Foundation and slab questions

Owner/builder SFR new building in zone 5 (6200′ above Reno). On a 17% south facing slope with somewhat friable bedrock varying from 1′ to 4′ below ground level. 1000 sq.ft. garage slab on grade with stepped footing/stemwall foundation. 1200 sq ft two story house with stepped footing/stemwall crawlspace foundation.
The building inspector has already given the ok to drill into the bedrock and connect the stemwall directly to the rock where it can’t be dug with the backhoe.
The footing is 16″ wide, 7.5″ tall, with 16″x16″ steps about every 10′ or so to go down the slope. The stemwalls are 7.5″ wide and vary from 16″ to 48″ tall, the max height to avoid engineering.
Can this footing stemwall system be poured monolithic? With the footing forms having open tops? Was thinking it could be poured in lifts with the first pour/lift filling all the footing steps, then the footing, then the stemwalls in two or three lifts. I’ve seen contractors pour footing/stemwalls all at once but not on a slope with the steps. Seems like a good option to avoid the cold footing to stemwall joint in a seismic/high wind zone. Would have a concrete pump truck to do this.
It’s just kind of scary to try and get the slump correct. Helping my neighbor pour his slab in two parts on two different days and two different slumps made the work dramatically different.
On the slab want to put 1-1/2 of EPS underneath and then a 12″ square grid of #4 rebar. Want to be able to drive a 6500 lbs Bobcat on it and bring in some heavy machinery (10,000 lbs?) with a forklift. Was thinking of going to a 5″ thickness? The 12″ square seems good for the pour, so you can step in the holes while working it, compared to the 8″ woven mesh. Could this dimension go to 16″ square?
My neighbor completely eliminated the rebar in his slab just going with the small fiber reinforcing, but I thought this was only to control drying cracks?
Should I go with the budget Home Depot EPS? That does say it’s rated for under-slab. Or something with a higher PSI rating?
There is also some fill under the slab, up to three feet in depth. Should this be building sand, or should it be road base?
The only other thing that seems problematic is how do you set up a screed edge on the slab when the footing/stemwall is already poured? The stemwall will be up to 4″ higher than the slab, and slab is sloped to drain toward the garage doors. You could do the slab in two parts which would give you a center edge. But the edge at the wall is the issue. The only DIY info I’ve found is to hand trowel an edge during the first part of the pour. Seems like one of those things that’s going to be difficult on a first time, one time basis.
GBA Detail Library
A collection of one thousand construction details organized by climate and house part
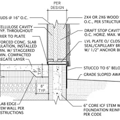
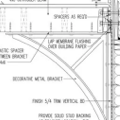
Replies
Hi Chris -
pretty complicated project and post. It sure sounds as though you need local expertise; you are not the first landowner in your neck of the woods who has had to figure out--or pay a professional to figure out--your approach.
One thing I can tell you: check out the EPS Industry Alliance technical information on compressive strength of EPS by Type: http://epsindustry.org/building-construction/compressive-strength.
Peter
Chris,
We pour most of our foundations monolithically. That's made easier because most builders here form with boards, and use a 2"x4" on the top of the footings which helps contain the concrete. Much like this: https://www.alibaba.com/product-detail/concrete-plywood-forming-strip-tie-snap_60009926741.html
The upsides as you say, are increased strength, and a savings in time, labour and pump fees. The downsides are a capillary break isn't possible, and the forms can move a bit vertically if not well-staked.
The one situation that sometimes makes builders here do two pours are steps in the footings. Depending on how deep and how many, it is sometimes easier to pour them separately. Yours sound pretty simple. I'd be tempted to p0ur all at once, but if it's your first time, you might want to err on the side of caution. You can easily make up for any loss of strength by making the footing an wall rebar continuous.
for the floor I've been told to use adjustable height chairs to set a piece of round pipe so the top surface of the pipe is even with the finished floor surface.
use the pipe to screed, then slide it towards you, filing in the groove as you trowel or float the floor.
Re: slab design: I was involved in many industrial projects with heavy loads. Many of them did not have steel reinforcing in the slab, however they weren't over insulation, and they all had some degree of control joints and design to transfer loads at the control joints. Varying amounts of fill. I'm not an engineer. You'll need to bring in a graded gravel or stone (same as road base) that can be compacted, and install it in 8" lifts, compacting each lift, paying attention to moisture content. You'll need a decent size machine for compaction. Insulation will probably need to be high psi XPS made for plaza decks, etc. My guess is you'll need at least a 6" slab, maybe more. You'll need to plan crack control with sawcuts or other and then plan for transfer of loads across joints. A 10,000 pound machine may put most of its weight on the front wheels when fully loaded. Maybe a discussion with an engineer is in order.