GPS rigid foam retrofit: moisture accumulation in MN/Zone 7?
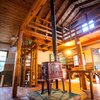
Hi all,
My current plan is the following wall for an addition:
1. High-strength drywall
2. Certainteed Membrain with Pro Clima tape at seams and Tremco acoustical sealant on electrical boxes, bottom plates, etc.
3. 2×6 Tstuds (R20) 24″OC with blown-in fiberglass (BIBS) insulation
4. 1/2″ OSB
5. Wrap (WRB, window/door flanges here) with Pro Clima tape
6. 2″ (R10) GPS rigid foam
7. Rain screen: 2-1/2″ strips of 1/2″ plywood at 45deg for drainage and attachment of vertical siding
8. board and batten-style vertical steel siding
This is attaching onto an existing structure which is conventional 2×6 with R-21 bats, and unknown interior barrier (possibly just 6mil poly?). The addition should be able to dry to the interior just fine. My fear is that the 2″ of foam will be insufficient to protect the sheathing on the original structure from moisture accumulation.
The builder is unfamiliar with these practices, so I am trying to help them as much as possible to research fastening techniques, etc. I see from Martin’s “Calculating the Minimum Thickness of Rigid Foam Sheathing” article that R-15 is recommended for exterior rigid foam in Zone 7. So… should I go for another 1″ of GPS and figure out how it should be fastened? Or is GPS vapor permeable enough that this will not be an issue?
I welcome your thoughts and advice.
Cheers,
Patrick
GBA Detail Library
A collection of one thousand construction details organized by climate and house part
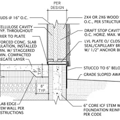
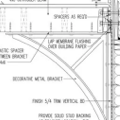
Replies
Hi Patrick.
I'm surprised no one has responded to this yet. This question usually generates lots of opinions.
I was at the Fine Homebuilding Summit last week and, as you can imagine, wall assemblies were discussed quite a bit. We heard from experts who follow the code recommendations (which you read about in Martin's article), experts who don't, and experts who build what some here on GBA consider risky assemblies. Yet they all have monitored their walls, and remodeled them, and have never seen a failure, despite the different approaches. But there was one commonality: they are all hitting very low air tightness numbers verified by a blower door test, or three.
If I were building a wall like yours, and I wasn't working with an experienced architect or builder, I'd hit or exceed the 2018 IRC recommendations for continuous exterior insulation (for thermal performance and dew point control) and either use a smart vapor retarder, as you are planning to, or a class III vapor retarder (painted drywall). And of course, I'd pay great attention to air sealing from the exterior and interior and everything in between.
One more thing. I know that many high-performance architects and builders are using ZIP Systems sheathing very successfully, and I'd definitely use it confidently if it was a good fit for my job. However, based on many success stories (and failures) of wall assemblies that don't have ZIP as the exterior water and air barrier, if I wasn't using ZIP, I think I'd go with plywood sheathing over commodity OSB.
> 2018 IRC recommendations for continuous exterior insulation
There is no such thing. In your Z7, there is an IRC requirement for exterior foam IF you want to use a Class III vapor retarder on the interior side (which you probably don't want to do since it tends to create walls that fail with high interior humidity).
There are some good actual recommendations here.
Consider not using sealants that remain soft and can be pushed out of a joint. Also consider using Drainwrap to reduce retention of unlikely water.
+1 on using taped plywood (vs OSB) and doing a very good job of verified air sealing.
>"Class III vapor retarder on the interior side (which you probably don't want to do since it tends to create walls that fail with high interior humidity)."
Can anyone tell what Jon means by this?
Is he suggesting one should rather use an interior smart vapor retarder? A higher class vapor retarder and no exterior foam? No interior vapor retarder with adequate ext. foam? I can't figure it out...
Tyler, first, Jon is not correct; in the 2018 IRC for CZ7 the prescriptive requirement for walls is R-20 cavity + R5 continuous insulation or R-13 cavity + R-10 continuous. (Unless you follow the U-factor alternative: https://codes.iccsafe.org/content/irc2018?site?type=public/chapter-11-%5Bre%5D-energy-efficiency#IRC2018_Pt04_Ch11_SecN1102.
Where I do agree with Jon is that for zones where class 1 or 2 vapor retarders are required, including zone 7, you can reduce that to a class 3 vapor retarder (i.e., latex paint on drywall) if you meet certain requirements. For zone 7, that requirement is at least R-10 continuous insulation over 2x4 insulated walls or R-15 continuous over 2x6 walls. It is not explicit how they arrived at those numbers, but for roofs they state that the intention is to keep the condensing surface above 45°F, and charting temperature profiles through assemblies shows that the same logic is likely true for walls. The problem is that a surface at 45°F will condense water out of air at 70°F and 40% relative humidity, and the higher the temperature or RH the higher the risk of moisture accumulation.
I'm working on a similar project and questioning the value of using both a Tstud and exterior continuous insulation, but I haven't done the math on it. Did you end up building with this wall assebly?
With the existing house, I would check the vapor barrier and if it does have 6 mil poly I would make sure the exterior insulation is vapor open (rigid mineral wool or wood fiber) to provide a direction for the wall to dry.