Global warming impact of HFCs in CCSPF vs. transportation emissions of rigid foam

The consensus about the global warming impact of HFCs in closed cell spray foam and XPS rigid foam makes it pretty clear that they should be avoided.
But what about the impact of transportation of the material? Rigid foam seems like it must be inefficient to transport around, since it uses up space on a truck/container without really making use of the full weight capacity of those vehicles. Closed cell spray foam is much more compact and space efficient, being compressed into liquid bottles. Perhaps this could change the equation enough that CCSPF wouldn’t be such a bogeyman compared to EPS and polyiso?
(XPS, of course, would not be redeemed by this, since it has HFCs AND suffers from the presumed transportation inefficiency.)
Has anyone analyzed this? I don’t know enough of the particulars of the shipping industry to try and work it out myself. There is also a potential counterpoint, which is that rigid foam tends to be made more locally than spray foam. I believe this is true but I’m not certain.
GBA Detail Library
A collection of one thousand construction details organized by climate and house part
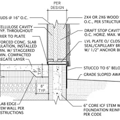
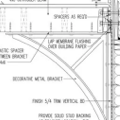
Replies
I've never seen a foam spray truck that was any smaller than a van capable of carrying enough rigid foam for a mid-sized project to the site. It's lugging around the not-insignificant weight of the installation equipment, not just barrels of chemical. The weight of the delivery truck dominates both, but the trucks aren't any different in size.
The long haul transportation energy costs of the bulk material is a function of weight, not volume:
At R4.2/inch 1.5lb density Type-II EPS is 0.03 lbs per R-ft^2.
R7/inch 2lb polyurethane is 0.06 lbs per R-ft^2. That's twice the weight/R of EPS.
R6/inch 1lb polyiso is less than 0.01 lbs per R-ft^2. Even derated to R4/inch for cold climates it beats 2 lb polyurethane on a weight/R basis- it even beats EPS.
Half pound R3.7/inch open cell foam is a hair over 0.01 lbs/R-ft^2, comparable to 1lb polyiso but with a more consistent performance over temperature.
This is a very rough cut, but it's pretty clear that 2 lb polyurethane loses the embodied transportation energy race too, primarily due to it's density.
Care to look at 3.5lb dense-packed cellulose at R3.7/inch, for about 0.08 lbs/R-ft^2?
The transportation energy hit is really in the noise compared to the environmental hit from just the polymers, but the blowing agents are still a real factor.
I guess I was thinking more from a DIY perspective -- the bottled spray foam kits you can buy. A 200 board foot Froth Pak, assuming R-7, is 0.03 lbs/R-ft^2. Why am I getting half of your number?
Is transportation energy cost really just a function of weight, when the material is so low density, like foam, that it can take up a whole truck while severely under-utilizing the truck's weight capacity? You could probably tow a trailer load of foam with a much smaller truck, yet they seem to be hauled around on standard heavyweight trucks/train cars/etc. A truckload of 1lb polyiso only weighs a few thousand pounds, so the weight of the vehicle carrying it is a huge overhead.
I'm not doing the math in my head correctly today (may I have a cuppa joe, please,. or maybe a calculator :-) )
FrothPak isn't 2lbs density, nor is it R7/inch. According to Dow it's nominally 1.75lbs per cubic foot, and R6.1/inch (at only 180 days aging, no telling what it is in 25 years, but probably less than R6.)
A cubic foot of 2lb polurethane foam at R7/inch weighs 2lbs, and is (R7 x 12"=) R84.
2lbs /R84= 0.02 lbs /R-ft^2
A cubic foot of 1.5lb EPS is (R4.2 x 12"=) R50.4.
1.5lbs/R50.4= 0.03 lbs/R-ft^2
A cubic foot of 1lb polyiso is (R6 x 12" =) R64.
1lb / R64= 0.017 lbs/R-ft^2
A cubic foot of half pound polyurethane is (R3.7 x 12=) R44.4
0.5lbs/R44.4= 0.0 11 lbs/R-ft^2 That's half the lbs/R of closed cell foam (but it arrived at the site in the same truck.)
Sheet foam is usually delivered to construction sites in box vans or flatbeds about the same size as spray foam trucks, not tractor-trailer rigs.
Moving freight by rail is nearly ALL about weight, not density. With tractor-trailer rigs density matters somewhat, but not as much as you might think.
But whether moving it around in pickup trucks or tractor trailer rigs, the transportation energy use difference is in the statistical noise. The polymer and blowing agents dominate the total impact, which is why using reclaimed/reused goods like cellulose is greener despite potentially higher transportation energy use.
Thanks Dana. I'll continue to stay away from closed cell spray foam, and aim to use mostly reclaimed rigid foam (so far that's all I've used).
EPS is usually expanded more locally than XPS, so that reduces transportation costs. But that is minor compared to the blowing agent impact.