FPSF question – limited space for insulation

I’m designing the shed, about 100sf, flat roof, zone 6. I’m going to run radiant in the slab for heating. I’d like to do a FPSF for performance of the radiant, in fear of it heaving and mostly because it’s fun.
My major issue being 3 sides of the slab will be on the lot lines and against fencing, so fun things like permiter wing insulation are not possible.
I took a look at an old CMHC guide (attached photo) which recommends a 6″ slab, 12″ deep perimeter footing and 2″ of vertical EPS along the perimeter and in my area 2 feet of wing insulation.
Since I won’t be able to do the wing insulation, one thought would be to increase the the Rvalue/thickness of the perimeter vertical insulation, but even that poses an issue since the more I have to step in the 2×4 walls inward & away from the fence to have it bear on the foundation the less ideal it is.
Does anyone have any design suggestions or experience with this?
Thanks in advance,
Jamie
GBA Detail Library
A collection of one thousand construction details organized by climate and house part
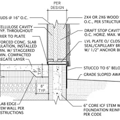
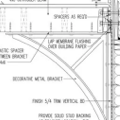
Replies
Jamie,
This sounds like a job you're doing for fun rather than for practical reasons. If I were you, I'd abandon this idea.
If you are building a 10 ft. by 10 ft. shed, why heat it hydronically? Where will you put the boiler or water heater in such a small place -- and why would you want to use the limited space for a mechanical room?
How often will you heat this room -- and why?
A simple space heater is the way to go, in my opinion.
Hi Martin,
Well the shed itself has a practical purpose. Its the slab itself where I'm trying to optimal with.
In terms of heating, the house already has radiant, including exterior radiant for the snow melt system. It is an easy run for me to add radiant in this shed slab being supplied from within the house. Also, from my experience, an electric space heater costs me about $100/month in the winter months, which adds up pretty quick. So the fun part (for me at least) is to optimize for better efficiency and doing the harder thing now for a better tomorrow.
To be honest, my main concern is heaving. I will be putting a deck ledger on the front face of this slab, so I don't want the slab to move around. Pouring shallow slabs and Heaving is something I don't have a lot of experience in, so I thought I'd ask the community in an effort of diligence.
Otherwise I'm thinking I'll just pour a straight 6" thick slab without footings, with 2" of EPS insulation underneath and around the perimeter and hope for the Best.
Thoughts?
Jamie,
Assuming that you are allowed to build right on your lot lines -- that's not always the case -- you can, indeed, build a thick slab (or a thickened-edge slab) and "hope for the best." I've done it, with good success.
The key is to excavate all of the topsoil down to undisturbed subsoil -- you don't want any vegetative matter under the building -- and to install a very generous depth of crushed stone. The crushed stone needs to be drained with a couple of perforated pipes, to daylight.
If you don't have moisture under the slab, you won't have heaving. Ideally, the slab will be slightly elevated, so that the grade slopes away from the building in all four directions.
Soil conditions vary, so there is always the chance of heaving -- but these guidelines have worked for me.
Since you're planning to run hydronic tubing in the slab, you should consider upgrading from 2 inches of rigid foam to 3 or 4 inches.