Has anyone worked with ISO from Insulation Depot?

Was wondering about experiences purchasing re-claimed insulation from the Depot. I can get a truckload of 3″ full sheets of ISO. Will I need to cut new edges and will it be full of holes? They’re finishing a job in Chicago the the price for shipping to Appleton, WI is good.
Thanks,
PK
GBA Detail Library
A collection of one thousand construction details organized by climate and house part
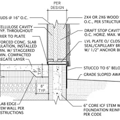
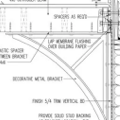
Replies
Ask Them. Reclaimed is not new. It's reclaimed. Your labor goes up, material cost down. What else would you like to know?
You use spray foam to fill voids by buying froth packs or can foam. Most of the foam may be in perfect shape except for attachment holes from prior use. Put bad edges in window cut areas.
If you want perfect foam, buy new.
Paul,
I'm assuming you are talking about polyisocyanurate (polyiso).
I interviewed architect Jesse Thompson on this issue; you can find his remarks in my article, Visiting Energy-Smart Designers and Builders in Maine.
In that article, I wrote:
"Jesse stripped the old siding off the house and covered the wall sheathing with 6 inches of recycled polyisocyanurate purchased from Insulation Depot, followed by vertical rainscreen strapping and new siding. ... In a comment posted on a Q&A page on the GBA site, Jesse shared some lessons learned from his project. He provided the following advice to anyone thinking of installing recycled polyiso on their walls: “Try very hard to have all penetrations (dryer vents, boiler venting, ventilation, etc.) planned for, installed, taped and sealed before adding foam. ... He also lamented the difficulties of installing polyiso of inconsistent thickness. “We had sheets of salvaged polyiso vary by up to 1/4 in. over a 48 in. sheet, which meant the strapping need to be shimmed before siding, which was slow and tedious. In fact, if I was doing it over, I would probably specify salvaged EPS foam instead and use thicker layers to make up for the lost R-value. Salvaged foam can be very affordable; we've skinned a house 4 in. to 6 in. thick for only $2,500 in foam.” "
I have. Here's my take:
http://www.finehomebuilding.com/item/23460/patricks-barn-insulating-with-garbage
I've seen reclaimed foam from foam reclaimers that was as nearly perfect and consistent as virgin stock with perfect edges & corners and few holes, and I've also seen goods that were pretty beat up or compressed. I've also seen mixed-lots that were a combination of 3" and 3-1/4" stuff (as well as a few pieces of tapered foam- which may have been part of Jesse Thompson's lot) that makes it a bit more awkward to deal with. The more beat-up stuff is usually priced accordingly. All lots will have some scrappage rate of more damaged goods, but in general most of the reclaimers are pretty good about not shipping pure junk. I've never felt ripped off by any of them, but the sample size is small.
Insulation Depot (now Nationwide Foam Recycling: http://www.nationwidefoam.com/index.cfm ) is just one of a handful of reclaimers in my neighborhood, but are pretty up-front about what it is. They all deal with multiple types of foam, not just polyiso. It's not clear that the thickness consistency or lot-consistency issues are readily solved by going with EPS, as Jesse Thompson seems to be thinking- EPS manufactured with different tapers for flat-roof applications are as common as tapered polyiso, and it's often a pretty subtle taper, sometimes subtler than the 0.25" per foot code min slope requirements for flat-roofs (though that's also a common taper applied to roofing foam.)
But in a Chicago location in an exterior sheathing application location there may be performance reasons for making at least the outer layer of foam in a multi-layer stackup EPS rather than polyiso, due to the severe performance hit polyiso takes when the average temp through the foam is in the 30s F or lower, and the performance uptick seen by EPS at those same low temps. Two layers of 2" of each, with the EPS on the exterior is likely to outperform an 4" layer of either, on an annualized basis, since the EPS "protects" the R value of the polyiso layer at low outdoor temps. (Unfortunately there is no easy way to model this.)
At a 25F mean temp through 2" of EPS the EPS delivers about R9.2, whereas replacing it with 2" of polyiso would yield about R7.5. But theslightly warmer inner layer of the stackup would still be delivering R10-ish if polyiso, but only R8.8 if EPS. As the outdoor temp rises the polyiso performance rise quickly to over R11, and while the outer layer EPS performance falls to about R8.4. With EPS on the outside of polyiso in a 2"/2" stackup you get pretty much ~R20 performance across a range of outdoor temps, whereas with 4" of polyiso-only you take bit of a performance hit during the coldest weather when you need it the most.
