Heating and Insulation: A million different answers to the same questions

Hi all- I recently purchased a small Tudor (1300 sq ft.) built in the late 1920s on Long Island. You probably know where this is going, mostly un-insulated house with oil fired steam heat in need of upgrading. I’m luckier than most in that I have a heating contractor in the family who is going to help us with a gas conversion and switching away from steam. Everyone has a million different answers to the same questions all with different biases and I’m having a hard time sorting through it all and was wondering if you lot could help illuminate a solid course for me to continue on.
Heating:
The system my relative wants to put in would consist of a gas fired, very efficient hot water boiler with an indirect tank for domestic hot water use. He’d create 5 zones utilizing as many of the existing radiators as he can (properly tested obviously since coming from steam) and add a few baseboard or radiators in the now unheated basement (potentially a ductless mini split system for basement for coolingdehumidifying but TBD).
Insulation:
Making use of the NYSERDA financing (New York state) program I was going to have everything insulated to as much as made logical sense. I’m the kind of guy who goes a -little- beyond what most people consider necessary but just understanding what most people consider necessary is hugely complicated. The leading contractor now is telling me he only wants to put 2″ of closed cell foam in the attic turning it from an unconditioned vented attic space to an insulated one. He insists that anything beyond 2″ is an absolute waste.
In the basement he wants to put 2″ of closed from spray from the joists down to the floor, again saying that more than 2″ is completely unnecessary.
On the first floor he’s telling me to not dense pack a single thing. He’s saying plaster walls from the 1920s with some kind of decayed insulation likely in there already, there’s no way to get an efficient dense packing in there. The correct way to do it, which he advised against it as being not cost effective, was to completely remove the plaster, spray foam the cavities and reseal it back up. In this scenario it would be something I would do over the course of 10 years myself instead of right up front.
Understanding I’m going to have a lot of stuff open that I won’t have for another 20 or 30 years at a minimum, am I making the right choices? Are there other items I should be looking at? If I had 20 million dollars I’d have the greenest home on the planet but I’m not and need to be sensible. I can afford to go a little beyond, but nothing insane. Thanks in advance for your thoughts!
GBA Detail Library
A collection of one thousand construction details organized by climate and house part
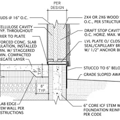
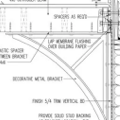
Replies
The closed cell spray foam argument that "... more than 2" is completely unnecessary..." should be read as "...more than 2" is completely not cost-effective...", at 17-18 cents per square foot per R. Cellulose & fiberglass are less than 1/4 the cost. R12-R13 is WOEFULLY below code-min for roofs/attics in US climate zone 4A (all of L.I.). The most you can safely install in one pass without a cooling/curing period between lifts is also 2", which is why that's magically "all you need", according to some contractors. But with R12-R13 foam on the underside of the roof deck you can safely add up to ~R28 in fiber below (and in contact with) the foam without creating a mold farm in your climate zone. How deep are the existing rafters?
In the case of the foundation, IRC code minimum R for new construction foundations is R10 continuous insulation, which means 2" of 2lb foam will get you to code-min. But going to R15 using cheaper methods has a long term financial rationale.
Sounds like he/you haven't even taken a look to see if there is any wall insulation, or what the wall's material stackup is from the interior paint to the outdoor air. DO figure that out, but wall insulation is definitely not to be ignored. (Though spray foam is one of the most expensive solutions.) It's usually possible to blow fiber insulation from the exterior without screwing it up, with only some minor siding repairs to deal with later. If that's vinyl siding blowing it full of cellulose is completely safe. If it's wood clapboards with leaded alkyd paint there may be some work to do there. But re-siding is going to be a heluva lot easier to deal with than gutting the interior, and if the plaster is in decent shape, keep it! (My house is 9" wood clapboards w/ horsehair plaster on the interior, built in 1923. I dense packed it with cellulose without messing up the walls about 8 years ago. There was some exterior paint failures in some areas due to the inability of the clapboards to dry toward the interior, but stripping those areas and applying a vapor permeable stain has held up well.)
