Getting ready to rebuild basement – thoughts?

So I tore out all the exterior walls in my zone 7 Wisconsin basement. Prior owner had spf framing with faced fiberglass and 6 mil poly under the drywall/panelling. Fiberglass rodent nesting material in sill plate area.
So here is the plan…
Tyvek rolled over top of block wall, down to floor and under the bottom plate.
1 1/2 XPS to make the difference between the 2×6 sill plate and the 10 inch block plus ~2″ overhang. Spray foam to seal those together and to insulate the rim joist.
Then I plan to frame 2 x 6 walls 24 OC 1 1/2″ ( block wall height) short of floor joists. Bottom plate with PT wood . Then, on the block side install the r23 3.5 inch fiberglass paper to Tyvek. Caulk back side for adhering the 2″ EPS foam boards and tape joints with Tyvek tape. Then stand up and secure to the joists with 1 1/2″ blocking. Respray more foam to seal that to prior spray. Can’t do it all at once due to clearance issue .
With the insulation to the back, I can run the electric and other wire/boxes in the clear. Then drywall. Sounds a little crazy, but what are your thoughts?
GBA Detail Library
A collection of one thousand construction details organized by climate and house part
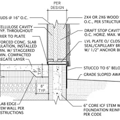
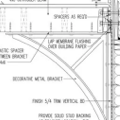
Replies
Do you have a good capillary break between your sill plate and foundation wall?
Mineral wool is less prone to critter nesting problems compared to Fiberglass. I’ve had the same problems with critters nesting in the fiberglass batts in my exterior walls and have been replacing it all with mineral wool.
I would use rigid foam and not batts on the inside of that foundation wall. Rigid foam is a safer option.
Bill
Hi Tom,
I'm a bit confused. Are you using a layer of XPS foam against the block wall and then a layer of EPS installed to the studs before you raise the wall? And what's the purpose of the Tyvek? Seems overly complicated. Check out the illustration and article below:
http://www.greenbuildingadvisor.com/article/how-to-insulate-a-basement-wall
>" ...1 1/2 XPS to make the difference..."
XPS is possibly the LEAST green foam insulation in common use, due to the mixture of HFC blowing agents used, predominantly HFC134a with a 100 year global warming potential of ~1400x CO2. As the HFC diffuse out slowly over a few decades the thermal performance drops assymptotically toward that of EPS of similar density. At full depletion it hits R4.2/inch instead of the labeled R5/inch or the "lifetime" warranteed R4.5/inch ( good luck collecting on that warranty when it drops below that point in 30-50 years. :-) )
EPS is blown with variants of pentane (about 7x CO2 @ 100 years) , most of which escapes the foam and is recaptured. If you're going to use rigid polystyrene in that location, use EPS.
In climate zone 7 the 2" of XPS isn't sufficient dew point control on an 2x6/R23 studwall on the above-grade section of the foundation without use of interior side vapor retarders. TABLE R702.7.1 in chapter 7 of the IRC spells out a minimum of R10 for 2x4 walls, so even at the warranteed R9 a mere 2" of XPS isn't even enough for a 2x4 wall. It needs at least R15 for dew point control on a 2x6/R20 assembly, and with R23 cavity fill it's prudent to install a bit more.
Instead of 2x6/R23 with 2" of continuous XPS, install 3-4" of EPS on the foundation wall, trapped in place by a 2x4/R15 studwall. At 3" even cheap low density Type-I EPS will be at least R11.5, and Type VIII roofing EPS would be R12.5, Type-II EPS would be R12.6. Skip the Tyvek- just tape the seams of the foam board with a suitable air sealing tape.
With 4" of reclaimed Type VIII roofing EPS (R16.7) and a 2x4/R15 studwall you'd have plenty dew point control, and would have much higher performance than the 2" XPS + 2x6/R23 wall, at the same wall thickness.
Since fiber faced roofing polyiso is often more common on the reclaimed foam market it's reasonable to go with that instead of EPS. The only caveat with polyiso is to not allow the exposed cut edges to be in contact with potentially moisture-laden concrete. Leave an air gap or install a 1-2" layer of EPS under the bottom edge to protect it from the slab, leaving a half inch gap between the EPS and wall as a drainage channel.
https://greenbay.craigslist.org/search/sss?query=rigid+insulation
https://duluth.craigslist.org/search/sss?query=rigid+insulation
Reclaimed XPS is also fine- just derate to the fully depleted R4.2/inch for design and dew point control puproses.
>"Bottom plate with PT wood ."
Don't bother. A better bet is to put 1.5" of EPS under the bottom plate as a thermal and capillary break, through screwing the bottom plate to the slab with TapCons. Even pressure treated wood will wick moisture into the assembly creating a potential mold issue. During the summers the slab will be below the dew point of the outdoor air, and so will the bottom of the bottom plate if it's down on the slab. With a bit of insulation between the slab and bottom plate the bottom plate stays warmer and drier year-round. Extending the bottom plate EPS under the wall foam is fine too, as long as the bottom plate EPS has an air-gap between it and the foundation wall.
Sorry, I forgot something. 2 inches of polyiso to 4 feet below grade on outside of block. Using tyvek to limit moisture to wood/insulation. XPS used for less mess while cutting. Only using 3 sheets for the whole project. I can accept the consequences.
>"...2 inches of polyiso to 4 feet below grade on outside of block."
Polyiso should never be in contact with soil, such as below-grade on the exterior side of the foundation wall. Polystyrene works there.
>"Using tyvek to limit moisture to wood/insulation. "
It's doing nothing for you there. Tyvek is extremely vapor permeable, and provides very little caplillary break.
>"XPS used for less mess while cutting."
Cutting XPS is NOT less mess than polyiso:
https://www.finehomebuilding.com/2009/01/29/theres-a-better-way-cutting-rigid-insulation
I'm confused- are you planning to cut'n'cobble the foam board between studs? (A bad idea.) Continuous foam board protects the wood from moisture in the foundation wall, and has a much higher R-value/inch than wood. Installing high R/inch foam between studs is a waste, and impossible to make reliably air tight:
https://www.finehomebuilding.com/2017/07/10/closed-cell-foam-studs-waste
XPS is only for taking up the gap of the 2 x 6 on top of the 10 inch block wall, then overhang to top plate.