Roof Assembly for Garage Conversion

I have some clients in Seattle (climate zone 4c) with a detached 16×20 garage that they would like to convert into an office/craft room/hangout space.
The garage was built sometime in the 1940s, and has 2×4 wall construction with old-school 1x board sheathing for the walls and roof, and 2×4 trusses framing out the roof spaced 24″ o.c. The concrete slab on grade is about 2-3″ below the top of the concrete stem wall.
The plan is to remove the garage door on the east wall, as well as a door on the west wall opposite the garage door (seen in the photos attached below), and infill them with wall space. We are also going to add a couple of windows on the east and west walls, and enlarge the existing door that opens out to their patio to a 6′ out-swing patio door.
For the floor, I’m planning on putting down a vapor barrier on the concrete, and then installing Vinyl plank floor on top of 2x sleepers with rigid insulation between the sleepers. I’m not sure at this point if I’ll have to insulate at the edge of the stem wall.
For the walls, my plan is to install high density batt insulation (R-15) and install drywall for the interior finished surface. Though I may have to furr out the walls to get (R-21).
I’m not sure about the approach for the ceiling.
Roof Approach 1: My thought was to create an attic within the existing truss space. and install a flat GWB ceiling on the bottom of the existing trusses. I’m not sure about the best approach to venting it though: there isn’t really space to get a good ventilation channel from the eaves, so I’d need to use a shingle over edge vent, as well as install a ridge vent. And the attic space is going to be so tight, I’m not sure how easy it would be to install the batts on the floor (though I suppose the contractor could install them before the GWB was installed). Does that make sense? I believe to meet code we’ll have to insulate the attic and vent, but it sounds like from some of the articles I’ve read here that it might be better to seal the attic up tight. So I’m confused.
Roof Approach 2: It would be nice to convert the ceiling into a cathedral ceiling, to have more head height. I’d have to have the contractor install a ridge beam at the ridge, supported on posts. Then reframe the roof with new 2×10 rafters, install closed cell foam insulation to R-49 between the rafters, sheath with GWB, and use a PVA primer/paint. And limit the ceiling penetrations! Thoughts on that approach?
Thanks,
-Chris G.
GBA Detail Library
A collection of one thousand construction details organized by climate and house part
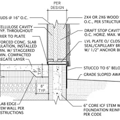
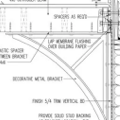
Replies
I don't know nearly as much as many of the folks here so take this for what it is worth:
- A sliding door may be more practical than a set of French doors. Having a built-in screen vs having to add a secondary screen is great.
- The roof seems like a big financial risk in this project. If I were you, I would take a close look at any way to get reasonable ventilation up through the existing eaves, then add vents at the top of the gables or retrofit two vents into the roof (you can add the vents from above without needing any new shingles; much easier than retrofitting a ridge vent.) I'd then put up the drywall ceiling and then blow in insulation after that is installed from one or both of the end gables. If you can get away without touching any trusses or doing any major work on shingles, I think that would be great for the project budget.
- The space is only going to be used occasionally and the Seattle climate is mild. For heat, I'd focus on the ability to heat it up quickly. Get some forced air heat (they make some in-wall electric forced air heaters) and oversize them a bit. That way, they won't hesitate to keep the thermostat very low when they aren't using it and they can quickly warm it up when they need it.
Properly sized gable vents will work just fine with your roof. It looks like low slope, so it might need the larger 1/150 vent opening area.
You can insulate a ceiling like that with batts with either faced or high density. The faced batts can be stapled in place before the drywall is hung and high density batts are usually stiff enough to stay in place on their own. The simplest is what Canada Deck suggests and blow in insulation after the drywall is up. You can do this through the gable vents on both ends.
I think the ridge beam option is way too much work. Besides all the framing, now you have to deal with the point loads from the columns.
If you want a bit taller ceiling, I would suggest replacing the rafter ties with some hold downs (ie HDU2) and allthread rod. Your engineer can spec the exact size and spacing for these. The nice part is you can install the hold downs on the other side of the rafter, put the threaded rod in place, tension then cut the rafter ties. This saves having to shore up the whole structure. Painted white, the tension rods will disappear into the ceiling.
With the shallow rafters, you won't have much space left for venting, so closed cell spray foam is the simplest.
For the concrete floor, you don't want poly. There will always be some small air gap between the poly and the concrete where the humidity will be high and mold can grow.
If you have to deal with slab moisture, the best is to coat the slab with a vapor barrier coating. Most epoxy floor paints and roll on tile decoupling/waterproofing membranes work with this. You can check if you have to worry about moisture by taping a sheet of poly to the concrete. If there is condensation bellow the poly, you have to deal with moisture.