Closed cell spray foam is one of the LEAST green ways of insulating, due to the HFC245fa blowing agent used, which is a powerful greenhouse gas (~1000x CO2). LaPolla makes an HFO1234ze blown 2lb foam which is much lower impact, and the smaller player Aloha Energy (up in Albany NY) makes a 1.8lb water blown closed cell foam, as does Icycene (though Icynene's 2lb water blown goods run only about R5/inch.)
On the heating front, if you're going to micro-zone the hell out of it be sure to use one of the cheaper stainless steel 10:1 turn-down ratio modulating condensing boilers such as the WBRUNG 080W / UFT-080W, or the Navien NHB-80, any of which can modulate down to ~7500 BTU/hr out, and make sure there is sufficient radiation on each zone that the zone can actually emit 7500 BTU/hr at an average water temp of 125F or less. The WBRUNG 080W costs the same or less than a small non-modulating cast iron boiler, and SHOULD be cheaper to install too. It's enough boiler for 19 out of 20 houses in the US, and more than your house needs (even the "before" picture, but it's low min-modulation levels makes it a great choice for a 5 zone modestly sized house.
James,
You wrote, "The leading contractor now is telling me he only wants to put 2 inches of closed cell foam in the attic turning it from an unconditioned vented attic space to an insulated one. He insists that anything beyond 2 inches is an absolute waste."
In your climate zone (Zone 4), the 2012 International Residential Codes requires a minimum of R-49 for roofs or ceilings. Two inches of closed-cell spray foam only provides about R-12, so your contractor is wrong.
Your contractor is half right, inasmuch as achieving R-49 with closed-cell spray foam is very expensive. But there are better (smarter, cheaper) ways to achieve R-49 than with 100% spray foam.
Here is a link to an article that describes all of the different ways you might achieve R-49 in your roof assembly: Creating a Conditioned Attic.
To D Dorsett:
1) The rafters are 2 x 6 (actual 2" x 5.5"). There is 32" in between the ceiling and the peak of the slope on the second floor, a few feet of sloped wall and a knee high area of unconditioned space (see attached picture for room on second floor). Contractor was talking about putting an air handler in the space above the ceiling but I do have an alternate spot for it if we think there's an insulation concern we can address with that space.
2) The basement is 3 feet above grade, 5 below, what are you suggesting for the basement? Elimination of closed foam in general and moving to something else or supplementing the closed foam with another more financially viable product? I also want to make sure I have a vapor seal incorporated into any of this.
3) The exterior walls are painted load supporting brick masonry, I was told due to this, it wasn't entirely feasible to get at the walls from the outside. With your plaster walls, did you find it was completely worthwhile dense packing those areas? Do you wish you gutted and foamed at all?
4) What's a good resource for me to read about greener spray foam alternatives? What are the practical implications of going this route from a financial standpoint?
5) There's a Wells McClean Ultra modulating, condensing, whatever boiiler that was sized for 5,000 sq. feet that took a mild amount of Sandy damage that we're going to refurb and put to use in the basement. He says it makes no difference that the boiler is oversized and can do some crazy amount of BTUs, the modulating condensing whatever will only make what it needs. If for any reason we can't refurb that we're going to go with a Lochinvar Knight Boiler KBII-I-O or something. I'm very ignorant when it comes to boilers so I welcome any input you have on either of those optoins heh.
To Martin Holladay:
Thanks Martin- What do you say to people who say, "forget the R value, it only matters with older products, closed cell foam is a different ball game?"
Apologies, forgot to attach photo.
The smallest W-M Ultra (the -80) is ridiculously oversized for a 1300' house, and only modulates down to 16,000 BTU/hr-in/15,000 out. If you tighten up the house you won't have a heat load for the WHOLE HOUSE of 15,000 BTU/hr until it's colder than 25-30F outside. If you break it up in to five zones you'll short-cycle the thing into low efficiency and an early grave unless you add a buffer tank.
If it's any of the bigger Ultra models it'll need an even bigger buffer tank- it's just not worth it.
Lochinvar makes some tiny boilers that modulate down to the same range as the UFT-080W or NHB-80, but they're twice the price from distributors, and unlike the UFT, Lochinvar demands that the system be configured primary/secondary , doubling the pumping requirments. (They void the warranty if pumped direct.)
