Health risk of 2×6 wall with 1″ exterior rigid foam, cavity filled, and inteior stud wall strapped with poly membrane?

Hello … I have a quick question on the practicality of the health risk posed by trapping moisture within a 2×6 stud wall cavity. There were condominiums built in our area, 1 which I happened to live in for a few months, that had the exterior walls built in the fashion of having brick (lower units) / stucco (upper units) followed by 1″ of Poly Iso foil faced rigid foam on the exterior with the cavity filled with fiberglass batt-insulation and then they ran plastic sheeting on the interior of this stud wall. When I moved into the condo unit I could fill the fiberglass literally rip into me. We opened the center of the wall up … 12″ gap in the drywall and pulled out the fiberglass batt insulation … which when pulled out was sopping wet … and then proceeded to spray foam the wall cavities with open cell foam. This helped quite a bit but I still couldn’t tolerate living in the building. Is this type of wall construction typical for a 2×6 wall or was this improperly built in regards to building code? The thing is, the rest of the tenants in the building have quite a bit of a parkinson’s shake symptom during the warm summer months, and then their symptoms diminish along with the summer. To me it seems totally improperly built, as it seems to trap the moisture in the wall cavity not allowing it to vent exterior or interior of the wall system. I didn’t know if the state (Illinois) ever regulated such a building code for wall assemblies (this construction dating back to the 80’s I believe), and if the designers of the assemblies are ever held responsible for such assemblies after such a long duration of time …
GBA Detail Library
A collection of one thousand construction details organized by climate and house part
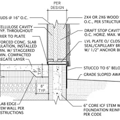
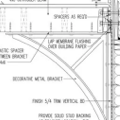
Replies
Jon,
First of all, this is not a medical forum, so it's hard to give advice to your neighbors -- "the rest of the tenants in the building have quite a bit of a Parkinson's shake symptom during the warm summer months" -- except to say, "You certainly need to discuss your symptoms with a doctor."
If you opened up the wall and discovered that the fiberglass batts were "sopping wet," it's safe to say that the building has defects. Fiberglass batts should not be sopping wet.
Here at GBA, we advise builders who want to install a layer of rigid foam on the exterior of their walls that they should never install interior polyethylene. That's been good advice for decades. However, the type of wall you describe did not violate the building codes when it was built.
Illinois has two climate zones: Zone 4 in the south and Zone 5 in the north. In Zone 5, a 2x6 wall with exterior rigid foam needs a rigid foam layer with a minimum R-value of R-7.5. (For more information on this issue, see Calculating the Minimum Thickness of Rigid Foam Sheathing.) While some manufacturers of 1-inch polyiso claim an R-value that high, the actual performance of polyiso in cold weather is closer to R-5 than R-7.5, so that fact may have contributed to this problem.
Bottom line: it's a lousy wall.
It's the moisture trap, not the insufficient exterior R hat created the problem. Without the interior poly sheeting the sheathing would have taken on more moisture than is prudent, and may have even started some mold growth, but the fiberglass would not have gotten sopping wet with R5 foam instead of R7.5.
It is the lack of the ability of that wall to dry in either direction that allows moisture to build up and never leave.
Also, polyiso manufactured in the 1980s was blown with CFHC blowing agents, with much better low-temp performance than post-Montreal Protocol goods blown with pentane. I'll bet it's still performing at better than R6, and could even be R7 at low temp.