See:
http://www.buildingscience.com/documents/information-sheets/info-502-temperature-dependent-r-value
Note the section at the bottom where they recommend:
"Use a hybrid insulation approach – install cold temperature-tolerant insulation over top of the polyisocyanurate insulation to increase the mean temperature of the polyisocyanurate."
Patrick: That's a bit of a screwball take IMHO. Cut'n'cobble framing bays is a very different animal than insulating sheathing or roof foam-over, which is what most people do with rigid foam.
"The process is slow, too. With spray foam or fiberglass batts, insulating is normally one of the quickest parts on a construction schedule, but our method of cutting and fitting foam and then spray-foaming the perimeter and seams is slow, slow, slow, especially when doing multiple layers such as the rafter bays."
http://www.finehomebuilding.com/item/23460/patricks-barn-insulating-with-garbage
Seriously? Why would anybody (including me- "Guilty, yer honor!" :-) ) ever do it that way?
And why would you think that's what Paul is going to do with it?
My mantra is normally, "Save the high-R foam budget for the exterior, where it's performance isn't robbed by the thermal bridging of the framing."
While there's a place for cut'n'cobble for those with more time than money, it's not something that makes any sense when paying burdened labor costs. It's very labor intensive, and the scrap rates are high.
Also note your INITIAL (and still valid for non-cut'n'cobble applications) take can be found here:
http://www.finehomebuilding.com/item/20691/patricks-barn-oh-boy-mountains-of-polyiso-insulation
"I was impressed with the condition of the salvaged material. The company even sent a half-pallet extra—so we don't complain about any broken pieces, I suppose. If the weather is good, we should be installing foam and hanging siding this weekend."
The reclaimed foam wasn't a problem, but your methods/application may have been.
Thanks for sharing folks!
Seven years ago I added 2" EPS exterior to 1960 fiber sheathing and built out the already replaced double pane windows. Still had cold interior walls (2x4) and there's no way to EASILY add to the interior walls. Completely sealed the attic around the perimeter and ceiling areas, then blew in 18" of cellulose on top of the existing 10 inches of fiberglass.
Now I want a warmer wall so the siding comes off once again this spring (whenever the snow melts...) and I'll build out the outside window boxes further and wrap the whole house with two layers of re-claimed offset 3" polyiso. My foam guns will get a workout again but with a small 1,200 Sq Ft. house it's not to bad. I do all the work... after work. That should make for a warmer wall in this old house.
Cheers,
PK
It's screwball of course, Dana. I didn't link to the other blog post, because it was linked in the later posting. And you're also right that the insulation was of better quality and greater in quantity than I would have expected. I'd use it again.
Paul- a couple of comments:
Fair warning- two layers of 3" foam (6" total) gets to be fairly awkward to implement (particularly on walls) due to the very long screws that are required. A total depth of 4" is quite a bit easier. The assembly awkwardness at 5" may be do-able, but even there you're still looking at hitting the 1.5" edges of 2x framing with 7.5-8" timber screws through multiple layers. At some point retrofitting Larsen trusses and blowing cellulose starts looking pretty reasonable. Jesse Thompson managed to do the 6" of foam, but I doubt that was their first fat-foam foam-over job. Anticipate having a bit of a learning curve.
If the stud wall sheathing is not fully air tight &/or the stud bays are NOT dense-packed with a high density fiber the exterior foam may be getting bypassed by outdoor air infiltration. With 2" of EPS and dense-packed stud bays you would be at roughly 2x the whole-wall R of a 1960s type 2x4/R11 wall, and just shy of an IRC 2012 code-min wall for Appleton's US climate zone 6 location. The conditioned space surface of the interior walls shouldn't be all that cold if it's not leaking air into the stud bays.
Appreciate the concern Dana!
I have done 6" before and always pre mark top and bottom stud locations before hand so I know dead center and only miss once or twice on like sized homes. I did open up two locations 20 years ago to fix some poorly done electric circuits and found a lousy fiberglass batt job and I'm sure it's the same way. Interior walls were probably less then R7 to start when we bought the house in 87. I do have some leak fixes yet but a blower door test showed we did well at 50p with 1.1 air changes. Most of the leaks I've fixed since. Remember we have -10F to -20F for 20-30 nights a year so the walls can be cold often. I just don't want them so cold.
I love Larson trusses but for a one man job, it would take forever. I always have a very tight budget but it's all paid for in cash. Solar pays all our utilities so we really have no bills outside a phone.
Wish me luck, and I appreciate all concerns written on this site.
Cheers,
PK
Green Insulation Group is another company that supplies reclaimed , recycled, and surplus product .
They stock a wide variety of products http://www.greeninsulationgroup.com