If you can get a mid-winter or late winter fill-up slip from the prior owner or real estate broker with a "K-factor" stamped on it we can estimate the where-is-as-is heat load now. I'd hazard it's somthing like 30,-30,000 BTU/hr @ +15F now, but would be ~15,000-17,000 BTU/hr with relatively modest thermal upgrades.
With 5.5" rafters hit it with 2" of closed cell foam on the roof deck, and add R15 rock wool under it and NO INTERIOR VAPOR BARRIERs, only gypsum board (painted or not). That will have a center-cavity R of R30, and will be flush with the rafter edges. When it's time to re-roof you can then consider putting 3.5" polyiso nailbase panels up there to bring it up to code. At 2" closed cell foam is about 0.5-0.6 perms, which is low enough to protect the roof deck from wintertime moisture, but high enough to have a reasonable drying rate the rest of the year.
Either 2" of 2lb closed cell foam or 2" of foil faced rigid polyiso would be adequate for the basement. Keep the cut-edge of the polyiso off the slab or it can wick moisture. Fire rated Dow Thermax would not need to be covered for fire safety, all other foam solutions would, though intumescent paints would be acceptable protection in some jurisdictions. Are you planning to finish the basement?
Is there any air gap between the brick an interior, or is it plaster & lath on furring set directly on the brick witn only a miniscule space?
As for greener 2lb foam:
http://aloha-energy.com/spray-foam-installers/
http://www.lapolla.com/foam-lok-2000-4g/
http://www.lapolla.com/request-free-spray-foam-insulation-quote/
James,
Q. "Martin, what do you say to people who say, 'Forget the R value, it only matters with older products -- closed-cell foam is a different ball game'?"
A. I say several things:
(1) You are ignorant about R-value. (More info here: Understanding R-Value.)
(2) You are ignorant about the science of heat flow.
(3) You are ignorant about code requirements.
OK, maybe I don't actually say those things. But I think them.
For more perspective on this debate, see It’s OK to Skimp On Insulation, Icynene Says.
A) Regarding the WM Ultra, it’s even worse than you think. It’s not an 80, it’s a 230 he thinks. He says that I could heat the entire block with it if we wanted to. He’s not concerned about short cycling because to him, it’s a free boiler so he’s not worried about the lifetime. When I told him what you said his initial comments were, “it sounds like this person knows what they’re talking about, I’d love to talk to this person because it’s so rare, maybe I can give them business” (the guy has 30 trucks and he still thinks like this) and then followed it up with, “look, I don’t know that I’m doing the right job there, it’s a massively oversized unit, all I know is I have an almost perfectly new $4500 modulating, condensing boiler and I’ll always be around to service it.” Is your point here that the savings on the boiler will not be worth it in the end on lost efficiency and additional needed gear? If the upshot is I just need to buy a bigger buffer tank but I’ll still have realized great efficiency while saving 4 grand, isn’t that a win?
B) He also wanted to know if you took into consideration the domestic hot water use when you postulated your BTU demand. He’s taking into consideration the current size of the radiators, additional radiators for the 800’ basement, feeding an indirect tank for domestic hot water and he also sizes to 0 degrees which from my understanding is much colder than what most other people size systems for. His argument on the 0 degrees is that we live in New York and we have 10 days or so a year when it does in fact get that cold.
C) I’ve lived in the house for the entire 2015-2016 heating system up until this point. It was a mild first half of the winter and an average second half of the winter and we’re at a K-factor of 4.3 burning 8-1200 gallons of oil.
D) The basement is already finished, but dated. We plan on taking the attached basement (picture & floor plan, same outline as first floor), taking out the paneling, drywalling over the insulation and taking down the ceiling and painting it. This is approx. 50% of the basement pictured with the other 50% on the other side of a wall.
E) What’s the best way to determine how much space is in between the brick and the lathe? Plaster is one of those things that I feel like I’ll never full understand in terms of what’s standard and what’s not.
F) Thank you so much again for all your help, do you have any contractors you’d recommend or other resources you feel like I should be utilizing to help make my decisions?
