Foundation wall, mainly

Zone 8, Fairbanks, Alaska. 14,000 HDD (at least as recently as the early 70’s. I don’t know any more; seems more like 10,000.) Part of this design was shamelessly stolen; the rest was tweaked to my “specs”, for various reasons.
The first photo is a cross section of the foundation wall and footer, with the “general wall” above it. No, this will not be constructed quickly, and no, it won’t be cheap. I know the soil will only take 17 psi and that 25 psi foam should be beyond adequate for bearing under the footer, but I can’t get myself to trust the foam itself. (Moderate seismic activity.) Thus, I’ll be spending $10/sheet extra for the 40 psi stuff.
One question I have is whether or not I need the extra 2″ of foam inside the ICF block, in addition to its own 2 1/4″ and the 1 1/2″ EPS I added.
As for the walls, that design was also stolen and tweaked. The 1/4″ plywood on the exterior (on 2×4) is my idea, as I don’t want to dense pack cellulose into a wall with just a WRB holding it in; another individual builds that way here, and I guess it works. It will be painstakingly drilled w/ a million small holes to keep its permeability high.
The 1/2″ plywood (on 2×6) will be an air barrier (gooed and taped) and vapor retarder. It will also have dense pack cellulose in it.
Another thought I had is that perhaps the treated lumber will shrink less than the KD wood above it, so maybe I’d trim the treated stuff so any shrinking does not pull the plywood off of the KD wood. Over-thinking again?
The Benjamin Moore vapor retarder primer idea is probably not a good one. I don’t want to trap moisture between it and the 1/2″ plywood, so it will probably not be there.
So shoot. Any suggestions?
GBA Detail Library
A collection of one thousand construction details organized by climate and house part
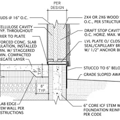
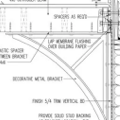
Replies
OK,and crap. I just saw that I posted the outer wall twice. Here is the interior, 2x6 wall.
John,
1) Your outer frame appears to bear on styrofoam. Loadbearing or not, this is not going to work unless there's some truss effect with the inner frame.
2) You have a deep 12.25" space for insulation exterior of the 1/2" plywood, but what about the inner frame? If that's part of the thermal enclosure then maybe you don't need such a deep outer insulation space. What's the target R-value?
3) If the footing were 12" high all the way to the edges, that would be easier to build and would still allow plenty of insulation. Is the terrace shape a waterproofing feature?
4) You could use Homasote or an exterior gypsum sheathing in place of 1/4" ply. That would give a high perm rating without drilling holes. 1/2" DensGlass has a perm rating of 23.
John,
If you are planning to invest in such an expensive foundation, then it would make sense to run the design through the PHPP software (laborious though it is to input the data) to see whether all that foundation foam is doing you as much good as you assume.
Just shooting from the hip, here -- but I imagine that some of that vertical foundation foam is saving you very few BTUs each year. It might make sense to save a few dollars on foundation foam and use the money to buy better windows.
TJ: Thanks for the thoughts. I did not post all the details. I'll respond after the bullets.
1) Your outer frame appears to bear on styrofoam. •• Yes, it does bear, and will only have wall weight on it. Plywood bracing to between the two walls, Larsen Truss style. This is essentially a REMOTE wall, with cellulose instead of foam.
2) You have a deep 12.25" space for insulation exterior of the 1/2" plywood, but what about the inner frame? •• 2x6 will be packed w/ cellulose.
What's the target R-value? •• Extreme. This should be approx 60.
3) If the footing were 12" high all the way to the edges, that would be easier to build and would still allow plenty of insulation. Is the terrace shape a waterproofing feature? •• I was just trying to save on concrete w/ the terrace; probably not worth the hassle, true. Thanks for a second opinion on that.
4) You could use Homasote or an exterior gypsum sheathing in place of 1/4" ply. That would give a high perm rating without drilling holes. 1/2" DensGlass has a perm rating of 23. •• Never heard of either, but they sound far better than my plan. I will check them out. Thanks.
