Footing for stem wall in shallow trench with crumbly soil

Here in central Arizona, the concrete footing for a 24″ stem wall for a small house need only reach 12″ below grade. My plan was to dig a trench 16″ wide and slightly more than 12″ deep and use the soil as the form for a footing 12″ thick, with enough margin at the top of the trench to keep the concrete from spilling out. Code only requires the footing to be 8″ thick, but the extra 4″ will cost me roughly as much as another course of concrete blocks for my stem wall, and given how slow I’ll be in laying blocks, 4″ more concrete is much easier, and losing 4″ of height compared to another course of blocks isn’t a problem, as my crawlspace will still be tall enough for me to get around.
As it turns out, though, my silty sand soil is too crumbly. The bottom 2/3 or so of the trench still has vertical sides, but the top 3-4″ has fallen in so that the profile of the trench is sort of a Y with a fat stem. I have thought of two possible solutions:
1. Build forms out of OSB (or plywood) supported primarily by the walls of the trench, but held from falling inward by 1×2 stakes nailed to the outside of the OSB. Strips of OSB 8′ long x 1′ high would be held by stakes 4′ apart that would penetrate deep enough into the soil to keep the OSB vertical. The stakes would be pressed into the walls of the trench so that they don’t create a gap between the soil and the OSB. I would tap the forms to a depth where their top edges would be a uniform 1-1/2″ higher than I want the top of the concrete to end up. I would make a screed board with a 2×4 that would just fit between the forms attached to a longer 2×4 that would slide along the top edges of the foms so that the 1-1/2″ thickness of the 2×4 on its underside would screed the concrete at the proper level.
a. Does this plan make sense in general?
b. I understand that plywood would be better than OSB overall, but it’s twice as expensive, and In this dry climate, I can pick a week when it will be sunny throughout, so the OSB won’t be in danger of getting wet before the pour. I will, however, need to remove it and the stakes after the pour. Will I need to coat it with something to ensure that I can remove it?
c. The trench was overdug in many spots. Am I correct in thinking that with the OSB pressed against the walls of the trench, a few inches of exposed trench-wall soil at the bottom won’t cause trouble, such as concrete creeping up the outside of the forms, to any significant extent?
2. Instead of building forms, a possibly far-fetched idea would be to mix some of my silty sand with Portland cement to make soilcrete that I would use to restore the top few inches of my trench to a vertical profile. I would make the soilcrete thick enough that I would get the fallen soil that made the top of the trench look like a V to stick back in place where it came from. I have no idea whether soilcrete would be sticky enough to stay put, but perhaps someone else has tried this. Option #1 still has the major advantage of making it easy to screed the concrete to a level top, but this second option would be a lot less expensive, as the amount of cement I would need is small, given the high soil-to-cement ratio in soilcrete (from what I’ve read). Does this idea have any potential?
GBA Detail Library
A collection of one thousand construction details organized by climate and house part
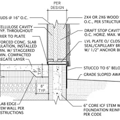
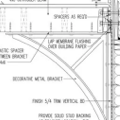
Replies
Jeff,
Widen your trench and use standard forms. That approach makes a lot more sense than fooling around with OSB forms supported by stakes in crumbly soil.
If you know what you are doing, widen your trench and build your own forms out of plywood. That approach works -- I've done it for two foundations -- but you need to make sure that you understand how sturdy the forms need to be, and you need to understand the forces that can cause form bulging. The forces are stronger than you think.
Lots of things can go wrong with a concrete pour. If you don't have access to re-usable concrete forms, and you don't have enough experience to build your own forms, you may want to hire a concrete contractor.
You say the top 4" of a 12" trench has collapsed. Unless there's something here I'm misunderstanding you still have 8" of vertical sided trench. If 8" is the required depth of pour, you're good to. Far easier, cheaper and quicker to lay an extra course of block than form the entire footing.
How about form the footing AND stemwall out using 2x lumber, pour the whole thing at once, skip the block entirely, then use the lumber for framing the house?
Yes, David's suggestion makes good sense too. If you're going to the trouble of forming, take it all the way.
I'd also suggest talking to your local inspections department. Assuming that this soil condition is not unique to your lot, local builders will have encountered this issue before and likely figured out the most cost-effective fix, and the inspections dept will know what they have approved.
Thank you, Martin, James, and David. The alternatives you suggest are good ideas I considered carefully before devising my plan for a form. My budget is too tight for hiring a contractor, and I don't know enough to be confident of avoiding a disaster if I try to pour the footing and wall at once, although the idea is quite tempting. I also considered revising my plan to have just an 8" footing, but given how slow I will be with blocks and how quick the type of form I propose here would be, plus the ease of screeding with the form, the form remains preferable--unless there's something with a significant chance of going wrong that I'm not seeing. Martin mentions bulging, but I don't see how that could happen with the soil walls flush against the outside of the OSB. I will fill in the last few inches of soil behind the top of the OSB so that all of the OSB has a solid backing. The stakes are only there to keep the OSB from falling inward while the concrete is being poured; the only forces of any magnitude will push outward. Is there anything specific you can see going wrong with what I propose?