Peak BTU demand for hot water is rightly met by sizing the indirect hot water tank, not up-sizing the burner. Unless you're planning on filling a 200 gallon spa multiple times a day you won't be needing the Ultra 230.
Dropping the design temp to 0F instead of +15F takes your likely pre-insulation heat load from 35,000 BTU/hr to maybe 50,000 BTU/hr. So what?
That's still 25,000 BTU/hr of boiler output to spare with an NHB-80 or UFT-080W.
In the post Spanish Influenza era of the 1920s it was standard to size heating system so that they could heat the place with all of the windows open. That resulted in ridiculous oversizing and sweaty humans with the windows closed. People dealt with it in two ways, often combined:
A: Paint the radiators silvery or bronze low-E paint, cutting their output by about 15%
B: Cover up the radiators with a grilled cabinet to slow convection, cutting output by even more.
Bottom line, big old radiators are GREAT for condensing boilers since they can deliver the heat at low enough water temperature to actually condense. If the plan is to re-use the existing rads by re-plumbing them for hot water instead of steam, the system and radiators needs to be pre-treated with something to help rid it of accumulated rust, but it should work just fine. The high water volume would usually have sufficient thermal mass that it wouldn't short-cycle the boiler, even though the Ultra 230 would basically never modulate, only cycle, since it's min-fire output would be higher than your load at 0F. You don't up-size the mod-con to be able to deliver higher temperatures with the oversized radiation, since that just reduces it's modulation- it only hurts efficiency. The ideal is to have a modulation range so that under outdoor reset control it will deliver long, nearly continuous burns with very stable room temps.
With enough big fat radiators on each zone the Ultra 230 will condense without super-short cycles, but it wouldn't be able to modulate (much, if at all)- it's minimum input is 46,000 BTU/hr, which at 95% efficiency would be about 43,500 BTU/hr. Your WHOLE HOUSE load after fixing up the place will be under 30,000 BTU/hr (under 20,000 BTU/hr if we can figure out the walls), and each individual zone would be a fraction of that. The beauty of a boiler that can modulate down to 8000, BTU/hr -in/7500 BTU/hr-out is that it can track the load, and deliver continuous burns even with just one zone calling for heat (if there is enough radiation on that zone.)
A K-factor of 4.3 means it covers 4.3 degree days of heating (base 65F) per gallon. A gallon of oil has about 138,000 BTU of source fuel energy, and it's unlikely that a ridiculously oversized steam system is delivering better than 75% efficiency, but let's call it 85%, since that's as high as it could ever possibly be with perfectly sized brand new boiler. That means of the 138,000 BTU (x 0.85) only 117,300 BTU went into the house per degree day. So if at 4.3 degree-days per gallon, the house only takes in (117,300 / 4.3= ) 27,279 BTU per degree-day.
With 24 hours in a day, that would be ( 27,279 / 24 =) 1137 BTU per degree-hour. That's your absolute highest worst case (higher than reality) heat load constant.
With base 65F and a design temp of +15F (which IS the 99% temperature bin for almost all locations on L.I.) you have 65F-15F= 50F heating degrees. So the implied load would then be
1137 BTU per degree-hour x 50F= 56,850 BTU/hr @ +15F
...if the system were actually 85% efficiency. A more likely 75% efficiency would imply a load of 56,850 x 75/85 = 50,162 BTU/hr (probably still high, but not crazy.)
At 0F you'd have 65F heating degrees and an implied load of 1137 BTU per degree-hour x 65F= 73,905 BTU/hr @ 0F, which is still within the output of a UFT-080W or NHB-80.