Martin: Thanks. Always good to get your ideas. The foundation insulating is way beyond what I had originally planned, but my "final" design had the problem of 6" of foam hanging out past the siding, requiring huge flashing. This eliminates that problem, but generates a ton of foam. I may slide the wall inward 2" and eliminate that much foam from the outside; that would help. As for the PHPP software, I will try to find someone who has it. It would be interesting to see what assumptions it uses to calculate foundation wall heat loss. I really have no firm handle on that, and, in fact, the heat loss from a SOG, in general, seems a bit nebulous. I don't know if Siegenthaler's equation is appropriate for this type of set up, or if what I did (used Q = U...., but a design temp of 40 F) is more accurate. I'll keep digging. john
John,
Why not leave all of the vertical insulation shown on the exterior of your foundation, but eliminate all of the vertical insulation from the interior of your ICF wall?
Martin: That is the direction in which I am leaning, given feed back; I posted with massive EPS inside, not knowing if it was necessary or useful, and I gather you deem it of little need. My gut says that the inner stuff won't be doing much, as the dirt under the slab will be getting heat from above anyway, so why have more vertically inside the wall? I was not sure, so thanks for the suggestion. Too, I have moved the foundation outward, reducing the exterior foam but keeping the wall 18" deep. I am also looking at floating the slab, which I would like to do. Robert R mentioned that he has not heard of tying the slab to the foundation wall, but most folks here do, apparently for seismic concerns. (I'm seeing a second engineer on that issue.) This is plan B-357. Thanks again. john
Too, I am thinking that 2" under the footer is enough. I doubt that many folks up here put in any.
I should also give credit to where it is due. The concept of exterior foundation foam supporting the exterior wall, though I have tweaked it, is from a discussion w/ Thorsten Chlupp of Reina Properties. Whether or not he would build this way is another issue; I will be.
John,
With all that foam is it neccesary to put the footing down so deep?
If that frost wall were shortened or eliminated, you could still insulate under the footings and the surplus foam clould be used horizontally as "wing" insulation to prevent heaving while saving a bunch of concrete. You would likely, of course, need an engineer's stamp on something like this.
This is what I'll be building for my 10K HDD climate (forgive the crudeness of the drawing):
Lucas: You are probably doing a good deal there. Apparently Thorsten is doing, or plans to maybe do, just that, and his whole system is a lot simpler than my tweaked-traditional style. It has been engineer-stamped, too. A shallow, super-insulated-underneath foundation lacks a 50-yr track record in the Interior, though I guess they are used elsewhere w/ success and I suspect they will work just fine here, too. So I either run w/ an "untested" system or tweak one that has been used for decades, if not centuries. I also see some potential problems w/ DIYing Thorsten's idea, but those may be solvable. Instinct/emotion should not necessarily play a part in building, but it is hard to avoid. Overkill is in my genes, and I KNOW that a deeper foundation will work for 100 yrs. I'm having enough trouble excepting foam under the footer! I can hit faom w/ a hammer and it dents. That is spooky. I like hard iron, man! Contact Thorsten at Reina Properties, and he may be willing to share his thoughts w/ you. His idea looks pretty well thought out, and goes way beyond 4" of foam. Thanks for the input; I may yet give in to this concept......
John, I'm with you on tradition and proven technology. Funny thing is though, there seem to be very few "high-performance" details that have any track record of more than 10 or 20 years. All these fancy tapes holding everything together... I wonder...
Up until a few months ago, I was thinking I'd go with a more traditional style foundation too, just not quite as deep:
https://www.greenbuildingadvisor.com/community/forum/plans-review/19568/detail-directory
I've had to come around to the idea of insulating under the footing. Martin had a good blog entry on the subject a while back which had a part in swaying my POV:
https://www.greenbuildingadvisor.com/blogs/dept/musings/foam-under-footings
The idea for the foundaton detail above came from the architect I hired (shamelessly and crudely reproduced here by me). I've always liked FPSF designs and this one really cuts back on concrete - right now, locally, concrete foundations are being installed for about $800/yd all-in. The plans are all stamped by the architect and his engineer and the local building official didn't even blink when I showed them to her.
