INSOFAST foundation insulation

I am about to start building my house with a basement. I originally planned to spray 2″ of closed cell foam on the basement walls and stud out the wall for drywall. I saw a product INSOFAST with insulation panels that I could potentially install myself. So that would be a significant cost savings during the build. Is the INSOFAST panels comparable product for performance and reliability to the closed cell foam and is it worth the money savings versus closed cell spray foam? Is there any drawbacks to installing the panels? Also, do I need to add any extra vapor barrier to the concrete wall if I go with the INSOFAST panels?
Thanks!
GBA Detail Library
A collection of one thousand construction details organized by climate and house part
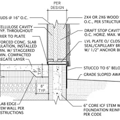
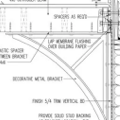
Replies
Any EPS (including that product) is fine to use on the interior side, and somewhat GREENER than closed cell spray polyurethane. You'll still need to seal the foundation sill and band joist with appropriate sealants.
To meet code minimum in climate zones 5 and higher takes 4" of EPS. Their UX 2.0 would only meet current IRC code in climate zones 1- 3. Zone 4A/B requires R10 minimum zone 4C and 5-8 need the full 4" to meet the performance levels of R15 continuous insulation.
According to the specs it's 1.25 per cubic foot (=Type VIII) foam:
https://www.insofast.com/resources/insofast-insulation-panel-specifications-details.html
Type VIII EPS typically has a vapor permeance rating of 3.5 perms max @ 1", which would be 1.75 perms max @ 2", which is tight enough to not need another vapor retarder, as long as the interior finish wall is more vapor open than that. Standard interior latex on wallboard runs 3-5 perms, which would be fine.
To meet code in higher climate zones you'd still need more foam, or a fiber insulated studwall snugged up to the EPS, in which case standard sheet foam would be cheaper. So it's really a product best suited for zones 1-3.
Is there any risk of moisture getting in the wireways or gaps in the insulation causing mold? One complaint I saw had that issue with the INSOFAST product.
You would need to air seal any opening to all of those raceways in the panels. You don’t want air to be able to move from the inside of the room to the concrete wall.
3” polyiso, (reclaimed if possible), taped seams and horizontal 1x4 screwed to the face will work better. You can run wires on the warm, dry side of the foam. Any foam option will need drywall or 3/4” plywood in front of it for fire protection unless you use a rated polyiso like Dow thermax.
New houses tend to have a LOT of water to get rid of during the first several months. If you can, you might consider finishing the basement walls until later, and just plan on running a dehumidifier in the basement until next winter.
I have used Insofast a few times and I like it... but I do not think I will use it again. (Like Dana said) I came to the conclusion that you need a framed wall anyway to get to code (Zone 5), so why pay extra for there system. For the future I would use EPS sheets glued to the foundation and tape the seams. Then frame a wall to fill with fiberglass/ mineral wool.
Another angle to consider is that you don't get a chance to plumb and straighten the foundation walls w/ Insofast. In my 1960 house the wavy out of plumb walls were transferred to the drywall. Even more of problem where I was tiling the wall for a shower.