Reality is probably still under 73,905 x 75/85 = 65,210 BTU/hr @ 0F
For a house that size to have a load that high means it has INSANE levels of air leakage and absolutely no insulation. If it's the original 1920s boiler (or even 1950s-60s boiler) with a retrofit flame retention burner it's actual efficiency is probably in the 50-55% range, which would put the implied heat load closer to the anticipated mid-30s @ +15F
To figure out the wall stack up, find few places such as closet or cabinet on an exterior wall where you can drill a hole in the wall with a 1" hole saw to do the inspection without worrying too much about making a perfectly cosmetic repair of the hole. You may or may not need a boroscope to get a better look at it. With a 1" hole you can both see if there's planking or other sheathing between the brick and the plaster wall, and you can insert a tape measure to measure depths. If there is wood sheathing, use a 1/4" drill to make a hole in the sheathing and use a piece of wire as a depth gauge to figure out how much space there is between the sheathing & brick. You can usually tell if there is an asphalted paper or some other WRB on the exterior of the sheathing. If it's a 2x4 wall with some insulation of some type in it that should become obvious too.
Seal any holes you make in the sheathing with a dab of expanding can-foam. You can plug the holes in the plaster & lath by caulking-in a gypsum board plug (made with the same hole saw) pushed in about 1/4" behind the finish surface, then once the caulk is set, use plaster of paris or some other quick-setting mud to finish over it before painting.
James ,
Please don't take this out of context . While you have a plumber in the family thatis willing to help you with the work , you may want to look the gifthorse in the mouth and have something better installed that is not so oversized .
I am a plumber and heating designer / installer and was at one time as ignorant as 95% of the heating specialists out there . What Dana stated about the Ultra being far oversized is correct . If you truly want to do this properly you MUST have a room by room heat loss performed , a survey of the existing radiation and whether it is sufficient or too large for the room it serves and any new emoitters must be sized properly . Your 90%+ AFUE Ultra as all other mod cons MUST utilize low water temps to achieve that kind of efficiency . The idea of running 5 zones magnifies how over sized the boiler is considering more than 2-3 zones at a time will ever be calling . Your boiler WILL short cycle itself to death in short order and the efficiencies you experiance will hardly be better than an old fashioned cast iron boiler .
Don't be taken in by the National Grid programs either . almost 100% of the guys performing installs under that program are installing a Burnham ES boiler and an HTP SuperStor , and they are doing them poorly I might add . Ask your relative if he would be willing to help you with a designed system that will achieve what you want . Find that designer / installer , compensate him to perform heat loss and optimize everything .
fact of the matter is this , if you do the envelope stuff right , you will not even need a boiler as you or your relative know them and you'll be able to install a real quality system for much less that will last . Although I am in Jersey I can put you in touch with the right folks in LI .
I would love a good contractor recommendation, Richard.
There's a lot here to digest and explore, especially from you Dana, I'm going to circle back around and come up with a new plan and share, thanks guys.
BTW: Today I learned that the guts of the UFT-080W boiler is manufactured by Kiturami (a Korean boiler manufacturer) and that the same series is under the tin of a few combi-boilers out there (Laars Mascot, Noritz CB series). So far as I know only HTP / Westinghouse are offering the 80,000 BTU/hr version, which is a much more appropriate size for space heating in most homes. The combi-boiler vendor opt for the bigger burner versions to be able to deliver reasonable hot water performance in cold-water areas without needing an exterior tank, but their higher minimum-modulation rates makes the larger ones less attractive for space heating, especially on micro-zoned systems.
It seems Kiturami and Kyungdong (Navien) are getting into the North American market using different tactics- Navien is going full out with their own distribution & support network, while Kiturami is OEM-ing the product leaving the distribution & support for their boiler-company customers to deal with. I like Kiturami's fire-tube heat exchanger approach better than Navien's dual finned water tube heat exchanger. YMMV. I alse like HTP's customer support, and would have no problem buying Kiturami boiler under the HTP nameplate for that reason. (Again, YMMV.)
Any progress on figuring out the wall stack-up?
If it turns out that it's lath-on-furring or something with no room for interior side insulation it's still possible to insulate a house like that, but on the exterior. There is sufficient thermal mass in the brick that you could meet current code-min with a continuous 2" / R13 of foil-faced rigid polyiso on the exterior, which isn't too difficult, and wouldn't mess up the interior while it was in progress. It could be done in sections as a DIY if necessary. You would have a diverse set of exterior siding options if you went that route.
John Comerford , 516 - 444 - 8722 . If you contact him , tell him I gave you his number . Very talented heating guy that is more than capable of getting your stuff right .