Oh, if you feel inclined, you should re-post your details to the thread I linked earlier. It's supposed to be a sort of dumping ground for details that come up - maybe they'll come in handy for someone down the road.
John,
The PHPP software wouldn't be useful for detailing the amount of foam around the footer itself. It would be useful to see the impact of the amount of subslab insulation you use, but it would require you to model all your assemblies and more. You would need to use a thermal bridging software like THERM to understand what is happening locally around the footer itself.
I worked on a Passivhaus design in climate 6. We were hoping to surround the footing with foam but we were building on a sandy slope and our structural engineer wasn't comfortable with it. Our foundation wall was an ICF with additional EPS outboard and subslab insulation. However unlike your detail we extended the ICF wall extended above the slab. The concrete slab was then poured up to the inner layer of the EPS on the ICF form. This way even though we couldn't surround our footer in insulation the basement slab was still isolated from the concrete in the foudation wall by the 2.5" of foam on the inside of the ICF which acted as a thermal break without adding the extra pieces.
Are you familiar with LOGIX ICFs? They come with thicker insulation options.
Lastly I would approach the bottom of your foundation detail as you would an exterior wall i.e. make sure the water shed by gravity has a path of escape downward. Currently you show the sub footing foam extended past the exterior vertical foam. I would recommend flushing this out and extending your water proofing application down to the lowest part of the detail. We used a Sto EIFS below grade product. You should verify if you can apply a bituthane product directly to the EPS.
Hope this makes sense. I'm in a bit of a rush.
The only significant dimensional change with KD lumber that I am aware of is when solid lumber is used as floor joists. Dimensional changes in length and thickness (the 1.5" dimension of 2x) due to changes in RH are negligible.
Because treated lumber typically is sold with a much higher moisture content I would assume the treated is more prone to dimensional shrinkage compared to KD lumber.
Lucas: Thanks. $800/yd? Good God! Is the 'crete laden w/ chromium, or was that a typo? I read Martin's blog about foam under slabs, too, and it also encouraged me to go ahead w/ this, spooky as it is yet.
J Chestnut: My second drawing has the slab completely inside the ICF, as you apparently did. That leaves 2 1/4" of foam to deal with when it comes time for flooring; not sure if that is good or bad. Maybe one could afix a 2x2, buried in foam, at the top of the ICF, just for attaching flooring. Just thinking out loud here about a rug. ??? Yes, the foam under the footer extends outward past the footer to move the isotherm out. Perhaps it is not necessary, or perhaps it should be jointed there, for drainage. I will check w/ a couple folks here. My soil is very dry, and cold. I am not sure how much folks worry about liquid water that far down, but I will inquire. We only have 2 brands of ICFs here, neither of which is Logix. I'll likely use ARXX. Thanks for the shrinkage info. As I understand it, wood posts shrink 1/1,000 of their length, mostly within the first year, but I was not sure what KD wood does across the 3 1/2". I guess I'll scrap the fiddling w/ the trimming plates idea. Thanks for the thoughts. john
John, yes, sorry that was a typo. $600/yd is what I meant to type. This includes site prep, compaction, formwork, steel, concrete and clean-up. I was told this is what to expect - locally - for the type of foundation I'm building. I have several estimates coming to me so we shall see...
Lucas: Oh. With all that included, $600 does not sound quite so bad. Good luck w/ your plan. I think it will work fine, and it seems brighter minds than me think so, too. j
John, I've read and heard that EPS suffers "shrinkage" over time - I've read/heard numbers from 1/2" to 10%. 10% sounds awful high to me. Have you given any thought about how that might affect your foundation design?
Personally I was planning on doing two staggered 2" layers instead of one 4" layer.
J, do you have any experience or comments on EPS "shrinkage"?
