Height of (SmartSide) wall sheathing with 12″ rimboard?

My basic question is whether to use 8′ sheathing/siding panels that barely cover the height of my exterior walls or much more expensive 9′ panels that extend down over most of my rimboard.
My single-story 20×48 house is in central Arizona where we have a Wind Design Speed:of 90 mph – Exposure C and a Seismic Design Category: C, The 8′ walls are framed 16″ oc with 2x4s making up the outer half of a double wall. The walls rest on an OSB subfloor that rests on a 12″ rimboard and i-joists supported by a 2×6 sill plate atop a 30″ masonry stem wall.
I will use SmartSide panels as sheathing and siding. The total height of my wall from bottom plate to top of double top plate is 97-1/8″, 1-14″ more than the 8′ panels that are actually 95-7/8″ high. If I use 4×8 panels, they could extend from 1/2″ above the bottom of the bottom plate to 3/4″ below the top of the upper top plate. If I use 4×9 panels, they could extend from 1-1/4″ above the bottom of the rimboard to 3/4″ below the top of the upper top plate (or 3/4″ higher at both ends).
I understand that the taller sheathing/siding would tie my walls to my rimboard better, but it would cost $700 more, which is significant on my budget, and it would still leave 1’1/4″ of rimboard and the 1-1/2″ of sill plate exposed.
How much benefit would the taller sheathing confer in my wind and seismic conditions? If much, is there a less expensive way to accomplish the same thing with hardware?
How do people typically cover the exposed rimboard and sill plate, whether a few inches or the whole?
GBA Detail Library
A collection of one thousand construction details organized by climate and house part
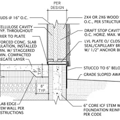
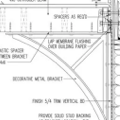
Replies
Jeff,
If you plan to install the SmartSide panels directly to the studs, with no intervening sheathing, then my advice is to purchase the 9 foot panels. You can disguise the 1 1/4 inch of exposed rim joist and the 1 1/2 inch of exposed mudsill at the bottom with metal flashing. If you do this, you'll still need to pay attention to air sealing in this area.
The alternative is to have a horizontal joint between 8-foot panels and strips of siding that are only about 13 inches wide. (You see this type of horizontal joint all the time on houses with T-111 siding.) This type of horizontal joint can either be near the bottom of the wall or near the top of the wall; it must be flashed with Z-flashing, and it will look cheap for the life of the building. This type of horizontal seam is also difficult to air seal. If you decide that the horizontal joint would look better near the top of the wall, you need to install horizontal blocking at the seam.
Needless to say, if you have any questions about bracing or engineering, talk to an engineer.
Thank you very much, Martin.
Jeff,
How deep are your overhangs and what is your roof pitch? You may find the 8'-0" panels extend up high enough for the top to be covered by the soffits. Then you could use a strip of regular sheathing above to tie the walls to the top plate.
Thank you, Malcolm. If I were installing soffits, your idea would be an excellent solution. With a 2' overhang (4:12 pitch), they're expensive and a lot of extra work, so I've opted for exposed truss tails.
For anyone making a similar decision,with walls braced adequately against racking, but wondering about connections from the roof to the foundation to resist uplift:
2012 IRC 602.3.5 Braced Wall Panel Uplift Path gives three options for handling uplift loads:
#1 is the basic connection requirements laid out in 2012 IRC 602.3(1), which require a relatively small wind upliflt load.
#2 installing approved uplift framing connectors to provide a continuous load path from the top of the wall to the foundation.
#3 wall sheathing and fastneners ... designed to resist combined uplift and shear forces.
APA's Revised E-510 says that structural sheathing provides uplift and shear resistance that eliminates the need for extra hardware such as strapping, The strand-based type of SmartSide is rated as structural; the fiber-based is not.
In my case, even the 9' SmartSide won't reach all the way from my top plate to my sill plate, so it alone would not provide adequate uplift resistance for options 2 or 3 above. If it reaches from the top plate to a couple of inches above the sill plate, straps between the sill plate and the rim board might complete the load path. (I'm not an engineer; this is just what I've gleaned from reading.)
The WFCM has a Table A-3.4 of nailing requirements for uplift straps, but it starts at a wind speed of 110 mph, and it doesn't say whether speeds below 110 should be considered as if they were 110. It does say that straps,if needed, should be 20 gauge, 1-1/4" wide, ASTM A653 Grade 33.
Is your rim sawn lumber?
No, it's LVL.
That is the good answer. If it is LVL it can be used in cross grain tension. You can use the LVL to splice the shear panel siding. You could Install the siding from the top plate down to the rim. Then add a finishing piece from the rim to the sill plate. Using the 9' panels. This will provide blocking needed at the horizontal panel joints for uplift continuity from the sill to the top plate and shear anchorage for the floor & walls system to the sill plate.
Thank you, Tim. Are you sure such a thin strip (3" or so) of the sheathing is strong enough? I know it would be very weak in other directions, but I would expect it to be stronger in the relevant direction here.
It will be nailed on all edges at at least 6"oc. to solid lumber behind it. The 3" strip is ok in that it has blocking at all edges. Make sure to used the proper flashing at this horizontal joint. Draw it out and have the inspector approve it before installation.
Thank you very much, Tim.
deleted