I really don't think OSB is a good form material. We usually use 1-1/8" form plywood and it has to be well-supported everywhere, otherwise it bulges out. The risk to you is not so much that your pour will be mis-shapen (although you get highly-sought-after style points for crisp, straight, smooth, flat concrete even if it's buried!) but that the OSB will get trapped between the concrete and the soil and will be a huge headache to dig out. The last thing you want are trapped form boards, ever.
The other advantage of over-digging and forming is that you can install your footing drains immediately after stripping forms, and then backfill. If you don't do it this way, you have to excavate next to the footing to install drainage. I know a lot of people just pour in a ditch and don't install drainage, and I guess maybe you can get away with it in a low-rain area with well drained soil. It would be a huge mistake here in Washington state...
Forms for mono-poured footings/walls are easy to do. You use 2x lumber from your framing package, form ties, 1x2 wood stakes, and duplex nails. Well within the range of a careful worker who is not under time pressure. I can post photos if you want.
Don't worry about the sides not being straight. Get the bottom width required. The trench has to be inspected before the pour. The top width is not important. The cost of materials and labor to dig the trench wider and form it will be far more than the cost of the extra concrete. Common sense needs to be used here. I've poured hundreds of feet of footing trenches that were not formed. Unless you have lots of money and time to waste, just pour it! As far as screeding: pieces of rebar in the trench with the proper grade on it will assure a level surface. Use a 4' screed made of 2" material. Attach a handle made of other 2x's and pat the surface of the footing to the top of the rebar. It has to be close to grade and close to smooth to prevent having to use an inordinate amount of mud to level the first course. Even if it is rough, you will have the first course level and ready for the second course before you got done digging the trench wider and constructing forms before pouring the footer. If you can, go watch a professional concrete company pour an unformed footing. You will feel more relaxed about the task yo have ahead of you.
Thank you, David. A drain isn't needed here. Getting the OSB out after the pour was my biggest concern and why I asked about coating it in my original question. I would love to do a mono-pour if I could; yes, please post photos.
If I stay with my original idea, how about covering the trench side of the OSB with inexpensive polyethylene to keep the concrete from wetting the OSB and sticking to it? Then, the only thing holding the OSB in place after the concrete hardens would be friction with the soil on the outer side. I would think I could pull the poly out fairly easily after I remove the OSB, as there would be 1/2" or so of space there and few things stick to poly, or I could leave it in place.
Thank you, Quentin. My concern about the concrete fanning out a few inches at the top of the footing was that the building inspector would think those projections would be vulnerable to breaking, but they won't be carrying any load, and they will have soil underneath, so perhaps not; it helps to know that you don't think the widened top is a concern. I also liked the idea of the form making screeding more foolproof, but it sounds as if you think it will be reasonably easy anyway. The building official said I would have to remove, before the concrete hardens, any vertical pieces of rebar I would use to determine the top of the footing, and rebar is more expensive and harder to cut than 1x2s, so before I came up with the form idea, I was thinking of using 1x2 stakes along the sides of the trench with markers for the correct height. The BO approves that idea as long as I remove the stakes. Would that work well?
Jeff,
Even if you don't decide to pour the footing and wall monolithically, it might still be a good idea to use framing lumber for the footing forms. If you intend to use CMU's for the walls it is very important that the top of the footing be level, or you will be fighting things from the start.
The beauty of the system David has suggested is it can be done on uneven ground with a sloped footing. All that matters is that your pour strip is level at the top of the wall forms.
Thank you, Malcolm. If I used framing lumber, would covering it with poly to keep it clean and prevent concrete sticking to it make sense? The mono-pour is a very attractive idea; I look forward to seeing David's photos, and I'll do some more research on it. My previous research indicated a fairly large risk of it going quite badly if one isn't experienced, but I might have gotten a poor sampling of opinion.
Jeff,
We pour all our walls monolithically, even for full height basements. Because it is a common technique here we are able to rent the vertical bars used to contain the dimension lumber used for the forms. To the south of us in Washington State many builders use the same metal strapping as lumberyards use to secure their loads instead. Without the bars you need some way to compensate. For short walls, we just use framing, but at two feet high there is a fair amount of horizontal force during the pour. I agree that calls for a fair mount of framing experience to guarantee the pour goes smoothly.
We don't cover or treat the 2"x8"s we use for footings. We strip them after two days and knock off the half-cured concrete. They are fine to frame with, but a bit rough on your saw blades.
Thank you, Malcolm. I appreciate the word of caution, and it's good to know the concrete will knock off the wood reasonably easily.