Lucas: First, shortening the wall to 24" reduces foam waste tremendously, which had been bothering me. Even going back to 4" (x 2' wide x 40 psi) under the footer, then an adjacent 4" x 2' wide x 25 psi piece (joint for drainage, plus I can shift to 25 psi) under the outer wall, this reduced the foam cost from $26K to $19K, and no scraps. That is a short wall, but at 32" overall I can deal w/ it. As for shrinkage, that is a lingering nightmare, which Is why I designed in 40 psi under the footer instead of 25 psi. The lit says the psi rating is for 1 per cent deflection (not deformation, as I recall), but I have not seen any data on "25 yrs after installation at 25 psi, 25 psi foam shrank xx inches". Thus, this is all on a wing and a prayer at this point. Too, a bit of settling would be OK, if uniform. Oh, sigh.... BTW: Dow Chem was kind enough to send me some samples of their 40, 60, and 100 psi XPS, and I must say the 100 psi appealed to my instincts. "Blue board" is very common up here, so it better not fail. The water absorption data from the EPS industry showed slightly better numbers for their EPS, but I did not dig to see how wet the soil was in their 15 yr study. Dry soil wouldn't be a problem for either one, as far as I can see. I will have to price that 100 psi XPS. If you get any reputable settling data, pls post it here. Thanks. j
Sorry I missed the second drawing. I take it the concrete slab will be your finished flooring. If you went back to the 2x6 for the inner stud wall you might have enough bearing on the concrete to cover enough of the inner insulation of the ICF that your baseboard trim would sufficiently cover the rest. I suspect that 2 1/4" separation vs. 1" would be worth the reduction in thermal bridging. (Again you'd have to run it through a program like THERM to quantify it. Wouldn't it be great if GBA had someone on staff to run THERM simulations of our details! )
I notice your Tu Tuft poly layer vapor vapor is under the sublab insulation. If you placed that above the sublab insulation you can tape your plumbing protrusions to it to help the integrity of the air barrier.
I would also consider a 'flashing' detail around the perimeter of your slab. When I tiled my bathroom recently I included metal flashing under the tile and backed up to the bottom wall plate. The reasoning being that I would rather have any water that reached the floor stopped by the flashing and let stand and soak into the tile rather than working back into the wall (or EPS in your condition).
I was wondering about your first drawing where the slab was tied into the grade beam. If your slab can in fact be independent from the grade beam then you are free to bring the ICF stem wall above the slab if it helps your detailing. It also may help to keep the wood in your exterior wall sufficiently high enough above grade.
Have you considered I-joists to fur out from the interior bearing wall? We were thinking about this for a project but haven't detailed it out yet. From the perspective of your outer exterior wall bearing on foam it might be a better approach.
Concerning EPS shrinkage I've seen the examples on this website of the T&G exterior foam sheathing shrinking. On an EIFS application we did last year exterior layers of EPS were "fully adhered" to the ICF. I don't understand the physics of why rigid foam would shrink but would expect that there could be a difference between a mechanically fastened application and a fully adhered application.
I've read enough about sub footing foam installations that my gut feeling is that is a relatively non-risky detail if the foam has sufficient compression strength. In Europe in order to address thermal bridging they have developed and are using high density foam load bearing elements embedded in EIFS systems. Don't know if this is true but I tend to think with the higher regulatory environment there we can have some confidence in what they are doing (but should be respectful of climatic differences).
Shrinkage...
John, just wondering...
If your plan is to do "air-tight" sheathing, why detail the drywall with gaskets/tremco?
