some of the insulation above the roof sheathing, and the rest of the insulation below (and in direct contact with) the roof sheathing.
This R-20 requirement for the rigid foam layer does not absolve you of the need to meet the total R-value requirement for the entire assembly -- usually R-49 in your climate zone, but sometimes less depending on which code has been adopted by your local jurisdiction. The R-49 is achieved by installing R-20 of rigid foam above the roof sheathing, and a layer of R-29 insulation below (and in direct contact with) the roof sheathing. All of this is explained in the following article: How to Build an Insulated Cathedral Ceiling.
Thanks again for your response.
Understanding that there are three preferred methods of insulating a cathedral ceiling (a bit off topic from the original question), I understand that a combination of closed cell spray foam (underside of sheathing) and an air permeable insulation (fiberglass batt) is acceptable. My question is how is it possible to obtain an R49, given 2x6 rafters? Applying 1.5" of ccsf is roughly R12 + an R19 batt, would only yield an ~R31...
Luke,
Q. "How is it possible to obtain an R-49, given 2x6 rafters?"
A. The answer can be found in one of the articles I linked to: How to Build an Insulated Cathedral Ceiling.
The article notes, "Most rafters aren’t deep enough to accommodate the insulation needed to meet minimum R-values required by code, especially if the rafter bays include a ventilation channel. For example, 2x10 rafters are 9 1/4 inches deep, so they only provide room for about 8 1/4 inches of insulation — in other words, about R-30 of fibrous insulation — if the rafter bay is ventilated. This is less than the minimum code requirement in colder climates.
"Builders solve this problem by furring down or scabbing on additional framing below the rafters to deepen the rafter bays. Another technique is to add a layer of cross-hatched 2x4s, 16 inches on center, installed beneath the rafters. It’s also possible to specify deep open-web trusses or to use deep I-joists for rafters."
For a more thorough discussion of this issue, read the article.