Framers forgot gasket material under an exterior wall

Hey All,
It looks like our framers put up an exterior wall without the gasket material (1/8″ foam) between the bottom plate and the concrete.
Is there a way to correct that without pulling the house/wall apart?
thanks.
GBA Detail Library
A collection of one thousand construction details organized by climate and house part
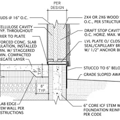
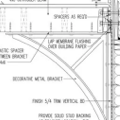
Replies
If the house is still being framed it's not that big a deal to jack it up a quarter inch and put the gasket in.
It's there primarily as a capillary break, which is important to have. It's a lot easier to get it in now than later.
They are still framing--not yet to install the sheathing. It is however anchored with Titan HDs, which would have to be cut in order to lift it. Along with severing links to partition walls. At this point I am glad that I stopped by the site to check something else and noticed it.
The capillary break is necessary to keep water from wicking up and has to be there per code though; correct?
Titan HD can be screwed out.
You'd have to drill new holes but in the scheme of things that's pretty minor.
Thanks DCc - I didn't think about backing the screw out.
Idahobuild, I'm sorry but I can't remember your foundation details. If you have a raft slab or another detail where there is a high-quality vapor retarder between concrete and earth anywhere they come into contact, then you don't need the sill sealer.
Otherwise, there are two relevant sections in the IRC that I'm aware of. R317.1.3 says that sills on a concrete slab in direct contact with the ground needs to be rot-resistant, unless separated by an impervious moisture barrier. https://codes.iccsafe.org/content/IRC2018/chapter-3-building-planning#IRC2018_Pt03_Ch03_SecR317. If they are using pressure treated wood for the sill then the sill sealer is not required.
Table N1103.4.1.1 (R402.4.1.1) says that the junction between the top of the foundation and the sill plate shall be sealed, as part of the air control criteria. It doesn't say with what, and in fact sill sealer doesn't make a great air seal. You could tape or use a flexible caulking such as Big Stretch. https://codes.iccsafe.org/content/IRC2018/chapter-11-re-energy-efficiency#IRC2018_Pt04_Ch11_SecN1102.4
I'm not aware of a code requirement for a capillary break; it's just good practice. Otherwise there will always be some amount of moisture wicking up into your walls.
Thanks Mike. This info. will likely come in handy. Also, the plans call for PT and sill seal.
I didn't think of Big Stretch as an air seal. I could use that and save ths in prosoco fast flash for windows.
You have to be careful dealing with contractors that they not let their problems become your problems. It's OK to ask here to get opinions on how big a problem this is and possible approaches but at the end of the day it's the framer who has to fix it.
DCc - I do feel bad pointing this kind of stuff out sometimes, but in the end we want the house built right AND per the plans. So, I smallow my empathy for the workers and report to GC.
I do really appreciate all the input from this group. The knowledge imparted on me in response to my question in here helps me have more informed conversations with the GC.
I talked to the GC and he talked to the Framing supervisor. Long story short is that the guys working on-site tried to fake it by cutting a section out and stuffing some foam in between the bottom plate and the concrete and stapling some foam to the bottom of the piece that they had cut out. Problem is they stapled the foam to the top side of the section they cut out. As was obvious from the fact that the board would only go back in one way.
I think the GC is now going to make them pull the wall up and fix it. For now he asked them to stop until Monday - when we can all get back on track.
Not sure what I'm looking at in that photo as to why that sill seal is on top or why it's cut, but is that supposed to be a sill plate? Also not sure of the specific requirements for Idaho, but if that's a sill plate then you would use a large washer at minimum and here in the PNW we use the larger 3" square plates to hold the sill down against seismic forces.
Im not sure aabout the raft slab thing. But the foundation and stem wall is in contact with soil.
The Plans do specify PT and sill seal.
Such a basic and major mistake, at the start of framing, does not bode well for the project. I hope you are considering this a warning sign for many more to come.
Things I'd do:
1. Does your project have a comprehensive set of details drawn by your architect? It should. The "project documents" are all you've got to hold over the head of your GC contractually. If you've got an architect involved and the details are not fully documented you should consider getting the package fully detailed by your architect.
2. Do you have a strong technical background in the construction trades? If not, you will likely not see all the mistakes. Consider hiring an independent inspector to check things out on a regular basis as the work progresses.
3. Hold a weekly meeting with the GC to find out what's coming next, so that you can be on top of that and be looking ahead as to potential mistakes, rather than dealing with them after they've been made.
I can't tell you how many times I've seen people show up here on GBA and ask questions like, "We've got the roof framed and now we're deciding how we're going to insulate the attic. Should we yada yada yada?"
The time to decide how to insulate the attic is months before you've applied for the building permit, not after half the work has been done. That's a recipe for disaster.
So look ahead at all the construction tasks coming up and make sure you understand what they are, who is doing them, what possible mistakes they could make, and how to tell if they're doing them right. Very important is to remember how one trade interacts with another. When one trade's "solution" becomes another trade's problem, nothing has been solved.
Thanks.
How do you insulate an attic? Just kidding.
See below for additional info.
Do the plans call for pressure treated sills?
The color of the sill doesn’t look like PT to my eye.
Remember making them do this right now will cost them 10K tops replacing rotted sills will cost you 200k out of your pocket in a few years.
I am beginning to wounder is paying for weekly professional private inspection might be money well spent.
After the faked cut out I would have zero trust in this sub. If the GC seems more upset with you than the sub that would be a big red flag and would require absolutely everything to be reinspected.
Walt
WaltA - the sill is PT -- phone cameras and internet play havoc with color. They are going to fix the issue. We're going to discuss this on Monday with GC and Framing Super.
I do like the idea of the independent inspector and plan to make a couple of calls on Monday.
I am disappointed in the framing crew for trying to pull a fast one and the GC wasn't very happy with them either.
I'm a bit surprised at the comments that seem to imply the job is going to hell in a hand basket. Idahobuild noticed an error on one wall - which was a deviation from the drawings. He brought it to the attention of the GC, who is dealing with it. In the lead up to this build he has posted numerous questions here on GBA, so he isn't uninformed. I'd let things play out a bit more before deciding this indicated much of a problem in the way things are going.
Thanks for all the info and support. I do think that all in the framing sub is doing good work. This wall is an extension of a problem with stem wall squareness. The GC, conc. sub and I talked through solutions. We then presented them to the engineer. I think the framing crew just felt a little rushed in making the change and forgot the sill seal. They just shouldnt have tried to deceive their boss, the GC and I -- very disappointing.
The bottom plate is PT.
The Titen HDs are the engineer approved connector and have a "washer head" according to Simpson. - Addition anchoring and sheer control comes from 20 Simpson Holdowns and Five strongwall panels.
I am going to have an indenpendant framing inspector come and look before final payment to the framing sub and county inspection.
More to come....I'm sure.
Deleted