J Chest: Again, thanks. As far as I've been able to gather (seeing, doing w/ various others around, and reading) the VB should go under the foam that is under the slab. Penetrations are detailed before the foam, pex, wire/rebar go in. Your flashing is an interesting idea. I've not tiled a floor, but don't they have vertical pieces w/ curved feet just for that reason? The EPS shrinkage is something I better check into. Here is my latest foundation wall, based of feed back from various sources. The 100 psi XPS occurred to me last night; maybe a 2x8 bottom plate is in order there???? I may also bump to 60 psi under the footer; it'll only cost $400 extra. As is, (if a retired math teacher did his arithmetic correctly) the 100 psi XPS area is "tougher" than the 40 psi under the footer. Keep the suggestions coming; I'm all ears. john
Lucas: thanks for clarifying the shrinkage direction of the EPS. I will inquire about that. As for the sheet rock gaskets, I figured "why not?" Isn't it always better to keep conditioned air in the conditioned space till the HRV gets it? That is my reasoning, for better or for worse. j
I lied. See http://www.epsmolders.org/4-cval.html for some details. It is "psi at failure or 10% deformation". Dimensional stability of 1.5%. Interestingly, but not surprisingly, the water absorption goes down quite a bit as the density goes up; another good reason for higher density under slabs. I have emailed a few places for info on shrinkage over life-time; will post what I learn. Read Martin's blog comments, too. j
It would be interesting to hear about what you find.
John, seems like you are a fan of the "belt, suspenders and extra pants underneath" approach ;-)
Lucas: Overkill is in my genes. When it appears, at least, that it is simple and cheap to overkill, then I do. I can't see where trapping/stopping air could hurt, as long as the barrier is vapor open. SOW, I think it was the Dow web site that mentioned that foam can creep under load, so to prevent that they recommend "a ratio of 3:1 for static loads". (For dynamic loads it is 5:1.) I assume that means that if you have a 10 psi static load, use 30 psi foam. That is one question I will be looking into, and the answer may lead to 60 psi foam under my footer. Again, that is only another $400, so WTH?
John,
If your lot is large enough, consider the option of extending your "wing" insulation to 20feet, eliminate the foam under slab. It will become similar to John Haits' PAHS style. With good windows and enough solar input, you won't need any shade at your location. All the soil under your slab and wing insulation becomes your thermal storage...maybe an extreme thought for your climate. Just a thought for consideration.
you won't need A/C for sure.
Harry: 20' W? Holy chit! I'll have to google that guy. Yes, I don't know how that would pan out w/ soil permanently in the 30's after about 5' down. I'll have to do some thinking. Thanks for the idea. While I am typing, I have been calc'ing the load on that 100 psi foam, and it may not work. I will be visiting an engineer Wed, and one question will be how the load is transferred through that bottom 2x8 plate, and also what effect the plywood and sheet rock will have on distributing the roof load farther from the stud, along the bottom plate. I will need a bit of help there, because if the load is concentrated w/in 1.5" of the stud (my assumption) it will be too much for the foam. I'd sure like to not have any slab touching the foundation wall much, but an ICF guy here said to NOT pour the slab inside the ICF completely, but rather over the top of it, floating or tied in w/ rebar. More to think about. And, no, we have never needed AC in 30 yrs, but now and then it actually gets up to 90 F!
Here is a chart I got from the InsulFoam web site, and I just spoke w/ a guy there who does a lot of the testing. He recommends staying in the 1% to 5% deformation range, as that is w/in the foam's elastic limits. When you approach the 10% (advertised) deformation load, you start to get permanent compression. This explains the "3:1" rule I mentioned above, approximately. I have no idea why foam is not advertised by its 1% deformation rating; that would sure make things more obvious to end users. j
OK, it's a done deal. I spoke w/ an engineer today, and he, too, could not see how to make the 100 psi XPS under the 2x6 wall work. It's just too iffy. So, back to setting the slab inside the ICF's, and moving the 2x6 wall inward 1 1/2". Ya think 19" of DPC is enough? I am 99% sure I will use 16" OC studs instead of 24", as I think that is legal with a one-ton/lf load and double top plates. It is nothing, too, to add a 2x4 every 4' to help catch the "middling" truss, if need be. So now it is on to other topics. BTW: Both foam reps explained the linear stability of their foams, and as we all use them it is a non-issue; tiny fractions of an inch. What IS important, though, is sticking to the 1%, or at most 5%, deformation load. Done deal, and IFQ on this. Thanks for the opinions and info, everyone. john